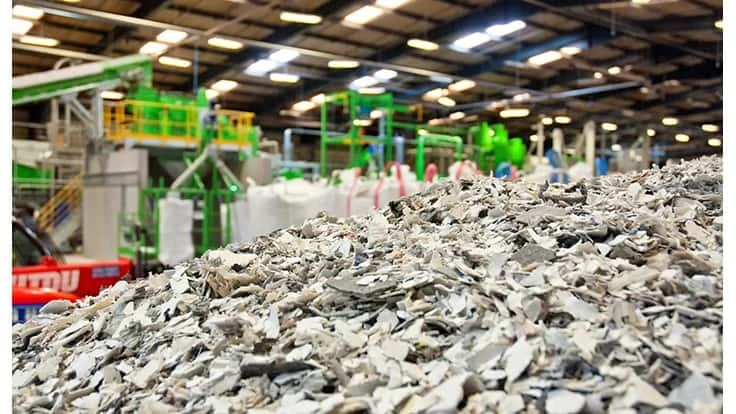
Plastics sorting technology provider Ad Rem NV, a joint venture of Belgium-based scrap recycling firm Galloo, says it has worked with Germany-based Hamos GmbH to develop a mixed plastics recycling system.
The two companies say an installation of the system in Telford, United Kingdom, is designed as a “processing line that handles the complete plastic recycling chain from waste to resource.”
The line in Telford has been installed for an AO Recycling facility operated by online retailer AO.com, which sells appliances including refrigerators, washing machines and dishwashing machines.
AO Recycling and its service provide All Controls were looking for a solution to recycle the plastic generated by obsolete refrigerators. AO and some of its original equipment manufacturer (OEM) suppliers wanted the material to be reused in new refrigerator production, according to an Ad Rem press release.
“There are many different types of waste plastics out there,” says Jelle Saint-Germain, a sales engineer at Ad Rem, who says the refrigerator scrap is part of a larger pool of such scrap in the U.K. and Europe.
“Over 4 million tons of e-waste is collected in the EU and U.K. annually, of which more than 500,000 tons is recyclable polyethylene (PE), polypropylene (PP), polystyrene (PS) and acrylonitrile butadiene styrene (ABS),” Saint-Germain comments. He adds, “Currently, most of those plastics are not being recovered. Of course, this is a tremendous waste of potential resources.”
Ad Rem and Hamos have combined forces to develop a custom-designed process, according to Ad Rem. “We start with the WEEE (waste electrical and electronic equipment) plastics mix and send it through the Ad Rem flotation, operating on a density of 1.09 specific gravity,” says Saint-Germain.
He continues, “To obtain the correct density, we add a patented pH-neutral agent to water. As opposed to the traditional use of salt, this agent does not dissolve into water, but remains in suspension, which enables us to recover and reuse it. It is a cheap substance that does not interfere with the electrostatic separation downstream, which is why this technology is so suitable to combine with the Hamos technology.”
In subsequent steps, the PE/PP is separated from the PS/ABS in a second flotation tank running on water, after which the PS/ABS is separated using a Hamos electrostatic line.
The proposed process has been “vigorously tested” by the equipment companies, says Ad Rem. As a result, AO Recycling has decided to invest in such a plant.
Using the complete technology chain from Ad Rem and Hamos as described, AO is now turning the mix of shredded refrigerator plastics into virgin-quality ABS and PS, according to Ad Rem. The plant, now described as fully operational, was commissioned in October 2019. It processes 4 tons per hour of refrigerator plastics, with a projected total yearly throughput of 20,000 tons.
Ad Rem and Hamos indicate they will continue to fine-tune the process, and Ad Rem says it has sold a similar system to be installed in Japan, where 40,000 tons of plastics will be sorted and processed annually.
Ad Rem was founded as a joint venture between machine-building group Valtech and Galloo. Active since 2008, the company describes itself as a supplier of innovative machines for feeding, treating and separating scrap materials. Penzberg, Germany-based Hamos GmbH designs and builds electrostatic separation systems.
Latest from Recycling Today
- BlueScope, BHP & Rio Tinto select site for electric smelting furnace pilot plant
- Magnomer joins Canada Plastics Pact
- Out of touch with reality
- Electra names new CFO
- WM of Pennsylvania awarded RNG vehicle funding
- Nucor receives West Virginia funding assist
- Ferrous market ends 2024 in familiar rut
- Aqua Metals secures $1.5M loan, reports operational strides