
Adding recycled plastic to asphalt for paving streets and parking lots has gained new interest. That’s a solid idea, and it comes as the Biden administration appears ready to support recycling and invest in infrastructure projects.
The Plastics Industry Association (PLASTICS) is managing a pilot project with resin manufacturer LyondellBasell to pave a parking lot in Ohio with asphalt fortified with 4,000 pounds of recycled polyethylene (PE) film.
Two significant projects also are underway in California. The city of Los Angeles has resurfaced a heavily trafficked downtown street with asphalt containing recycled resin as part of a sustainability project called LA’s Green New Deal. Also, near Oroville, a 1,000-foot segment of busy Highway 162 was repaved in July 2020 using recycled plastic as a binder in the asphalt.
The two California projects are in a mild climate, but the asphalt used in the Ohio parking lot will have to withstand the freeze/thaw cycles of harsh winter weather.
The Scottish company MacRebur, which calls itself The Plastic Road Co., announced plans to open a plant in Florida to manufacture MacRebur’s products, which it says have been used in road projects around the world.
Adding recycled plastic to asphalt is not a new idea, but it has been slow to gain interest in this country. Roads in India have long been patched with plastic-modified asphalt. Projects also are underway in the U.K. and the Netherlands.
In Ohio, the parking lot is at LyondellBasell’s Cincinnati Technology Center. The equivalent of 71,000 PE retail bags was added to hot-mix asphalt to pave 2,885 square yards. If this project is successful, the organizations have similar plans for another parking lot that is about five times bigger.
Last summer, PLASTICS announced that research had been completed on the process of using recycled PE as a solid additive during the asphalt manufacturing process. New York-based Domino Plastics Co. supplied the recycled resin.
The downtown Los Angeles project involved a block of 1st Street between Grand Avenue and Hope Street, which is a high-traffic area in front of the Walt Disney Concert Hall.
The asphalt on the road was removed, and recycled polyethylene terephthalate was added to it on-site; then the mixture was used to repave the street. The new material is thought to be five to six times stronger and more durable than normal asphalt.
Los Angeles officials picked 1st Street for the test project because it gets heavy vehicle use and has suffered deep rutting and deformation. LA has about 23,000 miles of roads and repaves about 2,000 lane miles each year. Officials estimate that about 25 percent of the city’s roads could be candidates for this process. The test project is expected to take up to two years to complete.
Infrastructure projects are important to the Biden administration and could provide new uses for significant amounts of recycled plastic.
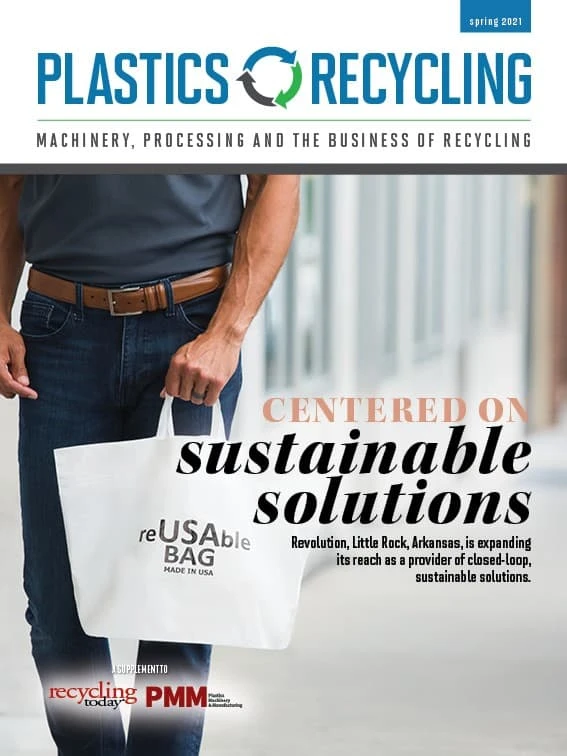
Explore the Spring 2021 Plastics Recycling Issue
Check out more from this issue and find your next story to read.
Latest from Recycling Today
- Freepoint Eco-Systems receives $50M loan for plastics recycling facility
- PET thermoform recycling the focus of new NAPCOR white paper
- Steel Dynamics cites favorable conditions in Q1
- Hydro starts up construction in Spain
- Green Cubes unveils forklift battery line
- Rebar association points to trade turmoil
- LumiCup offers single-use plastic alternative
- European project yields recycled-content ABS