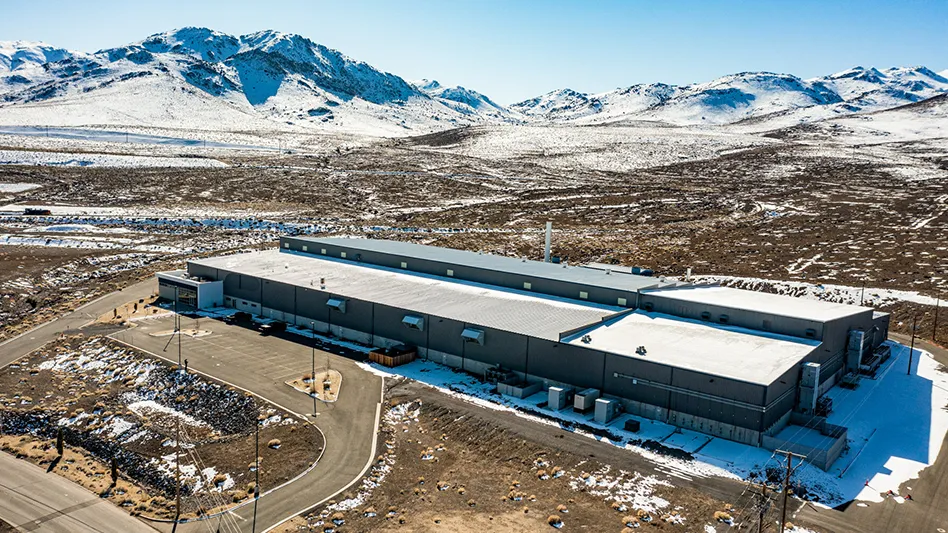
Photo courtesy of American Battery Technology Company
American Battery Technology Company (ABTC), a Reno, Nevada-based recycler of lithium-ion batteries (LIBs), has entered into agreements for the purchase of a move-in-ready, commercial-scale battery recycling facility located in the Tahoe-Reno Industrial Center (TRIC) at 2500 Peru Drive, McCarran, Nevada, to expand operations of its LIB recycling technologies.
According to ABTC, the demand for domestically produced and sustainably sourced battery metals has grown at a high rate in recent years, as the domestic manufacturing capacity of LIBs has grown exponentially from less than 50 gigawatt hours per year to now over 700 GWh/year of operational and announced capacity. The company adds that this rapid growth in demand has been amplified with the passage of the Inflation Reduction Act in the fall of 2022, which includes mechanisms to incentivize electric vehicle (EV) manufacturers and consumers to purchase EVs that source battery metals from domestic manufacturers.
RELATED: ABTC signs $20M term sheet for prepurchase of recycled battery metal products
In what it says is a response to this large increase in demand for its recycled products from domestic automotive and battery original equipment manufacturers (OEMs), ABTC has entered into agreements to purchase the move-in-ready battery recycling facility that will allow it to rapidly implement its internally developed LIB recycling technologies at significantly higher capacity than previously planned.
Covering approximately 137,000 square feet, the facility is currently vacant and was previously used for the recycling of lead-acid batteries and is already designed and permitted for similar operations. ABTC says that while all of the legacy processing equipment has been removed, the plant is already equipped with the necessary infrastructure equipment, including the electrical distribution, HVAC, compressed air, nitrogen, water treatment, material handling, analytical quality control and operational control rooms necessary to implement the company’s LIB processing technologies.
“We are excited to be able to capitalize on this opportunity to accelerate the first commercial-scale implementation of our integrated lithium-ion battery recycling technologies,” ABTC CEO Ryan Melsert says. “The purchase of this existing facility was significantly lower cost than constructing a new facility of similar design, and the fact that it is move-in-ready with the necessary infrastructure equipment already installed will allow us to accelerate our start of commercial-scale operations.”
RELATED: ABTC receives US DOE grant for construction of lithium manufacturing facility
Additionally, ABTC is currently completing construction of its Global Development Center in Fernley, Nevada, where it will develop and validate its battery recycling technologies at the bench scale, optimize them in pilot-scale operations and then construct and operate commercial-scale systems of these technologies to further improve the performance of its integrated battery recycling operations.
Latest from Recycling Today
- Novelis quarterly, full-year net sales down; CEO reports ‘strong improvements’
- Meeting the decarbonization challenge
- Cyclic Materials expands leadership team
- Paper cup acceptance at US mills reaches new milestone
- EPA announces $3B to replace lead service lines
- AMCS showcasing Performance Sustainability Suite at WasteExpo
- New Way and Hyzon unveil first hydrogen fuel cell refuse truck
- Origin Materials introduces tethered PET beverage cap