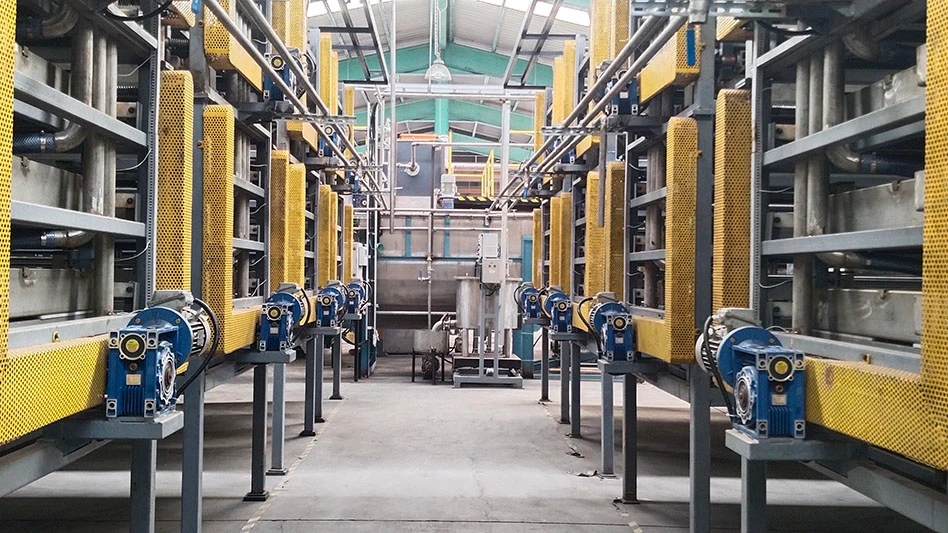
Photo courtesy of ACE Green Recycling
Ace Green Recycling, which maintains offices in Singapore and Bellevue, Washington, has delivered the first of three phases of a proprietary zero-emissions modular lead battery recycling technology to ACME Metal Enterprise at that company’s facility in Keelung City, Taiwan.
As part of the agreement, Ace will provide equipment and hydrometallurgical chemicals to enable ACME to produce “GreenLead,” which Ace says is lead produced in a “safe, sustainable and economical way.”
The technology provider refers to ACME as Taiwan’s leading lead recycler, operating for 40 years. As the installation unfolds, ACME will become one of the largest producers of emissions-free lead, with a capacity to recycle 20,000 metric tons per year of lead batteries to produce about 12,000 metric ton of environmentally friendly GreenLead, according to Ace.
The plant could generate nearly $24 million in annual revenue for ACME, Ace estimates, while not producing any Scope 1 emissions. The Taiwanese facility is the second recipient of Ace's lead battery recycling technology, and on its website, Ace mentions several other planned projects.
“We are excited and pleased to have successfully completed the installation of ACE’s lead battery recycling technology at our facility,” ACME Managing Director Linus P. Lu says. “This marks an important milestone for ACME as we build our capacity to provide sustainable lead recycling capabilities—not just for our company but for the entire lead battery ecosystem as well.”
Lead batteries most commonly are recycled via a smelting process that can involve furnace temperatures of more than 1,830 degrees Fahrenheit (1,000 degrees Celsius) that produces greenhouse gas (GHG) emissions and byproducts that typically are landfilled.
Ace's room temperature, electrically powered hydrometallurgical recycling technology replaces smelting and, according to the company, eliminates GHGs and reduces solid waste by more than 85 percent.
Phase I of the agreement with 2,400 metric tons of annual capacity was handed over to ACME in December 2023, with Phases II and III (which will increase annual capacity to around 20,000 metric tons) scheduled for later in 2024.
“During the 10-year contractual duration, these facilities will enable the recycling of over 14 million scrap batteries,” Ace says, estimating the new process will prevent the emission of nearly 265 million pounds (120 million kilograms) of CO2 equivalent.
Ace an ACME also estimate the Taiwanese processes will provide for the recycling of more than 14,000 metric tons of plastics.
The recycled-content lead produced at ACME’s facility is anticipated to be put back into new batteries made in Taiwan and Japan made by battery OEMs across Asia.
“It is our goal as a battery recycling technology platform to provide all players in the ecosystem a way to meet not just their commercial goals but their environmental ones as well,” Ace CEO Nishchay Chadha says. “We develop our carbon-free recycling technologies to meet the industry’s global aspirations to be responsible stakeholders in the mission of meeting net-zero targets.”
Ace says lead-acid batteries remain an essential component of global electrification, saying they are “a key element in the automotive and telecoms industries, while also playing a crucial role in the energy transition for renewable power storage.”
In addition to its lead-acid recycling technology, Ace Green Recycling also offers lithium-ion battery recycling technologies worldwide.
Latest from Recycling Today
- Radius to be acquired by Toyota subsidiary
- Algoma EAF to start in April
- Erema sees strong demand for high-volume PET systems
- Eastman Tritan product used in cosmetics packaging
- Canada initiates WTO dispute complaint regarding US steel, aluminum duties
- Indianapolis awards solid waste contract, updates recycling drop-off program
- Novelis produces first aluminum coil made fully from recycled end-of-life automotive scrap
- GPR’s hubbIT platform recognized in Georgia State University’s Marketing Awards for Excellence in Innovation