Cranes, or scrap handlers as they are more commonly known in the recycling industry, are the pride and joy of most ferrous scrap yard operators and owners. That’s because they are the work horses of the business. Without them, scrap could not be loaded or off-loaded; transferred to the baler or shredder; or effectively moved from one area of the yard to another. "Today, if a scrap handler goes down, there goes the mortgage payment," says Tim Wilson, vice president of sales of Material Handling Crane Systems, Chagrin Falls, Ohio.
"Before hydraulic scrap handlers, scrap was usually delivered to a yard on a truck and dumped into a pile," continues Wilson. "Then the scrap was cut by hand, and, if there was enough of the material, then a cable crane would move it aside and it would sit there for maybe six months. But you can’t operate like that today. With the demands of the mills and the high-duty cycles required to feed heavy-duty shredders, a yard cannot afford to lose its scrap handler."
Not too long ago, there was a fundamental shift in the scrap handler business. All scrap handlers were originally cable-operated. It was not until the late 1970s and early 1980s that the hydraulic scrap handler began making inroads into the market, although hydraulic material handlers and excavators had been well established in the construction industry for some time.
Today, the hydraulic-operated scrap handler is the standard in the scrap business because of its flexibility, high productivity, low cost and ease of operation. But there are still a large number of cable-operated units in operation. One industry observer estimates that there could be as many as 4,000 cable-operated cranes still in use, compared with 7,000 that are hydraulically-operated.
The U.S. ferrous scrap market is likely to stay strong for the foreseeable future thanks to increased demand from new minimills. Therefore, processors may want to consider upgrading their scrap handling capabilities sooner rather than later.
CUSTOM CONVERSIONS
There are a number of considerations to take into account when shopping for a scrap handler. One is whether the machine is a converted excavator or is expressly built to handle scrap. Although there is a growing movement to purpose-build the machines from the ground up as more manufacturers target the scrap handling industry, currently many of the excavator manufacturers do not make a production scrap handler. Instead, they farm out conversions to other companies. Material Handling Crane Systems is one such company that currently has conversion arrangements with Case, Caterpillar, Deere, Hitachi, Hyundai, Koehring, Komatsu, Link-Belt and Samsung. Material Handling Crane Systems converts about 150 excavators a year.
Because of the differences in material handling, the excavator must be modified in several major areas to perform properly in a scrap metal handling environment, including the undercarriage, boom, counterweight and operator position.
The conversions by Material Handling Crane Systems are done at its site in Ohio, then shipped back to the manufacturer for sale.
Norris Equipment & Fabricating Inc., Carrollton, Ohio, which also has a West Coast facility, is another company that does conversions and crane modifications. "If a customer buys an excavator, we will modify the necessary components at our facility, such as the boom and stick, cab, counterweight, etc., then ship those back to the customer and reinstall them on site," says Monica Norris, office manager at Norris. "It is more cost effective that way."
"Whatever the customer needs, whether to lengthen or shorten a boom, or add a generator and magnet, we can do it," she says. "We have done thousands of conversions on all kinds of excavators." Norris says conversions usually take about 35 to 45 days to complete, and they back up all their work with a two-year guarantee.
Those companies that convert excavators say that a conversion offers the same performance of a purpose-built handler, but at substantial cost savings.
DESIGNED FOR SCRAP
Although excavator conversions are popular, there are several companies that design and build scrap handlers from the ground up. Representatives from these companies flatly say that conversions can’t match up against purpose-built ones. One such company is Liebherr, based in Switzerland, with a major production facility called Liebherr-America Inc. in Newport News, Va., and supported by masterdealer Republic Crane & Equipment, Charlotte, N.C., and several other dealers in the U.S.
Liebherr claims to be one of the first companies to market a purpose-built hydraulic scrap handler back in the 1970s. Today, the company offers 14 different models, from pedestals to crawlers and rubber-tired versions. "I would say that we have the largest offering of original equipment hydraulic scrap handlers of any company," says Bill Allen, president of Republic Crane.
There are some concerns with excavator conversions, according to Allen. "The excavator is built for digging, not lifting," he says, "and when you start modifying it you begin to change a perfectly-designed machine into something less than perfect. At Liebherr, everything is factory installed to exact tolerances, and when it comes time for maintenance, there’s one book for parts, one source."
Tom Skodack, North American sales representative for Fuchs, a division of Karl Schaeff GmbH & Co., Germany, agrees. Fuchs, which is supported in the U.S. by Schaeff Corp., Sioux City, Iowa, also makes OE scrap handlers.
"We feel that a conversion can correct and adjust the excavator design only up to a point," says Skodack. "In the design of the excavator all the forces are geared toward pushing down and pulling back, and you can’t correct that without compromising another area. The forces transmitted back to the main frame are different, and different bending moments are created."
An original design uses less counterweight, so less horsepower is required to operate the scrap handler, according to Skodack. He says that with a purpose-built handler, an operator can lift about 65 pounds more per horsepower than with a converted one. He also points to the handlers’ swing bearing – the one between the lower tracked or wheeled section and the upper portion that rotates. "When you add more counterweight to the handler that bearing is going to wear more, so it will not last as long as you expected," he says. However, Norris and others claim that their conversions last just as long as purpose-built scrap handlers.
There may be middle ground between these polar views, according to Robert Thompson, president of Austin Heavy Equipment Services, Corpus Christi, Texas, who also sells a purpose-built scrap handler. He simply recommends that dealers investigate before they buy. "There are areas such as the hydraulics that are different from machine to machine," he says. "For instance, dealers need to know the difference between high- and low-pressure hydraulic systems, the operator’s parameters and the cost and parts availability associated with each type of system."
The hydraulic system is the heart of the scrap handler, according to Jim Westlake, vice president of Eastern Railway Supply, West Seneca, N.Y., and dealer of Atlas scrap handlers. "It’s going to make a big difference in daily production," he says. "An Atlas material handler has no high-pressure oil circulating when not performing a use function, for instance, that wastes horsepower and creates heat."
Within the universe of OE scrap handlers, there are some new developments. American & Ohio Locomotive Crane Co., Bucyrus, Ohio, recently introduced its new "E" Crane (the "E" stands for "Equilibrated"). The scrap handler is a combination of hydraulics and mechanical linkages to "achieve efficiencies in weight and movement," according to Sam Eichorn, general manager of the company. Instead of hydraulics throughout, the company has one hydraulic cylinder to maneuver the boom, and another cylinder that moves the counterweight in and out for balance. The top of the counterweight is then linked to the end of the stick, so when the counterweight moves in and out, the stick moves, too. Seram, France, is another company that has had a similar system on the market for some time, according to Eichorn.
Equilibrated cranes are desirable, says Gus Arenas, owner of Gala Environmental, Tampa, Fla., and the U.S. distributor for Seram, because the moveable counterweight keeps the scrap handler in perfect balance at all times. Thus, the crane is using power to only lift the load, and not the boom.
Another new development comes from Link-Belt Construction Equipment Co., Lexington, Ky. The company sells excavators converted to scrap handlers, and also makes production purpose-built ones. It recently introduced its new 6000 Quantum Scrapmaster, which replaces its LS-6000 C-series II model; and also introduced a new 4300 Scrapmaster.
The oil filter system is a feature that Ed Gitlin, vice president of Mid City Scrap, Iron and Salvage Co., Westport, Mass., really likes on a 4300 model that he recently bought. "The new Nephron oil filter system eliminates contaminants 1 micron or more in size," he says. "Anything that helps our machines get a longer service life is money in our pocket." Gitlin also likes the feature that provides a mechanic easy access to clean the oil cooler.
Caterpillar, Peoria, Ill., is also a company that sells conversions and builds scrap handlers from the ground up. "Our 5080 is a conversion, but our 320,325, 330 and 350 models are designed for scrap handling," says Barbara Hoffman, marketing services consultant for Caterpillar. "But that doesn’t mean our conversion is less than capable – it’s Cat all the way!"
Hoffman also points to the scrap handler’s unique side-by-side oil cooler which is designed for maximum cooling efficiency and easy cleaning, but she also points to the "overall ruggedness" of the Cat design. "I think what scrap processors like about our scrap handlers is the beefiness of the machines, and the durable fronts," she says. "Plus, they know we will be there to support them after the sale."
In addition, Caterpillar employs a Proportional Priority Pressure Compensated valve on its handlers that automatically proportions hydraulic fluid flow so that all functions proceed smoothly and predictably. The PPPC valve also adjusts pump flow based on demand, which reduces sound levels, heat output and fuel consumption, according to the company.
Atlas scrap handlers have a computer controlled hydraulic system that regulates functions according to desired working conditions. There are three pre-set operating modes for maximum precision, handling capacity or operating economy, in addition to a self-programmable operating mode. Other control features include automatic delayed idling and load limit control, according to Westlake.
ON THE MOVE
Today, most mobile scrap handlers are tracked vehicles, commonly referred to as crawlers, but this may be changing as more owners pave their yards to better comply with EPA stormwater guidelines and other environmental regulations. As this happens, many are turning to scrap handlers with rubber tires. The tires do not tear up the pavement like a tracked vehicle does, and they give the scrap handler better maneuverability.
"There aren’t many scrap handlers out there today that are wheeled," says Wilson, "but that is changing, and I foresee the scrap handler with tires becoming more and more popular."
Thompson, who agrees that the trend is toward wheeled scrap handlers, recommends that processors do some research in the area of tires. "We have had a lot of success with pneumatic tires, and buyers should not count them out," he says.
In Western Europe, most scrap handlers have already made the transition from tracked to wheeled, according to Allen. "Today, 90 percent of the scrap handlers in Europe have rubber tires," he says. Allen foresees that trend taking hold in the U.S. "About eight years ago, one out of every ten scrap handlers we sold in the U.S. was wheeled; now six out of every ten we sell are wheeled."
Scrap handler mobility is another area which is progressing. Many in the industry point to a time when the yard was built around the crane and the crane rarely, if ever, moved. Then crawlers came along and were more mobile, but still had a tendency to be fixed in one area. "Now with rubber-tired handlers, the operator can move from one part of the yard to another in a timely manner," says Skodack. "Customers today require a finer sort of scrap, and yards are going to have to keep up to stay competitive. One way to maintain a better sort is to handle the material the correct way from the time it is delivered and not have it dumped in one spot. A wheeled handler can follow the truck to different drop off points."
Reports from the field to the suppliers indicate that yards that are employing wheeled handlers have to equip them with radios because the handlers are covering a lot of ground. "It could be here one minute, then gone the next, so many yards are finding that they have to now give their scrap handler operators radios to keep in contact with them," says Skodack. "When the operator is more mobile he wants to do more, and with the quick-change attachments for the front that are now available, productivity can really be given a boost."
Another advantage to having a mobile scrap handler that it can be moved by trailer to handle scrap material outside the yard. "A scrap dealer can easily go out after certain material provided he has the right kind of equipment to roll in and out of a remote location in short order," adds Skodack.
"If you can have two highly efficient mobile cranes, instead of four old crawlers, then you are better off," says Allen. "Even the new minimills are making a transition to mobile hydraulic scrap handlers instead of using overhead cranes."
Wheeled scrap handlers are starting to make an impression on processors, agrees Jeff Padnos, president of Padnos Iron & Metal, Holland, Mich. "There were some at the recent scrap show and they definitely turned our heads," he says.
However, Arenas says that a stationary handler is still more effective if it is used to constantly feed a shredder or conduct some other similar, repetitive action. "With a stationary crane you can achieve better efficiencies because you can use an electric motor, and don’t have to worry about mobility. So although there’s a trend toward wheeled scrap handlers, both stationary and mobile ones are needed."
SCRAP HANDLER CARAVAN |
For the last five months, Case Corp., Racine, Wis., has been taking its scrap handling equipment to the field in what it calls “The Case Scrap Caravan.” The caravan stops at select Case dealerships in North America and offers customers a chance to try out specifically-designed scrap-handling machines. “This program allows customers to try out equipment designed for the scrap-handling industry at their own facilities, performing the jobs they do daily,” says Robert Weiglein, Case marketing manager, application systems. The scrap caravan is one of several Case caravans, including waste-management, sewer and water, demolition, aggregate and forestry, touring Case dealerships this year. . |
And paving does not necessarily mean that a yard has to make a transition to wheeled scrap handlers. The M. Lipsitz & Co. facility in Waco, Texas, has a scrap area that is 100 percent paved, but tracked scrap handlers are still used on the pavement. "We did two things," explains Melvin Lipsitz, vice president of the company. "We added rubber pads on the tracks, and we paved the yard the way airport runways are paved, with two 10-inch concrete layers that are laid in different directions on top of each other."
Although padding tracked vehicles is okay, some manufacturers warn that in cold climates vehicle operators have to guard against slippage on pavement because of the smooth surfaces.
Still, Lipsitz has a wheeled scrap handler, in addition to one truck-mounted crane, one on a pedestal and three that are tracked. "We run our operation like a production line, so our handlers don’t need to be moving around a lot," he says. "I like the wheeled handler, not because it is easier on the pavement, or because it is faster and more mobile, but because there is less maintenance on the undercarriage."
Overall, Padnos is pleased with the major heavy-duty handling equipment manufacturers who are now taking the scrap industry seriously. "These manufacturers are now genuinely listening to us and looking for ways to make their equipment better in order to meet our needs," he says.
The author is managing editor of Recycling Today.
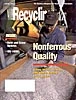
Explore the August 1996 Issue
Check out more from this issue and find your next story to read.
Latest from Recycling Today
- Green Cubes unveils forklift battery line
- Rebar association points to trade turmoil
- LumiCup offers single-use plastic alternative
- European project yields recycled-content ABS
- ICM to host colocated events in Shanghai
- Astera runs into NIMBY concerns in Colorado
- ReMA opposes European efforts seeking export restrictions for recyclables
- Fresh Perspective: Raj Bagaria