As with many things in life, when purchasing wear parts most recyclers are reluctant to go for the lowest-priced products, fearing they may "get what they pay for."
|
Conducting ongoing cost-benefit formulas for wear parts can be a complicated process for recyclers who operate crushers and grinders, but it can pay off with better purchasing decisions.
Makers of wear parts say it is the only way for recyclers to determine which product is right for their machines.
LONGER LIFE
For several reasons, one of the performance measures used by recyclers when considering wear parts is the life of the product.
The greater number of operating hours a set of blow bars or hammer tips last, the more purchasers are getting for their money. Additionally, if there is a greater time span between replacing wear parts, the less overall downtime there is likely to be on a given project or in a month-long period.
Making cost-effective wear parts decisions—or getting the most for one’s money—is unquestionably a critical choice for recyclers of concrete, asphalt, wood and other C&D materials. Along with labor, power and transportation costs, wear parts make up an important fraction of the operating costs pie.
"The percentage of operating costs attributed to wear parts varies from operator to operator, but it is significant," says Jeff Hickey, a product manager with Kennametal, Latrobe, Pa. The company makes hammer tips and other cast parts used in tub grinders and other wood processing equipment.
Operators of concrete and asphalt crushing machines also must tally up wear parts purchases as an ongoing operating cost. Jeff Hillis, parts sales manager of Eagle Crusher Co. Inc., Galion, Ohio, says his company has been reluctant to pin-point a percentage figure to allocate to what the average concrete or asphalt recycler will spend on wear parts. "The problem is, it varies a great deal due to things like the abrasiveness of materials and the operator methods used to feed the machine," says Hillis.
Aggregates recyclers can do little to change their circumstances in terms of regional product differences, notes Hillis. "In Louisiana, if you’re crushing concrete with 80 to 90 percent silica, your wear costs could be substantially more than when crushing limestone-based aggregates somewhere like Indiana," he offers.
On the other hand, operators of impact crushers can monitor and change work habits to prolong blow bar life, Hillis contends. As an example, Hillis notes that in its research, Eagle Crusher has found "that if you keep the hopper at a constant fill rate, you reduce your costs not only in fuel savings, but you also lower your wear costs. We think it’s because the material flows into a position better where it can be crushed more efficiently."
Operators of both concrete crushers and wood grinding machines can also prolong the life of their wear parts by pre-screening material.
Wood grinder operators can keep their hammer tips out of harm’s way by keeping "unshreddables" (such as heavy steel objects) out of the grinder material stream, notes Hickey. "Operators can achieve lower costs by pre-screening their material; they’re not tearing up tips and burning up fuel grinding things that shouldn’t be ground," he remarks.
Although railroad tracks and anvils may be the types of unshreddables that come to mind, Hickey notes that this can be a broader category that can include "rocks, metal fence posts, wire—it could be anything, and it usually is."
THE RIGHT FIT
|
Matching wear parts to the task and the machine may seem like an obvious step, but in a fast-paced market with a lot of conflicting claims by manufacturers, this obvious step can get lost.
On the aggregates side, Hillis notes that even though recyclers can’t pick up and move away from more abrasive materials that might be found in one geographic region (or on one particular job site), they can prepare to take on these nastier materials. "For example, clean asphalt needs the very hardest blow bar you can find, because it’s soft," says Hillis.
Matching metallurgy to the task can be complicated, though. In the case of the asphalt mentioned above, "If it has metal contaminants, you need to move down the metallurgy scale," notes Hillis.
According to Hillis, "With cast wear parts, you’re walking a tightrope between the hardest possible material to avoid sliding abrasion, and a material that is forgiving enough to take the impact abrasion." Both types of abrasion work in different ways to wear down the surfaces of blow bars in an impact crusher.
The complicated truth, according to Hillis, is that "there is no one wear alloy that works across the board in terms of both wear and impact resistance."
The result has been the creation of a variety of available products, with Eagle Crusher alone selling a wear parts with a half-dozen different metallurgical alloys, according to Hillis. Other manufacturers offer additional metallurgical innovations, offering crusher operators a variety of choices.
Wood recyclers operating grinding equipment face similar choices, according to Hickey. "Using the right tip for the job, in terms of both geometry and chemistry, is a key consideration," he notes. "Kennametal offers a wide variety of tools for specific applications."
As with the blow bars used by crusher operators, makers of hammers and hammer tips for grinders make products targeted for specific applications, whether in the forestry or green waste field, mixed C&D processing or for asphalt shingles.
While the hammer tips are the most frequently replaced items, additional parts such as hammers, rods and screens also need to be replaced periodically. "The tips are the most frequently replaced item, but the others need periodic replacement as well," says Hickey.
He adds that an operator should avoid trying to save a few dollars by keeping a set of tips in place beyond their useful life. "If they let hammer tips go too long, they generally only do that once," he remarks. "Otherwise, the hammers wear out instantly as well, so you’re trying to conserve some tips that may have cost you $10 each but wear out hammers that may have cost you $80."
TIMELY ARRIVAL
Blow bars and hammer tips won’t last forever, and the more productive a work crew is, the quicker these parts will need to be replaced.
Such a situation makes the timely delivery and nearby warehousing of parts critical. Wear parts companies are finding that the "just-in-time" trend has caught on with crusher operators the same way it has elsewhere in the manufacturing world.
"For crushing contractors themselves, the trend is that they keep virtually no inventory on hand," says Hillis.
His company has focused on quick turnaround time on order delivery of wear parts to try to distinguish itself in the market. The company keeps suitable inventory on hand to fill most orders on the same day, currently shipping out 95 percent of its orders on the same day and 98.6 percent within 24 hours.
Hillis says crushing contractors do themselves a favor when they establish a close relationship with their parts suppliers. "In our case, we can then pick up on a customer’s buying habits and we can predict what they are going to need," he remarks. "Often times, our people will call a customer and mention that they haven’t ordered, and will provide a useful reminder. The customer is usually grateful, because it keeps them from incurring extra ‘rush’ freight charges."
This whole scenario is more likely, Hillis adds, if the crushing contractor will also take some time to develop the relationship.
The author is the editor of C&D Recycler and can contacted via e-mail at btaylor@cdrecycler.com.
Get curated news on YOUR industry.
Enter your email to receive our newsletters.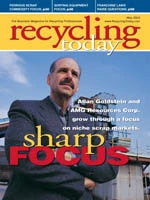
Explore the May 2003 Issue
Check out more from this issue and find your next story to read.
Latest from Recycling Today
- ReMA opposes European efforts seeking export restrictions for recyclables
- Fresh Perspective: Raj Bagaria
- Saica announces plans for second US site
- Update: Novelis produces first aluminum coil made fully from recycled end-of-life automotive scrap
- Aimplas doubles online course offerings
- Radius to be acquired by Toyota subsidiary
- Algoma EAF to start in April
- Erema sees strong demand for high-volume PET systems