The U.S. is second to China as the world’s largest producer of metal castings, according to the American Foundry Society Inc. (AFS), Schaumburg, Ill. In 2007, U.S. metal casters produced more than 13 million tons of castings with a value of more than $34 billion.
With the automotive and light truck industry accounting for 33 percent of the metal casting industry’s total market, according to AFS data, the downturn in the U.S. auto sector has left its imprint on many metal casters.
With pipes and fittings accounting for 15 percent of U.S. metal casters’ total market, and construction, mining and oil field equipment accounting for 6 percent, many casters also are feeling the effects of the downturn in the housing and construction markets.
In addition to contracting end markets, the U.S. metal casting industry has had to contend with the effects of globalization. In 1955 the U.S. was home to nearly 6,000 metal casters. That number has decreased to 2,130 in 2009. According to the AFS Web site (www.afsinc.org), this is the effect of "increased foreign competition, regulatory burdens and some attempts over the last decade to position the U.S. more toward a ‘service economy.’"
Alfred Spada, AFS director of marketing, public relations and communications, offers his thoughts on how domestic metal casters have been affected by the downturn in the U.S. economy and the potential boost the 2009 American Recovery and Reinvestment Act (ARRA) could deliver to the U.S. metal casting industry.
Recycling Today (RT)
: In what ways has the foundry industry been affected by the slowdowns in the automotive and construction industries?Alfred Spada (AS): There are a couple of different ways to look at this from our perspective. For this conversation, I’ll divide our industry into two categories. Most of the people in our industry are die casters and the rest are sand casters, permanent mold and all the [other] processes that our industry uses. The reason I divide that is because typically 70 to 80 percent of the die casters’ customer base is automotive market. From the die casting perspective it has obviously been significantly affected by the slowdown in the automotive sector. For the last year, year and a half, it has been very tough. It is typical to see a die caster right now who is heavily involved in automotive producing at 50 percent of its production capacity.
One of the things that has always been tough for the North American manufacturers is getting into the Asian transplants. While the Asian transplants are down, they aren’t down nearly as much as the GMs, Chryslers, etc. of the world. The Asian manufacturers have a different way of approaching their supply base. While some North American die casters have had some success getting into the Asian transplants, most of them are still heavily tied to Big Three. As a result, from the die casters’ perspective, there are significant problems.
If you look at the metal casting industry as a whole, 33 percent of our production goes to the automotive market. That means that there are some metal casting facilities that are heavily involved in the automotive industry—some that are 80 to 90 percent—but overall, 33 percent of the industry is involved in the automotive sector. Guys are being affected; don’t get me wrong. Those who are heavily automotive are in similar shape as the die casting market segment. But we have a lot of guys who don’t ever touch it, so they are not even paying attention to what is happening in automotive. It is the general slowdown of everything else that has affected them.
If you talked to a lot of metal casters in October and November of last year, they were having a record year or near record year in 2008. Obviously the housing starts and automotive had been down for a long time. They weren’t being affected by those because those weren’t markets that they served. However, things dropped off of the face of the earth in November, December or the first of the year. That’s when everything hit us.
Construction for us is about 6 percent of production overall. Construction from a housing starts perspective has been a big problem; but, really it is one piece of the pie, and everything is down, and I don’t think construction is any worse than anything else.
There is a big segment of our industry from a construction perspective that some people may think of, and that is pipe. We cast a lot of pipe, and also we cast a lot of manhole covers, tree grates, basic municipal castings. Basically, those are 100 percent reliant on housing starts. That market has been down for a year and a half, two years. But it is very similar to automotive; it is very isolated. It is a small group of metal casters.
There are 2,130 casting operations in the U.S. That is all metals, all processes. When you are talking about facilities that are doing pipe, there are 12 or fewer facilities. And when you’re talking about facilities doing municipal castings, there are 10 or fewer facilities. Facilities tend to specialize in some of those market segments, and those are the facilities that got killed by those two groups, with very little hope for the near future.
RT
: Are there any sectors of the economy, such as home improvement or auto repair parts, that have helped some foundry companies remain viable?AS: We have a couple areas that are doing relatively well. Farm has remained relatively strong. It is down 6 to 10 percent by some estimates, but when you are looking at everyone else being down 20, 25 percent or more, it doesn’t look too bad for us. Health care is another market where we have seen some decent activity. The great thing about metal casting as a support industry is that we are so diverse in terms of our customer base. One of my favorite stats is that 90 percent of all manufactured goods contain a metal casting. We have these giant markets—construction, farm, auto—but there are all these little niches in all of these different markets, and in all of these niches, there are hundreds or tens of buyers of castings. It is odd because when you visit metal casting facilities you will have ones that seem to produce the same kinds of components, and one will be down 40 percent, while the other will be right where it should be. And there is no logic there other than that they serve different customers in those market segments.
Military so far is still a relatively positive market. Oil is still doing reasonably strong for some people for the last couple of months, but the overall oil numbers are terrible. There is not an easy answer to this question. It just seem like it really depends a lot on who its customers are in these lesser market segments that determine whether a metal caster is doing well.
We are finding that a lot of buyers didn’t understand where their inventories actually stood. Companies that were buying castings were doing so well for most of the last year and they were just buying, buying and buying castings and they had no idea how many castings they already had. When things slowed down, they were able to take a look at their inventories and realized they had massive stocks sitting around.
Other customers were not doing it that way. They knew exactly how things were being handled. They didn’t have to put breaks on.
RT
: What steps can foundry operators take to operate profitably with lighter or slower melting schedules? How can scrap suppliers stay attuned to any such operational changes?AS: Energy efficiency is really where this comes into. You always want to run your furnace as efficiently as possible regardless…You don’t want to melt metals slow necessarily because you have to get that metal to a certain temperature, and there is an optimal way to get that metal to a certain temperature.
What a lot of them do is consolidate shifts. Instead of producing over five or six days, they are only melting on three or four days because they don’t want to heat those furnaces up every single day. They are optimizing efficiency on the days that they are running those furnaces and on the other days they are cleaning castings or doing maintenance. Since the energy required for melting is one of our expenses, you want to optimize every time you turn on that furnace. If you have to produce 5,000 pounds of castings, it makes no sense to produce 1,000 [on each of] five days if you can produce 5,000 in one day.
INDUSTRIAL STIMULUS Alfred Spada, director of marketing, public relations and communications for the American Foundry Society (AFS), Schaumburg, Ill., says he is hopeful the infrastructure spending in the 2009 economic stimulus package will be a boon to the metal casting industry. The $787.2 billion package includes: • • • • Spada says he is unsure as to when metal casters will begin to feel the effects of the infrastructure projects in the stimulus package and questions whether construction equipment manufacturers already have enough castings in inventory to make the equipment that could be needed for these projects. The potential benefits of the stimulus package are not limited to infrastructure projects. The AFS has compiled a list of additional benefits metal casters could see as a result of the 2009 American Recovery and Reinvestment Act that is available at www.afsinc.org/content/view/722.
The one thing I can say is that you have to watch closely what happens in next two to three months. The belief is that once this thing takes off, there is not going to be a lot of open capacity six or nine months down the road. Metal casters are going to need as much iron and steel scrap as they can find. There is going to be significant demand in this industry, whether it is from the stimulus packaging to pull things through or whether it is overall demand from customers to pull things through. But the problems that we had a couple years ago when scrap prices were through the roof, I’m guessing it is going to get a lot worse than that once everything does pick up on a global scale, but in particular in our market because we are losing plants. So demands on the plants that are there are going to be higher and higher, and they are going to need the raw material to be able to met those demands.
The quality is always important. The cleaner the scrap, the better. When demand was really tight, people were buying material of less quality because that was all they could get their hands on. Now, it really has to be highest quality stuff possible because everyone has got to make as much profit as possible.
RT
: Is there anything within the 2009 American Recovery and Reinvestment Act that offers hope for foundry operators, and if so what?AS: Everyone loves the infrastructure stuff. If you are going to build bridges, you need castings. If you are going to build schools, you need castings. All the equipment to build those things needs castings. The question is, when is that going to kick in? A lot of the big OEMs may have enough inventory to cover what they need to build the equipment to meet these needs.
I shouldn’t forget the alternative energy stuff. In your average 1-megawatt wind turbine, there are about 10 tons of metal castings. That is a pretty small turbine these days. We [also] have castings in solar equipment and in biofuel equipment.
RT
: In what ways have trade policy issues affected the health of foundries operating in the United States recently?AS: It is a tough one for us. I’m not going to implicate the Bush administration necessarily, but when we are looking at a global economy, North American metal casters have obviously been affected by low-cost foreign sourcing. Last year, about 23 percent of the demand for metal castings in the U.S. was coming from outside the U.S.
There are questions as to what the "Buy American" provision in the stimulus actually means. I know there are rules in there about trading partners. I don’t know how the Democratic administration is going to approach that…Are they going to be more protectionist or not? For us right now, when you are talking about free trade, it has significantly affected U.S. metal casters.
The industry knows that it has to compete in the global economy. We want to level the playing field. I want that field to be at our level. It is critically important to maintain a manufacturing base, but it is also important to be aware of what your affect is on the environment.
RT
: What are the best-case and worst-case scenarios or forecasts facing metal casting companies in 2009?AS: Our 2009 numbers at this point look like we will be 20 percent down in production overall from 2008; that is all materials, all metals and all processes. We are looking at a pickup in the second half of year; the first half of the year is going to be slower.
Alfred Spada of the American Foundry Society can be contacted at alfred@afsinc.org.
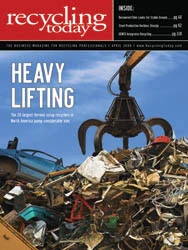
Explore the April 2009 Issue
Check out more from this issue and find your next story to read.
Latest from Recycling Today
- Aqua Metals secures $1.5M loan, reports operational strides
- AF&PA urges veto of NY bill
- Aluminum Association includes recycling among 2025 policy priorities
- AISI applauds waterways spending bill
- Lux Research questions hydrogen’s transportation role
- Sonoco selling thermoformed, flexible packaging business to Toppan for $1.8B
- ReMA offers Superfund informational reports
- Hyster-Yale commits to US production