
North American recycling companies began investing in wire chopping equipment at the end of the last decade in response to changes to China’s import policies for insulated wire.
Previously, wire and cable processing in North America was more specialized, with processors focused on recycling high-grade wire and cable. Now, in addition to processing high-grade materials, recyclers are recovering copper and aluminum from lower-grade material streams, which has involved investing in flexible systems that can handle various wire types and other forms of scrap, such as aluminum-copper radiators.
Versatility is a virtue
“For recycling processors adding a wire granulation and separation system, it’s essential to invest in equipment that offers high efficiency, durability and flexibility to handle different wire types,” says Sean Abenstein, chief commercial officer with Toronto-based Gensco Equipment Inc. and Gensco America Inc., Decatur, Georgia. “Look for machines that optimize yield while minimizing downtime.”
Gensco distributes wire chopping equipment manufactured by Guidetti S.r.l., based in Renazzo, Italy.
“Recyclers can ensure their cable and wire processing systems are flexible by investing in equipment that is designed to handle a wide range of materials, including copper, aluminum and mixed cables,” Abenstein continues. “Choosing the right compact or modular system allows for easy adjustments and upgrades as material types or volumes change. Additionally, selecting machinery with adjustable settings for granulation and separation processes, such as a refining mill, variable screen sizes and adjustable processing speeds, enables the system to process different materials efficiently.”
Versatility is an attribute other suppliers advise as well.
In wire chopping plants supplied by Denmark-based Eldan Recycling S/A, Product Specialist Flemming Hansen says the versatility comes in at the separation stage after the fine granulation.
The company works with customers to develop new applications, machines and processes for their needs, he says.
“When you’re making your investment, you need to plan for now, but you also need to prepare for the future,” says David Siejka, sales director at Wendt Corp., Buffalo, New York, which represents French equipment manufacturer MTB. “The feedstock that you’re planning to feed into your line right now is probably going to be different in five or 10 years.”

He says the company’s downstream systems, shredders and granulators are designed to be tuned to process a variety of materials, whether radiators, No. 1 wire, No. 2 wire, low-grade copper wire or aluminum cables. “The pieces can be tuned to process whatever you’re doing.”
In terms of capacity, he says Wendt designs systems that allow for growth. “We’ll design it for around 75 percent of one shift capacity, so your growth is getting to 100 percent capacity, then getting to an additional day or into a second shift. From there, you can plan how to reconfigure the pieces and what equipment can be added so that you can continue to grow.”
Christopher Simon is a recycling systems sales representative at Sweed, Gold Hill, Oregon, a manufacturer of copper and aluminum recovery systems. He says to provide versatility, Sweed installs its turbo mills with a bypass. “So, if you’re running No. 1 wire, you don’t have to mill it. You don’t want to mill it. Not that it’s a very high cost, but you could create some copper dust, which would equal some yield loss. You simply, in this case, push a button and turn a diverter plate, and then you’re not using the turbo mill.”
Even for processors of Nos. 1 and 2 wire, Simon says, “Within those two classifications, you can have very different materials that require system adjustments in relation to each material, that’s why it’s important to build flexibility into any chopping line and understand what adjustments are possible for each material classification.”
He also suggests that recyclers have their material tested on the equipment they are considering purchasing. Using Sweed’s test lab in Oregon, Simon says, “we can confirm their recovery rates. We can confirm their material quality.”
Abenstein says it’s important to choose a vendor with years of experience in supply and service, with spare parts on hand.
Simon encourages recyclers shopping for wire chopping equipment to ask questions of potential suppliers to truly understand the systems they are proposing and whether they are designed for their specific material steams.
As copper value continues to increase, processing lower-quality materials can start to make sense, he says. Some of these materials cannot be processed in a traditional chopping line. “If we know ahead of time what kinds contamination are present, we can design a system with the appropriate equipment to ensure high quality results with low operation cost.”
Expanded capabilities

For companies that want to improve or expand their existing wire chopping lines, Abenstein suggests adding advanced separation technologies, such as turbo mill systems and electrostatic air separators. He says such technology “can significantly improve the recovery rate of smaller and more challenging wire and cable types.
“Additionally, integrating automated systems with material handling conveyors and dosing systems can enhance productivity and reduce labor costs.”
For recyclers with existing lines who want to add capacity or improve efficiency, Simon says he likes to visit their operations and watch them run a shift. “I may be able to make some suggestions, especially on some of the harder-to-sort materials.” Sometimes simple changes can have a large affect, he adds.
Adding capacity can involve installing larger machinery, Simon says, while increasing purity can involve additional screening and separation equipment.
“Sometimes, you’ve got plenty of capacity on your tables; we can look at adding greater granulation capacity,” he explains. “[By] adding a second granulation line, then running that material to your existing table, you can see a substantial increase in capacity for the fraction of the cost of a completely new line.”
Hansen says today’s well-performing plants are characterized by robustness and minimal downtime for maintenance and service. “The key factor today is also the fact of avoiding loss of metals in the process and in the plastics/organics.”
Abenstein notes the importance of the separation process in wire chopping. “Companies that can supply a variety of screening or mesh tables is a bonus,” he advises. “Having the ability to quickly change, clean and control different types and sizes of granular and tailings provides better processing and removes the likelihood of contamination.”
In addition to dedusting or dust collectors that remove light waste, aspiration units can be incorporated to capture small copper chops and powder flakes that otherwise could be lost in the tailings or dedusting systems, he adds.
Additional considerations
Recyclers need to consider if they have adequate electrical supply and if their foundational support is sufficient for a wire processing line installation or if their floor will need to be reinforced, sources say.
One consideration that often is overlooked, Siejka says, is space. “You need to plan for more than just space for your wire chopping line. Ideally, you’re growing; you should have lots of material coming in and lots of chops ready to go out. So, how do you plan to keep that inventory in an enclosed area where it’s safe and secure?”
Protection from the elements also could be necessary. For example, the fluff in auto shredder residue (ASR) wire can absorb water. “You want to keep it dry,” he says, to ensure efficient operation.
“A company’s ability to assess, store and process grades and types of copper will allow for better separation and control,” Abenstein says. “With respect to operation, cleanliness of the processing area and proper maintenance are vital. Regular maintenance and operator training also help to maximize the versatility and efficiency of the system.”
Preparation and operation

Siejka says operators should do two types of material preparation. “There’s preparation for product quality and there’s preparation for what your machinery can actually handle. If you’re processing No. 1 wire, you have to produce high-quality chops on the way out. One leaded battery cable in a load could have the potential to blow your lead spec. Your hand sorting on the way in has to be really good.”
When handling lower-grade materials, equipment robustness is more important, Siejka says, as it could contain more wear-causing elements like steel, stainless, plug ends and junction boxes. If that material is missed in presorting, less robust shredding and granulating equipment could see increased wear and unplanned downtime.
“If you have a less robust process in front of your separation equipment, you have to invest more time, more effort [and] more labor into removing anything that’s going to break your machine,” he says. Using a more robust processing system upfront, Siejka says, operators can focus less on removing heavies and more on separation that occurs later in the system.
For processing lower-grade materials, Sweed uses heavier, larger prechoppers at the front end of its lines to manage the contamination, Simon says. “Then we’re using more advanced magnetics. Instead of just having a cross-belt magnet, we’ll put in a high-gauss magnetic separator, which removes stainless, but it’s also another way to get the small hardware, nuts and bolts. Removing any ferrous contamination will prolong the life of your granulator knives and lower your operating cost.”
He adds that a wider range of material sizes could exit the granulator when processing lower-grade materials. “Density separation technology works best on an isolated size range,” Simon says. “So, we may decide to separate the stream early to try to get some of that stuff out or perform multiple separation steps.”
The art of wire chopping
Siejka says an MTB trainer once told him wire chopping is part science but largely is an art. “It takes time to acquire those skills, to be able to properly tune all the equipment, to be able to learn all the things that the separation line can actually do,” he says.
The best operators invest in equipment and personnel, he adds. “I think investing in your people is huge and something that’s often overlooked. Wire chopping is more sophisticated than you would think, and keeping that expert knowledge in-house is extremely important.”
Get curated news on YOUR industry.
Enter your email to receive our newsletters.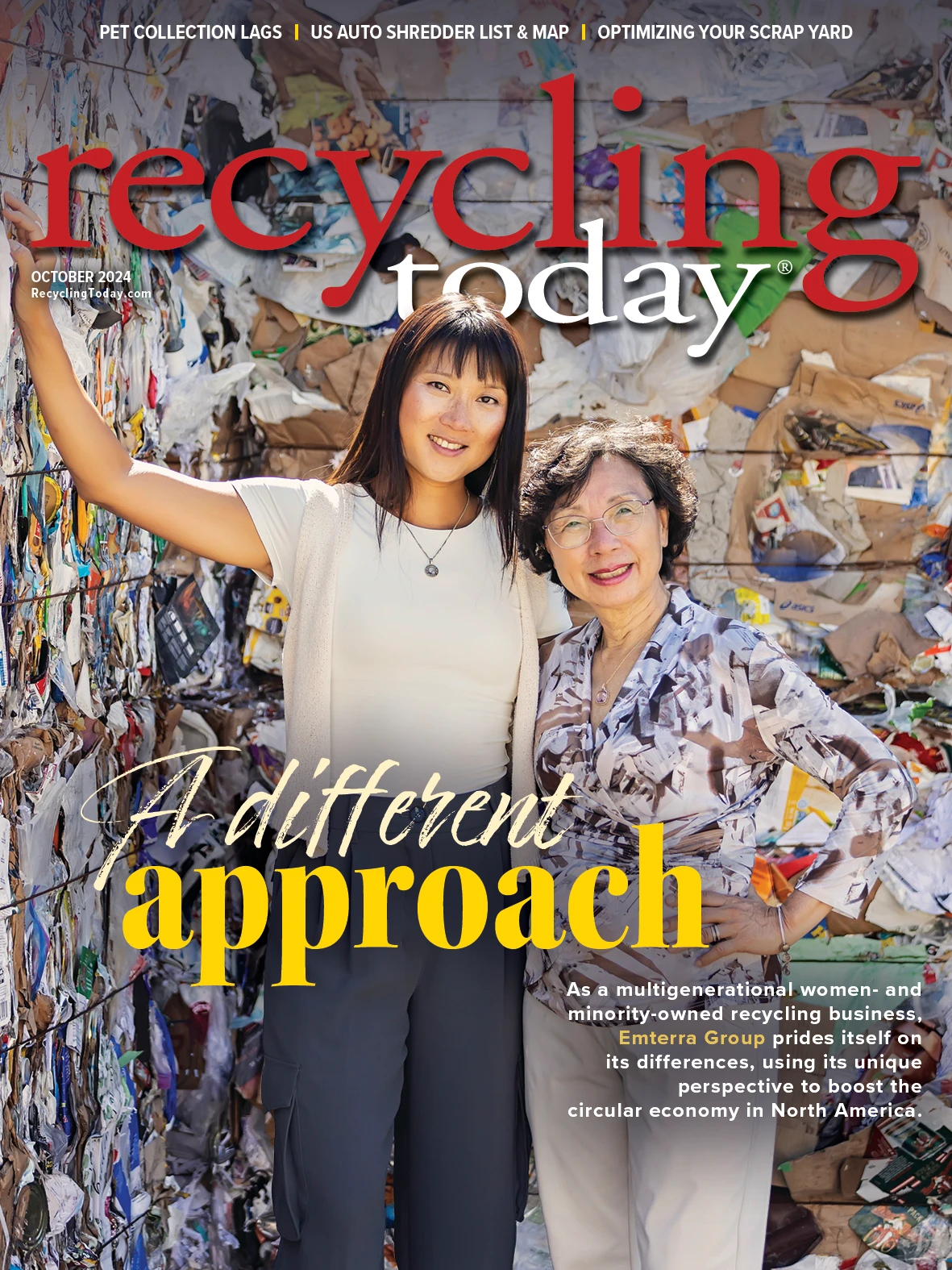
Explore the October 2024 Issue
Check out more from this issue and find your next story to read.
Latest from Recycling Today
- European project yields recycled-content ABS
- ICM to host co-located events in Shanghai
- Astera runs into NIMBY concerns in Colorado
- ReMA opposes European efforts seeking export restrictions for recyclables
- Fresh Perspective: Raj Bagaria
- Saica announces plans for second US site
- Update: Novelis produces first aluminum coil made fully from recycled end-of-life automotive scrap
- Aimplas doubles online course offerings