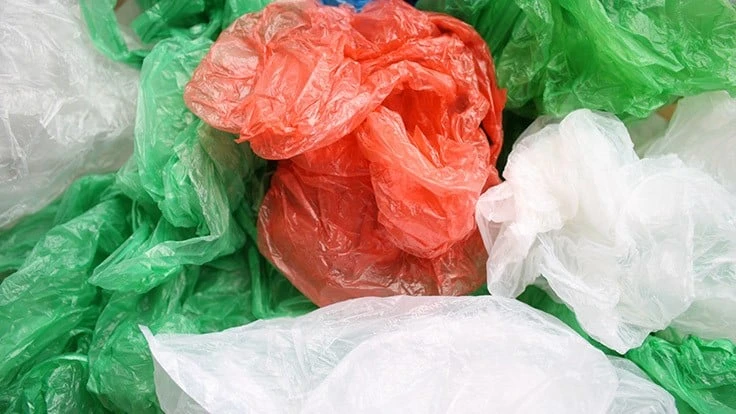
© Daizuoxin | dreamstime.com
The circular economy can be defined as an ideal, zero-waste economy where the materials we use every day follow a closed-loop, circular journey that starts with manufacturing and utilization and then moves into reuse, repair, redistribute, refurbish, remanufacture and sometimes compost. With a circular economy, everything comes back and is used again in one form or another, minimizing or completely eliminating landfills and incineration.
The circular economy differs from the existing linear economy, where things are produced, used and then some things can be reused or recycled, but some things end up in the landfill, oceans or other places they don’t belong. Some types of plastics are especially problematic in terms of recycling, but increasingly, manufacturers are becoming more conscious of the materials they’re producing and using to ensure that they can either be recycled, reused or composted.
In some cases, nonrecyclable and hard-to-recycle plastics are designed and used largely for convenience and for marketing. These items include single-use grocery bags, beverage cups and clamshell packaging made of expanded polystyrene (EPS) that is used by some fast-food restaurants. Ultimately, these packages are designed for customer convenience. They’re easy to use, disposable in the sense that they’re not intended for reuse, and they can be designed with company branding and marketing slogans.
But there has to be a conscious effort to use different types of plastics that can be recycled, reused and redesigned in order to become part of that circular economy.
Because it’s often less expensive to produce and use these types of plastics for products that are only going to be used once, historically the circular economy hasn’t been at the forefront for these applications in light of cost.
But there has to be a conscious effort to use different types of plastics that can be recycled, reused and redesigned to become part of that circular economy.
Manufacturers and marketers aren’t solely responsible for the use of nonrecyclable and hard-to-recycle plastics. As noted, most of these single-use items are designed for the convenience of consumers, and consumers may or may not have a recycling program set up either in their homes or in their communities. For many people, it’s a lot simpler to throw these plastics in the trash. Sometimes it doesn’t matter if the plastic is recyclable or not; it’s a matter of being conscious about recycling.
Circular solutions
For manufacturers, the circular economy can reduce certain costs. For example, in 2020 the Washington-based Association of Plastic Recyclers released a study comparing energy profiles of the environmental burden of virgin resin versus recycled resin. From the study, comparing just the expended energies of recycled polyethylene terephthalate, high-density polyethylene and polypropylene shows the virgin plastic expended energies for these materials are 1.7, 3 and 3 times the expended energies of their postconsumer recycled plastic counterparts, respectively. That is, it takes more energy to produce virgin resin from raw chemicals than it does to create postconsumer recycled resin that can be reused in one form or another. Using more recycled content—which manufacturers may be able to do using their internal processes—rather than buying virgin resin can cut costs and ultimately has a positive environmental impact.

Getting consumers to cooperate can be a challenge, but environmental consciousness already has received significant publicity, and many communities have either legally mandated or strongly recommended participation in recycling programs. Additionally, many product manufacturers who use plastic packaging or containers indicate that the plastic is recyclable. Some cities have banned single-use plastic grocery bags, and some stores sell their own branded, reusable bags or have receptacles for disposing the single-use plastic. Replacing plastic drinking straws with paper ones is one well-known example. Biodegradable “eco-plastics,” formulated from organic starches or from cellulose, are also an option in some cases. Again, it’s a matter of raising and sustaining awareness of the issue.
Get onboard with the circular economy
According to The SustainAbility Institute, London, “Society needs to stop thinking of plastic as 'waste,' but as a renewable resource that needs to be disposed of correctly.”
“Disposed of” are probably not the words to use here, rather recycled, reused or remanufactured. For plastics manufacturers, if plastic byproducts or defective products are recycled internally, there are potential significant cost savings within their own manufacturing process. If not, recycling programs can be set up so that the material goes to a plastic compounder that can turn it into a reusable resin. Always ask the waste haulers who collect the byproducts about where the material will end up to ensure that it won’t be dumped in a landfill. And, in every case, manufacturers can take care that their plastic scrap is properly sorted and that employees are trained to know what to do with it.
While the circular economy might not ever be perfected, there are practices and processes that can be put in place now as at least steps toward that final goal. Plastics manufacturers, those companies who use their products and end consumers can all play a role. The key is being environmentally conscious and willing to do the major and even the seemingly small things that support the effort.
A.J. Dilenno is vice president of commodity managed services at RWS Facility Services, which is headquartered in Chadds Ford, Pennsylvania. Dilenno is responsible for marketing all commodity fiber and resin throughout North America for the company. He also is responsible for maintaining and growing RWS’ national customer relationships with paper mills and plastic resin compounders, reprocessors and tolling companies. He has more than 10 years’ experience in the recycling and waste industry.
Latest from Recycling Today
- Nippon Steel acknowledges delay in US Steel acquisition attempt
- BASF collaborates to study mechanical plastic recycling
- Commentary: navigating shipping regulations for end-of-life and damaged batteries
- Haber raises $44M to expand to North America
- Canada Plastics Pact releases 2023-24 Impact Report
- Reconomy brands receive platinum ratings from EcoVadis
- Sortera Technologies ‘owning and operating’ aluminum sorting solutions
- IDTechEx sees electric-powered construction equipment growth