
For several decades, the U.S. has generated considerably more recyclable postconsumer material than it can consume across several sectors, including aluminum, copper, steel, plastic and paper.
The U.S.’ scrap surplus has not been entirely bad for processors and traders, allowing them to compete in a global market with many bidders for these materials, including aluminum.
Many of those same processors and traders, however, would welcome a more robust domestic aluminum scrap melt shop landscape, whether to offer new potentially low-cost freight options or because they are rooting for a North American manufacturing sector that will generate and consume larger volumes of secondary materials.
Throughout this decade, several U.S. aluminum investment announcements could point to a near-to-medium-term future in which a higher percentage of this aluminum stays onshore.
A list worth compiling

U.S. capital markets have long been more enthusiastic about investing in companies and activities deemed to be high-tech, often leaving even well-run metals producers feeling as though they were struggling to live off the leftovers.
The tech sector continues to attract more investment dollars, but several investment trends have created an opening for recycled-content metals producers, namely sustainability and reduced emissions (including the potential growth of electric vehicle sales), newfound support for infrastructure spending and supply chain-related support for reshoring or reinvesting in the U.S. manufacturing sector.
In the first few years of this decade, those factors have prompted companies based in North America and overseas to invest in new recycled-content aluminum production in the U.S.
Norway-based Hydro ASA has invested in several new melt shops or to expand existing ones in the U.S., as has Sweden-based Gränges. The Atlanta-based Novelis Inc. business unit of India’s Aditya Birla Group and Canada-based Matalco, meanwhile, have undertaken projects to build one or more recycled-content aluminum production facilities in the U.S. in the 2020s.
U.S. companies are not staying on the sidelines. Indiana-based Steel Dynamics Inc. (SDI) is building a recycled-content aluminum production facility under the name Aluminum Dynamics in Mississippi. Kentucky-based Owl’s Head Alloys, likewise, selected Mississippi for expansion and will work with Aluminum Dynamics.
Minnesota-based Spectro Alloys and the Ohio-based Ellwood Group have added capacity in their home states, and Indiana-based MetalX has selected a site in Defiance, Ohio, to expand its capacity to make recycled-content aluminum slabs.
Tabulating exactly how many tons of recycled-content aluminum will be made by all these facilities when the entire group is operational can be difficult. Not all projects are announced with a capacity figure, recycled content percentages can vary, and few facilities seldom operate at maximum capacity perennially. However, the numbers look significant.
Adding and subtracting

SDI’s Aluminum Dynamics subsidiary being built in Mississippi reportedly will have the capacity to roll 900,000 metric tons of recycled-content slabs annually, with those slabs coming from the nearby Owl’s Head plant and other sources.
The sizable new Novelis plant in Alabama will focus on consuming used beverage cans at its 600,000-ton-per-year aluminum sheet facility.
Hydro has added 120,000 tons of capacity in Michigan and has invested to increase the volume and types of scrap it can melt at its 90,000-ton-per-year facility in Kentucky. Additionally, Hydro’s extrusions business unit is adding 50,000 tons of capacity in Pennsylvania and has invested in technology to accept an additional 11,000 tons of scrap at its plant in Oregon.
In Ohio, MetalX and its technology vendors have designed a facility that will have the ability to produce as much as 200,000 metric tons of recycled-content aluminum slab annually.
The Matalco facility in Kentucky that opened last year is capable of producing more than 130,000 tons of recycled-content aluminum.
Gränges also has undertaken a project to add 25,000 tons of recycled-content aluminum casting capacity annually in Tennessee, while Spectro in Minnesota is in the midst of adding 60,000 tons of annual recycled-content metals production.
Just these investments, when operating at 100 percent capacity, have the ability to produce more than 2 million tons of recycled-content aluminum annually. Even accounting for the replacement of less-efficient capacity elsewhere and more realistic double-digit melt shop capacity rates, the planned capacity is poised to influence the import-export balance of aluminum scrap significantly.
According to U.S. Census Bureau statistics and a calculation by Recycling Today, in 2023, the U.S. exported about 33.6 percent of its generated aluminum scrap. While domestic furnaces melted 4.06 million metric tons of such material last year, some 2.06 million metric tons left by sea container or went over the border to Canada or Mexico.
For those reasons, the new capacity is unlikely to absorb the full 2 million tons that were exported. Also coming into play is whether compatible investments in overall U.S. manufacturing capacity will generate additional aluminum scrap.
No matter the import-export balance, another question to be asked is how will newly produced U.S. secondary aluminum be used?
Drivers, literally and figuratively
Aluminum has numerous markets, including construction and packaging, but part of the answer regarding its future use lies in the metals-intensive automotive sector.
In traditional internal combustion engine (ICE) vehicles, cast aluminum used in engine parts has been one driver of U.S. and global aluminum consumption. A study several years ago by London-based CRU predicted that while an EV revolution would damage the market for cast aluminum, it likely would provide new opportunities for makers of aluminum sheet.
A global trade association known as Alumobility doesn’t always distinguish between primary and secondary aluminum when predicting markets for the light metal within the EV sector.
The Switzerland-based group does take a clear position on how it sees aluminum’s role in the future of automotive production, writing, “Aluminum, which is 67 percent less dense than steel, is rapidly becoming the material of choice for automakers looking to create smarter, lighter, safer and more sustainable vehicles.”
Cast aluminum producers have long relied on scrap content, but makers of aluminum sheet in many parts of the world increasingly are tracking and trying to boost the recycled content percentages in their products.
Alumobility notes that the light metal as “infinitely recyclable” and says the production of circular aluminum is highly climate friendly.
The group adds that aluminum is used in ways that allow more than 90 percent of what is produced to be recovered for reuse, contributing to a more sustainable end-of-life recycling process.
“Aluminum is infinitely recyclable without any loss in its properties,” Alumobility says. “Compared to steel, aluminum recycling requires lower temperatures, resulting in energy savings during the recycling process.”
What percentage of EVs, ICE vehicles, building products and appliances made with aluminum will be produced in the U.S. compared with offshore is another variable that will help determine to what extent “made in America” secondary aluminum will be in demand.
Based on several big-ticket projects underway or recently concluded, several investors have cast votes of confidence that the U.S. can make and consume more recycled-content aluminum.
Get curated news on YOUR industry.
Enter your email to receive our newsletters.
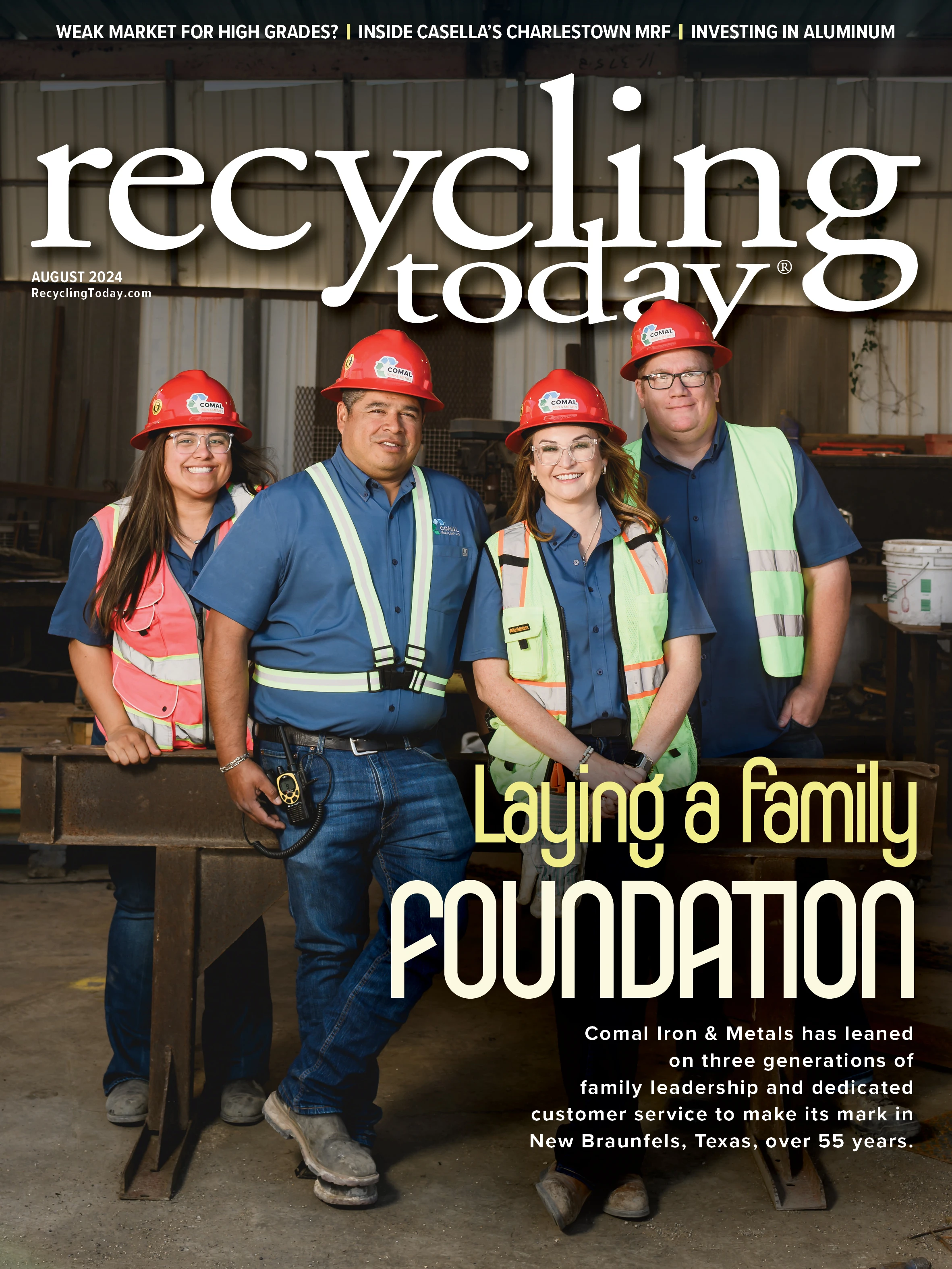
Explore the August 2024 Issue
Check out more from this issue and find your next story to read.
Latest from Recycling Today
- Unifi launches Repreve with Ciclo technology
- Fenix Parts acquires Assured Auto Parts
- PTR appoints new VP of independent hauler sales
- Updated: Grede to close Alabama foundry
- Leadpoint VP of recycling retires
- Study looks at potential impact of chemical recycling on global plastic pollution
- Foreign Pollution Fee Act addresses unfair trade practices of nonmarket economies
- GFL opens new MRF in Edmonton, Alberta