The complete line of Winkle (link to www.winkleindustries.com) scrap handling magnets, now called OptiMag, has been redesigned and additions have been made using new proprietary engineering software to achieve lighter weights, increased lifting capacity and lower costs for recyclers and steel mills, according to a press release issued by Winkle, which is based in Alliance, Ohio.
Sponsored Content
Still relying on manual sorters?
Let AI do the heavy lifting. Waste Robotics delivers reliable, high-performance robots tailored for complex waste streams. They require minimal maintenance, are easy to operate, and are designed to boost your recovery rates. Smarter sorting starts with the right partner. Waste Expo Booth #1969 & REMA #2843
Click here to see our robots in action!Get curated news on YOUR industry.
Enter your email to receive our newsletters.
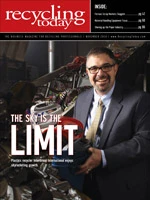
Explore the November 2010 Issue
Check out more from this issue and find your next story to read.
Latest from Recycling Today
- ReMA board to consider changes to residential dual-, single-stream MRF specifications
- Trump’s ‘liberation day’ results in retaliatory tariffs
- Commentary: Waste, CPG industries must lean into data to make sustainable packaging a reality
- DPI acquires Concept Plastics Co.
- Stadler develops second Republic Services Polymer Center
- Japanese scrap can feed its EAF sector, study finds
- IRG cancels plans for Pennsylvania PRF
- WIH Resource Group celebrates 20th anniversary