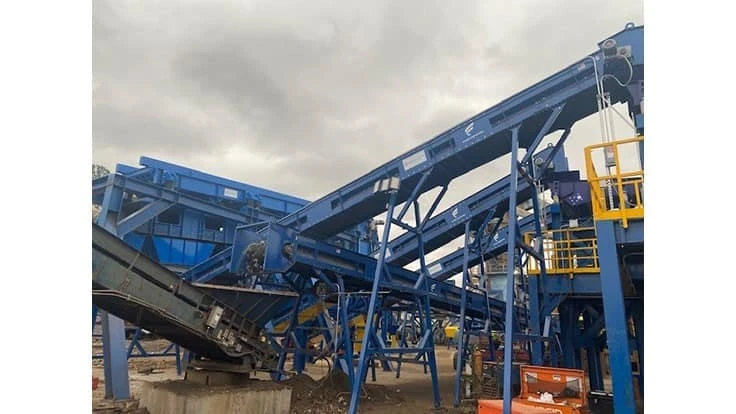
Photo courtesy of ISS
An automobile shredder operator in Statesville, North Carolina, sought to eliminate costs associated with sending automobile shredder residue, or ASR, off-site for processing by adding a nonferrous plant. This would enable the recycler to recover zorba, turning an operational expense into a source of revenue. However, space constraints meant a nonferrous plant based on trommels and high-frequency screens wasn’t possible.
The recycler wanted to make three cuts from the nonferrous line, processing nonferrous material from 4 inches down to less than 0.75 inches, processing up to 35 tons per hour.
Industrial Service Solutions (ISS), Houston, says it worked with Action Vibratory Equipment, Newberg, Oregon, to deliver a plant that eliminated the need for a trommel and fines screen setup and additional handling components, significantly reducing the footprint.
With the nonferrous plant online, the recycler was able to eliminate the cost of handling and trucking its ASR for off-site zorba recovery, ISS says. The expanded capability also enabled the recycler to explore new revenue streams by further developing its in-house ASR processing capacity.
Latest from Recycling Today
- ArcelorMittal puts French EAF conversions on hold
- Associations ask for effective EPR to drive textile circularity in Europe
- GESA report claims 72 countries recycled EPS in 2023
- Report: Saica exploring recycled paper mill project in Dayton, Ohio
- Hydro’s Alumetal to meet 15 percent of its energy demands through solar
- CSA Group publishes standard defining plastics recycling in Canada
- Second Cyclyx Circularity Center to be located near Fort Worth, Texas
- Sennebogen machinery keeps material moving at German recycling plant