As more scrap dealers opt to install radiation detection equipment at their yards, the next question to ask is whether they would be better suited with a hand held system or a fixed system.
There are advantages and disadvantages with both processes. The biggest advantage to the fixed system, one typically located at the front end and the back end of the yard, is that the systems are automated. These larger systems are highly sensitive, making it more likely that any radioactive material would be quickly flagged.
While these fixed systems are sensitive, there are steps that need to be followed, including slowing the vehicle for a proper reading. Also, the density of the load can play a factor in detection. The less dense the better, Huckabee adds.
Another advantage to an automated system is that the machines work ”24-7,” Huckabee adds. There isn’t an issue with labor, which reduces the chance of error.
While these advantages make them popular with many larger processors, as well as consumers, the cost of having multiple fixed systems in place can be steep. For many smaller processors, the cost of the fixed system makes them prohibitive.
This is where the hand held systems can play a role. Hand held systems can be very sensitive, “if the operator has been properly trained [properly],” says Huckabee. Because of the nature of the hand held systems, it can take a much longer time to properly scan the load.
Also, while they are sensitive, with a hand-held system the operator would have to go over the material in a much more methodical way, slowing down the process of moving material through the yard.
Despite these drawbacks, many smaller operations find that the combination of lower costs and some safety issues addressed make the hand-held systems a more viable method to ensure that the scrap material being processed is radiation free.
Annaco Inc., a scrap metal recycler located in Akron, Ohio, the company has a fixed system at the entrance, as well as several hand-held devices.
Rick Robertson, Annaco’s plant engineer, says all material that is trucked in must run through the detection equipment. If the fixed system detects a dose of radioactive material, the company runs the equipment through the system several more times, reducing the possibility of detecting a “false positive” reading.
Once it is determined that the load does contain radioactive material, the company will pull the load to the side and use the hand-held detection equipment to find the source of the radioactivity.
Robertson notes that when the company first installed radiation detection equipment between 7-8 years ago, quite a few loads were flagged for contamination. However, as the company has used the equipment to inspect all the loads that are brought in, it is very rare that contaminated are being found, as customers are aware of Annaco’s detection abilities.
Robertson speculates that since suppliers have found out that all loads are being checked for radioactive material, they do not even attempt to bring the scrap to the Annaco site.
While receiving radioactive scrap is a hit-or-miss scenario, many of the larger scrap processors have put detection units in their yards.
William Skopelija, plant manager for the Burns Harbor, Ind., facility of PSC Metals, says that while the company has detection equipment on a truck/rail scale, the company rarely if ever receives radioactive scrap coming across its scale. The main reason, Skopelija says, is that the company handles only a select type of scrap, primarily prompt scrap. While there are chances of a radioactive material being commingled with a load, the chances are remote. “We have only had one incident that I can think of where we had some radioactive scrap,” he notes.
PLAYING THE ODDS. The potential to receive radioactive scrap often increases with lower grades of scrap, or material that is shredded. Because the company does not take in any shredded scrap, and has established markets for prompt scrap coming from a number of the steel mills in the area, the chances of having scrap contaminated with radioactive material are minimal.
Despite that, he notes that the expense of having a load get mixed with radioactive scrap is too high to risk not having the scanners.
While PSC Metals, as well as many larger facilities, have some combination of hand-held and stationary detection systems, the use is not as prevalent with smaller yards. Often these yards are more willing to take in material from peddlers, with supplies coming from a wide range of sources.
Even more so than scrap processors, for consumers detectors are a piece of equipment that they must have. Eric Stuart, a spokesman for the Steel Manufacturers Association, Washington, says that all of the members of the association have radiation detection equipment installed. SMA members are primarily mini-mills, who use ferrous scrap as their key raw material.
Because mini-mills are the destination for scrap from a potentially wide range of dealers and regions of the country (and nations of the world), there is a significant amount of duplication with detection equipment on their site. Detectors can be located at the gates, on a scale, in various types of equipment, and even in the bag houses.
Huckabee says that many of these mini-mills not only have duplicate systems, but often have set up systems that totally surround the scrap as it is delivered to the site.
Despite all the efforts to prevent the introduction of radioactive scrap into a manufacturing environment, the fact is that every once in a while some radioactive scrap eludes all the detection devices. While it is becoming rarer, there have been reports of some steel mills ending up with radiation contamination, forcing a shut down of their operations while a costly cleanup take place.
Sterenka, in the earlier interview, estimates that there have been more than 80 incidents where smelters or electric arc furnace plants have melted radioactive material in their furnaces. Further, he noted that in from 35 to 40 of the cases there were multiple scanning systems at the time of the incident.
“There is no absolute, 100 percent solution,” Sterenka added.
While detection equipment can be quite costly, Stuart estimates that the cost of inadvertently allowing radioactive scrap to enter the furnace could run anywhere from $10 million to $24 million, a significant cost. In addition to the lost time and cost of clean up, a company could jeopardize its reputation with the buyers of the finished steel.
While many scrap processors say the amount of radioactive scrap is minimal at best, over the past several years there has been some lobbying to allow for more radioactive material to be added to the scrap metal stream.
Late last year representatives of a number of firms met with U.S. Department of Energy officials to discuss proposals for recycling more than 13,000 tons of scrap nickel, most of which is stored at the Paducah, Ky., Gaseous Diffusion Plant.
It is DOE's latest effort to find a use for the nickel that was once used in production equipment at enrichment plants in Paducah; Ky.; Piketon, Ohio; and Oak Ridge, Tenn. The nickel reportedly has a low level of radioactive contamination.
While more scrap recyclers are looking to either install radiation detection equipment at their facility or upgrade for increased coverage, the equipment companies are reporting increased interest by sources outside the scrap metal industry. With the concern over the smuggling of radioactive material into the country, several equipment companies report seeing strong interest by port facilities throughout the United States.
Get curated news on YOUR industry.
Enter your email to receive our newsletters.
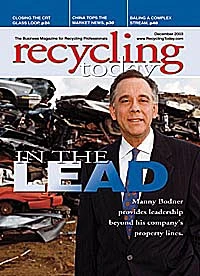
Explore the December 2003 Issue
Check out more from this issue and find your next story to read.
Latest from Recycling Today
- Green Cubes unveils forklift battery line
- Rebar association points to trade turmoil
- LumiCup offers single-use plastic alternative
- European project yields recycled-content ABS
- ICM to host colocated events in Shanghai
- Astera runs into NIMBY concerns in Colorado
- ReMA opposes European efforts seeking export restrictions for recyclables
- Fresh Perspective: Raj Bagaria