_fmt.png)
Many within the U.S. recycling industry have a common misperception that when it comes to industrial standards and environmental regulations Mexico represents the Wild West. Waste Eco Treatment (WET), a company based the state of Querétaro, Mexico, is committed to breaking those perceptions, which it says simply do not reflect the reality of the country, its people or WET’s long-standing mission to care for the environment through the responsible collection, storage, transportation and recycling of hazardous waste.
Santiago Ortega, an executive at WET, had been on a mission for more than a year to find the right equipment for WET’s ambitious expansion plans. Ortega had taken a global tour, attending recycling conventions and expositions and visiting recycling equipment manufacturers in his effort to find the right equipment. While attending ISRI2019, the annual convention hosted by the Institute of Scrap Recycling Industries (ISRI), Washington, in Los Angeles this April and WasteExpo in Las Vegas in May, one line of size-reduction equipment in particular piqued his interest: The Solo series from CM Shredders, Sarasota, Florida.
Earlier this year, CM Shredders, a manufacturer of industrial shredders and recycling systems, introduced the Solo line of single-shaft shredders, which are designed to provide a consistent and exact finished particle size for use in a wide range of applications.
The Solo series is the first line of shredders developed jointly with CM’s new sister company, Schutte Hammermill, a New York-based manufacturer that has developed an extensive line of size-reduction equipment that includes hammer mills, lump breakers, crushers and shredders.
Exploring the options
“We researched, viewed and climbed all over recycling equipment from Europe to China, and admittedly we probably have had way too many boxes to check on our mission to find the perfect machine and manufacturing partner who we could count on for the long run,” Ortega says.
_fmt.png)
He says he was intrigued by the news that CM Shredders and Schutte Hammermill had combined their knowledge and equipment “to develop turnkey solutions to process nearly every market we are servicing with a single machine.”
“WET approached us with a substantial list of applications and very specific sizes for each material they wanted to process all within one machine,” says Mario Vazquez, sales and marketing director at CM Shredders. “One day WET could be processing textiles, and the next they could be running scrap wood or pallets, plastics, paper, carpet or a plethora of other materials used for recycling and biofuel feedstock.”
He adds, “We accepted and welcomed that challenge.”
The companies scheduled a time for the WET team to visit and run tests involving dozens of materials at CM’s new test lab and R&D demo facility in North America.
Putting equipment to the test
Located at its headquarters in Sarasota, CM’s new 4,000-square-foot R&D and demo facility features dual-shaft and single-shaft shredding systems from the company’s product range.
It was quickly evident that the CM Solo series shredder was the machine and CM Shredders was the partner WET had been searching for, Ortega says.
The Solo line features CM’s shredding technology, replaceable sizing screens and a “Smart-Ram” system that is designed to automatically adjust ram pressure for maximum efficiency. The shredders feature four-way reversible tool steel cutting teeth.
The Solo line also is designed to use less power, produce minimal dust and reduce manpower requirements.
The line is available in five models with the choice of 12-, 15- or 20-inch rotor diameters and powertrain options ranging from 30 horsepower to 125 horsepower.
“Regardless of the products or materials we threw at them, CM had technology, equipment, innovation and expertise to deliver reliable, high-performance-based solutions to any of our recycling applications,” Ortega says. “We purchased and commissioned our first CM Solo shredder that same day.”
Vazquez says, “We will be able to not only develop processes but also to help out WET with a proactive approach when facing the challenges of today’s production environments, whether through test shredding, applications, developing turnkey systems, training support or R&D work.”
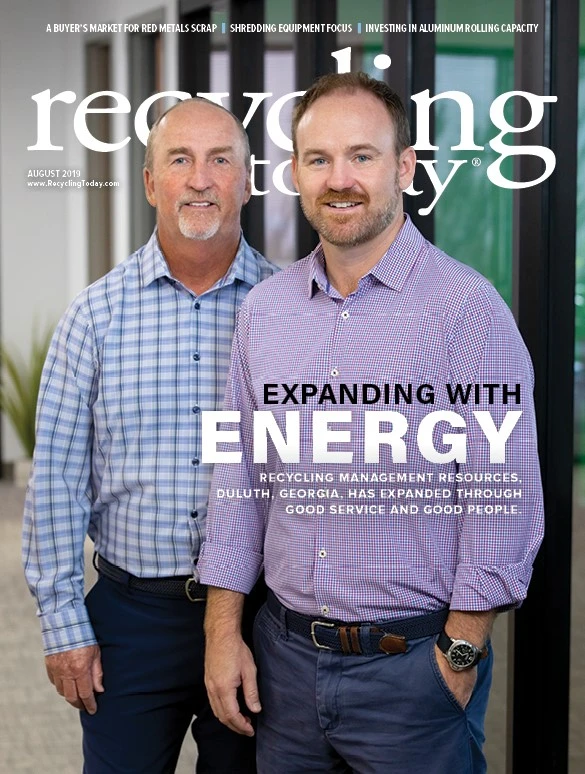
Explore the August 2019 Issue
Check out more from this issue and find your next story to read.
Latest from Recycling Today
- Nucor receives West Virginia funding assist
- Ferrous market ends 2024 in familiar rut
- Aqua Metals secures $1.5M loan, reports operational strides
- AF&PA urges veto of NY bill
- Aluminum Association includes recycling among 2025 policy priorities
- AISI applauds waterways spending bill
- Lux Research questions hydrogen’s transportation role
- Sonoco selling thermoformed, flexible packaging business to Toppan for $1.8B