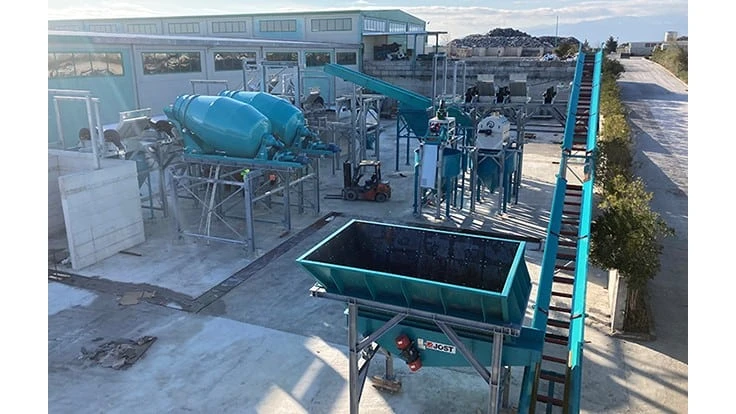
Belgium-based Ad Rem NV is providing technology to a heavy media separation plant in Polykastro, Greece, designed to help separate more than 10 metric tons per hour of mixed plastics and metals from shredded end-of-life vehicles (ELVs).
According to Ad Rem, as of late December, trucks are driving on and off the site of Greek recycling company Konstantinidis Bros. SA, delivering “structures and components of their new separation plant: a Heavy Media Separation (HMS) system, built by Ad Rem, aimed to deal with their automotive shredder residue.”
Ad Rem calls the new plant a high-tech, state-of-the-art installation “doing much more than just separating materials.” The technology provider says the plant’s owner, Konstantinidis Bros., was established in 1971 and is Greece’s largest recycling company.
In 2018, Ad Rem installed what it calls “Scavenger” system at the Konstantinidis Bros. main production facility in Thessaloniki, Greece. The Scavenger is a compact machine, combining several sieving and wind sifting steps, according to Ad Rem.
Using the device, a fines fraction is created, as well as a light fraction that is suitable for waste-to-energy applications. The remaining fraction is called SHF (shredder heavy fraction) and contains all the plastics and metals. Free from fines and light materials, the SHF fraction will enter into the new HMS system.
The HMS system is the result of many years of innovations by Ad Rem and its parent company, Galloo, which processes scrap and operates shredders. Galloo started developing flotation plants for metal recovery more than 30 years ago and continues to do so, now via Ad Rem.
The new plant in Greece includes a washing system designed to comply with local regulations and to keep the sorting media clean, so “the separation process remains stable, and pollutants are concentrated in a single sludge output,” according to the firm. Ad Rem tapped into the knowledge base of Galloo and sister company Trevi Environmental Solutions to design the system.
Instead of vibratory rinsing screens, rinsing drums are added at both output sides of the separation drum, designed to enable cleaning of the sieves while in operation. Not only does this prevent frequent maintenance stops, it also prevents media material losses, says Ad Rem. “By using this innovation, the plant will consume the lowest possible amount of medium, while remaining operational on a 24/7 basis, except one shift per week for cleaning and general maintenance,” the company adds.
A double medium storage system enables the operator to switch the density of the system in a very short amount of time, according to Ad Rem. “This way, plastics can be separated from metals on a lower density, while magnesium or aluminum can be floated from heavy metals on higher densities using the same system.”
The separation drum itself is the result of a study done in coordination with the university of KU Leuven in Belgium. In that study, a computer model of the separation process was created, and the process and drum geometry were simulated for varying circumstances. The results of the study were implemented in the physical design of the plant: When floating aluminum from heavy metals, the misplacement observed in both outputs approaches zero, says Ad Rem.
A patented system was added to extract water from the medium, ensuring “perfect control over the medium density and avoiding the need to add fresh medium every time the density needs to be increased,” Ad Rem says.
A focus on automation means these stages work largely without any operator involvement, says the firm. Frequency drives for most motors and pumps, sensors measuring the tank levels, automatic density measurement help ensure the plant can operate efficiently. “Pump clogging up? The increased current will be visible for the operators so they can unclog it before the system stops. Density dropping? The automatic medium dewatering system will keep it up and stable,” the company says.
Additionally, an interactive visualization and analytics system will store all plant data for years and display it in custom-made graphs.
The plant is scheduled for completion in early 2022, according to Ad Rem, which describes itself has having been founded in 2008 as a joint venture between machine-building group Valtech and recycler Galloo.
Latest from Recycling Today
- BlueScope, BHP & Rio Tinto select site for electric smelting furnace pilot plant
- Magnomer joins Canada Plastics Pact
- Out of touch with reality
- Electra names new CFO
- WM of Pennsylvania awarded RNG vehicle funding
- Nucor receives West Virginia funding assist
- Ferrous market ends 2024 in familiar rut
- Aqua Metals secures $1.5M loan, reports operational strides