But even during the downturn, shredder operators did not take a break from their task of extracting as much marketable metal as possible from each daily output of shredded material.
Even with demand for ferrous scrap down, savvy operators looked for ways to maximize their harvesting of aluminum, copper and other metals for which—even if not at an ideal price—there was plentiful demand.
LOOKING BEYOND THE OBVIOUS
Auto shredders can be explained to casual observers as a way to process automobiles, appliances, and other large objects to produce a marketable grade of scrap iron and steel that can be sold to mills.
But beyond that obvious function, the difference between profit and loss for a shredding operation is usually measured in what is recovered beyond the iron and steel.
“Downstream separation” has become a crucial part of the shredding industry, and for the past two decades, it has been where much of the research and development in shredding technology has been directed.
Huron Valley Steel Corp., Belleville, Mich., has for several years operated facilities that use a variety of methods to extract as much metallic material as possible from the automobile shredder residue (ASR) shipped to them by shredder operators.
While most shredder operators use eddy currents and some also operate their own media separation systems, Huron Valley’s process involves a series of technologically advanced magnets, eddy currents, light and heavy media separation systems, and light imaging systems. The combination of processes is configured to wring out every possible metallic element from the ASR shipped to Huron Valley.
Chaparral Steel, Midlothian, Texas, and its parent company TXI have set up a similar venture called the STAR (Systems and Technologies for Advanced Recycling) project. The STAR project, now operating as Star Recycling, has been able to conduct research and develop separation technologies using the 180,000 tons of ASR that is produced at the massive shredder at Chaparral Steel’s Midlothian complex.
According to Star Recycling marketing manager Helene Honeybone, Star is using “heavy media and flotation methods” to separate out aluminum, stainless steel and mixed heavy metals from the ASR it processes. “When we take in residue from other shredders, it is already eddy current separated,” she notes.
“We went into flotation to increase the nonferrous metal revenue,” she says of Star’s own origins. “Ultimately, it increases the revenues of scrap processors produced from shredding autos.”
Star Recycling is optimistic that the flotation technology it has developed will allow the company to process a greater volume of material than some other heavy media systems while also producing a higher yield of marketable metals.
ACROSS THE POND
A directive that will soon be enforced in the 15 nations of the European Union (EU) has prompted attention to the overall recyclability of shredded automobiles.
According to the EU’s End-of-Life Vehicle (ELV) directive, auto manufacturers (and the dismantling and scrap companies that they choose to work with) will have to demonstrate that a certain percentage of the automobiles that are being scrapped are being successfully recycled.
The process developed by the EU means that starting with 2001 model autos, auto makers must provide cost-free “take-back” of all vehicles at dealerships. The companies or agents of the companies (dismantlers) must then “de-pollute” the vehicles to ensure that all toxic fluids have been drained and the batteries removed and sent to appropriate recycling or disposal sites.
Between the years 2001 and 2015, auto makers will have to demonstrate that an increasing percentage of the auto by weight is being recycled, starting with 85% in 2001 to 95% in 2015.
Thanks largely to the recyclability of the ferrous and nonferrous metallic content of autos, the first target of 85% seems to be within fairly easy reach. A study conducted by France’s Renault of ELV autos tracked in 1998 indicated an overall recycling percentage by weight of vehicles of 82.9%.
By Renault’s calculations, nearly two-thirds—65.6%—of the automobiles’ content consisted of metals that were shredded and shipped to mills, smelters and foundries. Another 17.3% by weight was recorded as being re-used or otherwise recycled by the auto dismantler network in France. That left 17.1% as ASR or other material that was land-filled.
Having tracked those numbers, Renault is implementing changes in the way it designs and builds cars that it believes can help it increase the total to 85% and beyond. The company is attempting to put in place a system that will allow dismantlers to easily remove certain large plastic components (bumpers, the dashboard, seat foam and tail light casings, for example) and return them to the Renault supplier companies who made them for regrinding.
If Renault’s efforts work as planned, auto shredder operators would ultimately receive Renault auto hulks that are lighter overall, but would consist of much more than two-thirds metallic content, making them a higher quality of shredder feedstock compared to the autos currently received.
The other solution being studied by European auto makers involves finding alternative uses for ASR. Currently, as in North America, ASR is most often land-filled, though in Europe that is becoming increasingly costly. Some nations are, in fact, “taxing to death” the very notion of land-filling ASR.
PROGRESS IN ASR END MARKETS?
Throughout the history of auto shredding, the phrase auto shredder residue end markets would have to be considered an oxymoron. ASR is not traditionally marketed, but rather disposed of.
Observing a pile of ASR can serve as an explanation of why it is so difficult to recycle the material. Even though there may be some plastic components that are commonly recycled within the mix of an ASR pile, there is a “needle in the hay stack” dilemma as far as separating those pieces from the many other types of plastic, rubber, composite, textile and glass materials found in the mix.
“It’s still regarded as a problem,” says Star Recycling’s Honeybone regarding the handling of the plastic, rubber and glass portions of ASR. (These combined non-metallic portions are sometimes referred to as the organic portion.) But finding end market solutions to the entire stream of ASR—including the organics—“was also one of the reasons that we went into this venture,” Honeybone says.
“We saw an opportunity to separate out the organics stream and do some-thing with that, and develop them into possible products long term” she remarks. “We realize this is not going to happen tomorrow—it’s a long process but we are committed to it.”
Among the ASR destinations being tried in Europe are cement kilns, and other waste-to-energy options for ASR are also being explored in Europe.
What remains to be seen, however, is to what extent the EU Parliament’s final version of the ELV legislation will allow waste-to-energy applications to count as recycling versus disposal.
Waste-to-energy scenarios are nonetheless being explored by the Association of Plastics Manufacturers in Europe (APME), Brussels, in cooperation with the American Plastics Council, Washington. The two trade associations jointly released a report earlier this year detailing the co-combustion of ASR along with municipal solid waste. “The study concluded that such co-combustion did not adversely impact boiler performance, stack emissions or disposal of the combustion residues,” the two groups remark in a joint statement.
The amount of effort being put into waste-to-energy methods may serve as an indication that both plastics manufacturers and shredder operators see such scenarios as the most feasible option in the near future.
On the American side of the ocean, where there is no ELV directive hanging over the heads of shredder operators, it remains to be seen whether affordable landfill tipping fees will continue to relegate ASR to the landfill either as daily cover or as tipped-in contents.
The author is editor of Recycling Today.
Sidebar
The Hazardous Side of Shredding
Operating an automobile shredder has its accompanying hazards, ranging from explosive devices entering the shredder to the danger of working near several moving parts.
Another type of hazard stemming from shredding operations, however, is the disposal or emission of trace amounts of toxic substances that enter shredders. For example, the U.S. Environmental Protection Agency (EPA) has been examining the amount of mercury found in auto shred.
In the case of mercury, much of it remains mixed in with the metal that is melted in foundries and furnaces. (Light switches are the primary source of mercury in automobiles.) An EPA scientist conducted a study earlier this year of emissions from furnaces that melt shredded auto scrap, and found as much as ten times more mercury in the emissions than was present in 1995. The EPA is considering its options concerning either urging or mandating the removal of mercury switches before autos are shredded.
Environmental considerations also affect the status of ASR and its potential re-uses. The presence of PCBs in certain types of plastic used in auto components may render them unrecyclable. Although much of the plastic may have no such toxic content, a recent EPA interpretation held that any plastic sent through an auto shredder that is mixed with PCB-laden plastic is non-recyclable under current EPA guidelines.
The ruling leaves daily landfill cover as one continuing option (the EPA considers this disposal rather than reuse), but puts on hold many other potential markets for ASR.
The Institute of Scrap Recycling Industries Inc. (ISRI), Washington, says it “is working with a broad coalition of interested parties to address this issue.” ISRI also admits, though, that the EPA interpretations concerning ASR re-use have “dealt a serious blow to recycling activities.”
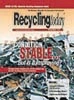
Explore the November 1999 Issue
Check out more from this issue and find your next story to read.
Latest from Recycling Today
- P+PB adds new board members
- BlueScope, BHP & Rio Tinto select site for electric smelting furnace pilot plant
- Magnomer joins Canada Plastics Pact
- Out of touch with reality
- Electra names new CFO
- WM of Pennsylvania awarded RNG vehicle funding
- Nucor receives West Virginia funding assist
- Ferrous market ends 2024 in familiar rut