
The solution the North Aurora, Illinois, company came up with was to add new size-reduction equipment from Lindner Recyclingtech America LLC, Statesville, North Carolina. Winco purchased a regrinding line, consisting of a Micromat Plus 2500 shredder and an LG 1500-800 grinder.
“I wanted higher volumes of regrind for production,” Martin says.
The new setup has been effective.
Operating out of a 57,000-square-foot warehouse, Winco buys, sells and processes postindustrial commodity and engineering plastics and also offers toll-grinding services. It processes several kinds of plastics, including high-density polyethylene (HDPE) pipe, HDPE and polycarbonate sheet, polyethylene (PE) and polypropylene (PP) purgings and polyethylene terephthalate (PET) from a variety of postindustrial sources.
Winco’s restriction on space was the biggest challenge, says Tomas Kepka, vice president of Lindner reSource America LLC. “That’s something where Lindner was the best fit because of our small footprint.”
But the solution wasn’t as simple as installing a new shredder and grinder, Kepka says. One of the challenges was dealing with the many sizes and types of materials that Winco handles.
Lindner got specifications on the materials Winco wanted to process and customized the new line to handle that material and produce the required throughput—about 5,000 tons per hour of 0.5-inch regrind.
In the system, plastic is placed on a heavy-duty belt conveyor that feeds the 180-horsepower Micromat Plus 2500.
The single-shaft shredder has an internal ram that allows for high throughput. It is designed to prevent material from bridging between the ram and rotor during shredding.
The overlapping rotor is 22 inches around and 98 inches long. It carries four reversible 1.69-inch-by-1.69-inch Monofix knives. Designed for productivity, the knives need minimal maintenance, according to Lindner.
Two separate conveyors—one linked to the Micromat and another linked to a
“It can grind any size purge—a
Kepka says the Lindner shredder can handle parts as long as 8 feet with diameters of up to 50 inches.
Knife maintenance is simplified through Lindner’s Monofix system, in which one bolt holds a knife, as well as the knife holder, in the rotor pockets. Exchanging a complete set of knives takes no more than two hours, including cleaning and adjusting the knives and exchanging the counter knives, Kepka says.
Martin says the new Lindner line also is a big upgrade in terms of safety; features include stop cords around the conveyors.
In addition, the system uses less power and requires little maintenance.
As part of its compact design, the shredder has an internal swing ram inside the hopper rather than a traditional horizontal ram.
“We customized this shredder with our infeed and discharge conveyor; therefore, we were able to place everything in quite a small space,” Kepka says. The installation covers 1,200 square feet.
Martin says the increase in production is significant. “It’s just more efficient, and you can actually run the whole machine with two guys versus one machine [where] you’re only running [with] one guy, but your output is 3,000 to 4,000 pounds a day. With this machine, you’re doing 30,000 to 40,000 pounds a day. ”
The initial cost was a challenge at $850,000, Martin says. But, with the increased production, it has paid for itself.
For more information: Lindner Recyclingtech America LLC, 470-819-8281, www.l-rt.com Winco Plastics, 630-966-2002, www.wincoplastics.com
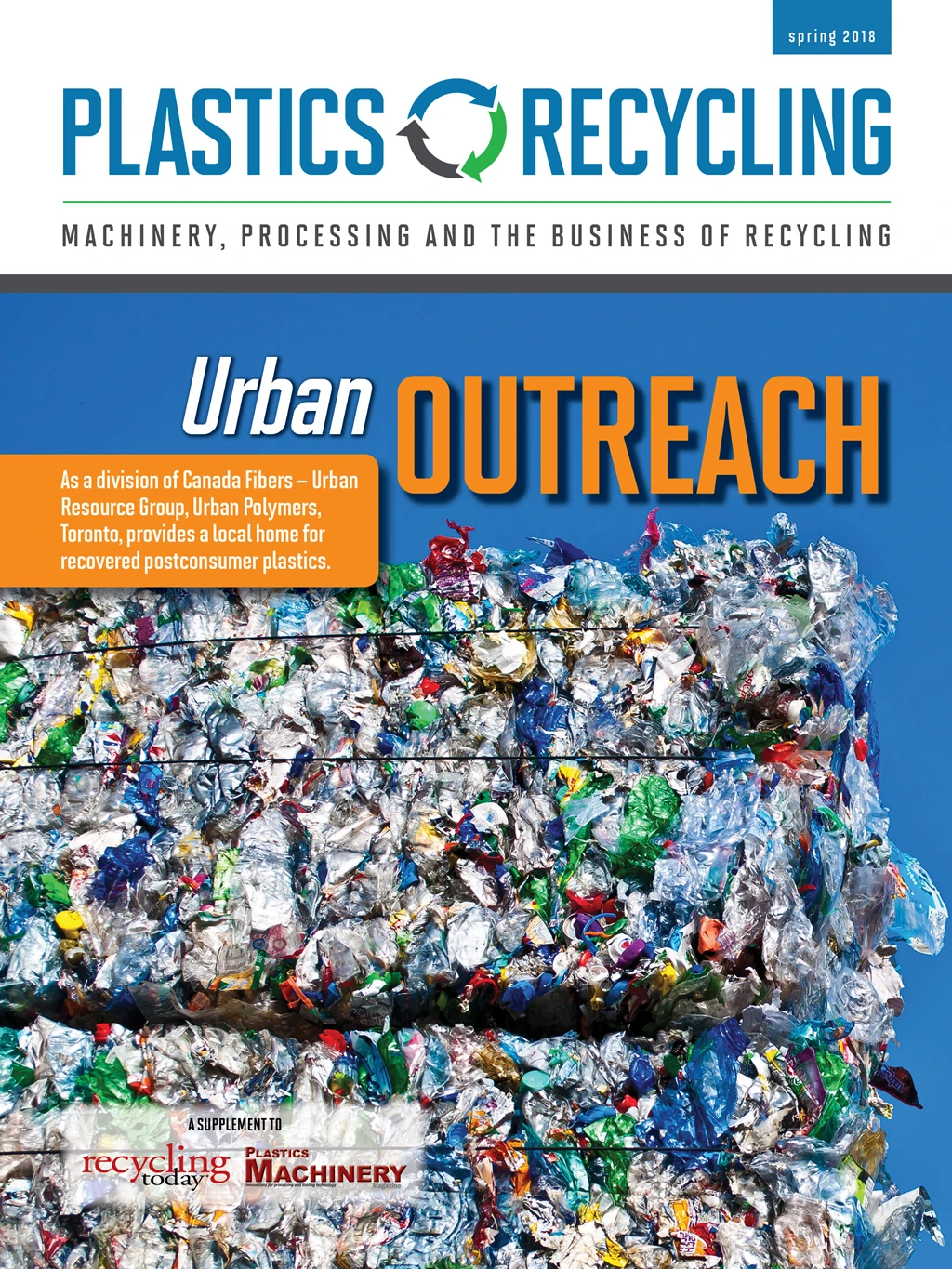
Explore the May 2018 Plastics Recycling Issue
Check out more from this issue and find your next story to read.
Latest from Recycling Today
- GFL opens new MRF in Edmonton, Alberta
- MTM Critical Metals secures supply agreement with Dynamic Lifecycle Innovations
- McClung-Logan Equipment Company joins Tana’s authorized dealer network
- Grede to close Alabama foundry
- Plastics Recycling Conference 2025: Working toward their targets
- SWACO rolls out new commercial recycling and food waste programming
- Updated: Matalco to close Canton, Ohio, plant
- Metso launches electric Anode Weighing and Casting Machine