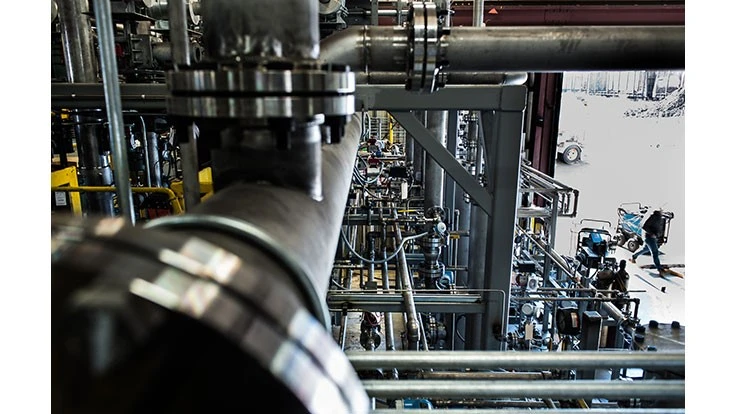
Agilyx Corp.’s “most innovative” facility in Tigard, Oregon, was initially built to convert hard-to-recycle plastics into synthetic crude oil. At one time, Agilyx generated about one million gallons of jet fuel from plastic scrap and received $80 to $100 per barrel. When commodity pricing crashed to $40 per barrel, Agilyx looked to restructure the business and found converting polystyrene back to its basic form for reuse would be both sustainable and profitable.
Retrofitting the facility
While studying its database of chemical conversions and different polymer “recipes,” Agilyx found that polystyrene, in comparison to mixed plastic scrap, is easily manipulated back to a styrene monomer, says Agilyx Chief Executive Officer Joe Vaillancourt.
“As chemical recycling becomes more of a focus of the world--and I do believe that it as a platform technology really has the ability to dramatically increase the recycling rates--it is still chemistry,” Vaillancourt says. “I think people assume that waste, however they think about waste, is not quite as heterogeneous as it is.”
After several successful tests, Agilyx committed to recycling polystyrene (PS) but had to make several changes at its facility to make the venture sustainable and profitable. First, Agilyx uninstalled the back-end cleaning system for fuels and designed one for small scale polystyrene monomers.
“Cleaning various hydrocarbon products is a very different process,” Vaillancourt explains.
Second, Agilyx positioned itself to deal with high contamination found in PS products, such as “tremendous” amounts of dirt and residue in the hundreds of tons of seedling trays Agilyx processes.
Before “qualifying” a waste customer into the facility, Vaillancourt says Agilyx runs various tests on their material to understand the chemical composition, as well as the contamination range. Agilyx has developed a sophisticated program that mixes different customer’s products together to create a “recipe” to produce a consistent styrene base for new products. Today, Agilyx accepts polystyrene from more than 500 waste suppliers.
“For us, we’re excited because it’s the first commercial facility, to my knowledge, in the world that can take a polymer, break it down to its elements and then reform it back into virgin polystyrene,” Vaillancourt says.
Developing the business
After 15 years of converting plastics into fuel, Agilyx has “deep” chemical conversions and thousands of polymer recipes, but it takes more than being a chemistry expert to be economically viable. Agilyx’s facility processes 10 tons of PS per day, which is small scale compared with how much material its partner AmSty, an integrated producer of PS and styrene monomer, processes, so the company has to be strategic about business development and sourcing material.
“Where you’re putting facilities, how big they are, transportation around the feedstock and off-take side, how close you’re integrated with your partners” are all factors of whether the business will be financially successful, Vaillancourt says.
Vaillancourt, who worked for Waste Management for 15 years, says one of the biggest challenges around waste-to-value propositions is the difficulty in accessing the proper amount of quality waste.
“It’s everywhere, but it really is hard to gather,” he says. “We decided to vertically integrate and develop our own sourcing activities.”
Locally, Agilyx partners with waste management company Recology to source PS collected from a residential recycling program. Agilyx also started sourcing material nationally, from single-use PS food trays from school systems in Florida to municipalities in Canada and more than 300 commercial customers.
Agilyx has formed joint ventures and off-take agreements with Texas-based AmSty and Ineos Styrolution, which use Agilyx’s styrene monomer to make food-grade consumer packaging. Because the monomer needs additional refining before use, Agilyx is working with the companies to develop a product that meets American Society for Testing and Materials (ASTM) standards and can go directly into new polystyrene products. Agilyx, in collaboration with AmSty and Ineos Styrolution, is also currently sourcing material for Agilyx's new polystyrene facilities in California and Chicago, which will process 50 to 150 tons of polystyrene per day.
Dispelling myths
Part of growing the business is changing the public’s perception of PS. Ordinances and bans, such as San Diego’s PS and single-use plastic ban, are sweeping the nation. The common misconception is that the material is not recyclable.
“People are concluding that polystyrene is not a high valued polymer because it can’t be recycled,” Vaillancourt says. “It’s just not true. The irony, at least from a chemist’s perspective, is styrene is
The material is often not accepted as a recyclable because of
To help create public awareness, Agilyx is creating circular PS programs. The company recently collaborated with McMenamins, which hosts one of the largest concert series in the Portland, Oregon, area. Agilyx encouraged the brewery to use polystyrene products, such as foam beer cups, at their venue and partnered with a waste management company to collect 2,000 pounds of cups, which have been recycled back into new polystyrene products.
“I think there’s interesting growth despite the negative press on polystyrene,” Vaillancourt says.
Get curated news on YOUR industry.
Enter your email to receive our newsletters.
Latest from Recycling Today
- Recycled steel price crosses $500 per ton threshold
- Smithers report looks at PCR plastic’s near-term prospects
- Plastics association quantifies US-EU trade dispute impacts
- Nucor expects slimmer profits in early 2025
- CP Group announces new senior vice president
- APR publishes Design Guide in French
- AmSty recorded first sales of PolyRenew Styrene in 2024
- PRE says EU’s plastic recycling industry at a breaking point