John Morris, executive vice president and chief operating officer (COO) of Houston-based Waste Management (WM), shared his perspectives on the waste and recycling industry and his insights into WM’s operations during an interview with Recycling Today Editor DeAnne Toto during the 2020 Paper & Plastics Recycling Conference International. The broadcast event, which was hosted by the Recycling Today Media Group, publisher of Recycling Today, aired Oct. 20-22.
Among the topics Morris addressed were how WM is working to create more value out of the material entering its material recovery facilities (MRFs) and the changes it has made to improve the sustainability of recycling.

Morris said that in the last four to five years, despite low commodity market prices, WM has invested in its recycling infrastructure, either upgrading technology in its existing plants or building new MRFs. He mentioned what WM has dubbed its “MRF of the future” in Chicago, saying that facility’s degree of automation is improving efficiency. Inside that plant, WM is positively sorting recyclables with the help of automation. He credited positive sorting for “building a much better product.”
Automation and mechanization also are reducing employees’ exposure to potentially dangerous items in the material stream, such as needles.
Additionally, the increased use of automation has helped WM address issues related to staffing at its MRFs. “Those are challenging jobs,” Morris said. “And to find people that you can get in there … has traditionally been a challenge.”
“The way we conduct business looks a little different today, especially when you’re inside one of our facilities, because we want to make sure we can keep people safe.” – John Morris, executive vice president and chief operating officer of Houston-based Waste Management
Morris said the pandemic has presented additional challenges for the company regarding worker safety. “But it’s been also an opportunity for us to really demonstrate how we can take care of our people.”
Read on for more detailed responses from Morris on these and other topics in the edited excerpt of the interview below.
Recycling Today (RT): What potential threats keep you up at night as the COO of Waste Management?
John Morris (JM): Well, you know there’s not a lot that keeps me up at night. I will tell you, though, obviously at the onset of this pandemic, we wanted to keep our people safe first and foremost. And, certainly, there were a few sleepless nights in the beginning of making sure that as a provider of essential services we were going to be able to do that. The way we conduct business looks a little different today, especially when you’re inside one of our facilities, because we want to make sure we can keep people safe.
The good news is, while we’ve certainly had some employees and their families who were impacted personally, by and large, we’ve kept our folks safe, and it hasn’t impacted any one of our facilities in a disproportionate way.
I wouldn’t say our recycling business keeps me up at night. Certainly, we’d like to be further along in really reinforcing the foundation of the business. We’ve spoken publicly about moving to a fee-for-service model, being less reliant on commodity prices to drive the sustainability of the business. You know, recycling has to be economically sustainable in order to be overall sustainable for our customers.
RT: The Advanced Disposal Services (ADS) acquisition was a significant step for the company. What about that acquisition made it attractive to WM?
JM: Well, you know, as a compliment to Richard [Burke, ADS CEO] and the team over at Advanced Disposal, they built a really strong company with strong assets, and we felt like those assets combined with the WM assets in those regions were going to make for a stronger company. Part of our evaluation aside from the physical assets was also the people and the culture there. And we felt like they would be a really good fit.
RT: What about your acquisition strategy over the next five years more broadly?
JM: We’re going to be focused in the real estate where Advanced had assets, and we’re going to work to combine those assets and those folks and make sure we take care of our customers.
I think outside of the real estate where Advanced exists, you’re going to see the same strategy. We’re going to continue to look for the right opportunities in the M&A space, but we’re going to continue to be disciplined about it.
RT: How might WM be looking to broaden its business?
JM: For the last decade-plus, we’ve always kept an eye on what was happening in certain areas of technology advancement, and we’ve been pretty public about the fact that if we can find ways to take elements of what is now the waste stream and create higher value materials out of that, that’s an area where we’re going to continue to look. There’s been certainly a lot of technology that has been tried and, interestingly, a lot of those technologies work, but whether they’re scalable and whether they’re economic, those are two really important bars. So, to the extent that the waste stream starts to migrate to different forms of a commodity stream, where we can convert elements of the waste stream into higher value materials and have a higher and better use, we’re going to continue to look to do that. When you think about investments outside of the traditional spaces, that’s the one area where we continue to keep an eye on that to make sure that we’re more at the tip of the spear, if you will.
RT: How do you see WM treating expansion in the recycling space?

JM: In the last four or five years, we’ve probably invested well over a quarter of a billion dollars in our recycling infrastructure, both in upgrading technology in existing plants and building out some new technology. And I think that the one that sticks out and we’ve talked about a lot is the MRF of the future in Chicago. We’re very, very pleased with that because it does a couple of things. One, it’s automating and making us more efficient. We’re doing positive sorting with that equipment. And the last piece really is, one of the struggles around recycling, at least for us, has been staffing those facilities. Those are challenging jobs.
What some of this technology advancement like the plant in Chicago does for us is it solves a few things. One, the quality coming out of the facilities is better, the efficiency of the facility is better, and it’s solving a real challenge we’ve had around keeping labor inside. When you look at investments going forward, over the next three or four years, we think we’ll have advanced technology to some degree in virtually every one of our facilities.
RT: Does that advanced technology center around artificial intelligence and robotics largely?
JM: Actually, the plant in Chicago does not; it relies more on optical sorting. We do have eight robots deployed around the country, and we’re continuing to look for opportunities to use robotics in the plant for a lot of those same reasons.
RT: You mentioned positive sorting and that you are finding that to be a much more effective method than the negative sorts. Why might that be?
JM: As single stream has become much more prevalent over the last decade and a half, while it’s promoted recycling, it’s also brought in a lot more contamination. That’s one of the things we struggle with both from a quality of material standpoint but actually also from a safety standpoint. A lot of what we see coming into the plant, not only is it not good for the outbound material, but in a lot of cases when it’s batteries, aerosol cans, those kind of things, it can present some safety issues for us.
When you look at positive sorting, like we’re doing in Chicago and a handful of other places, we’re building a much better product. Obviously, when you’re doing it through an automated or mechanized process, you’re not exposing folks to some of those other things.
RT: You mentioned safety around COVID-19 earlier. Can you talk a bit more about safety and how innovation could potentially change the industry?
JM: Some of the risks are to some of the folks on the sorting line. So, clearly, as we mechanize or automate some of the sorting and the exposure to some of those materials, we’re obviously going to reduce the risk. And what you see, for instance, in the plants, we’ve got more advanced technology that folks are not interacting with the material stream as much as they’re more quality control.
RT: Given the risks that are inherent in that incoming material, are you doing more at the front end to evaluate those incoming loads and just flat out reject certain materials or loads?
JM: As the scrutiny over commodity quality has risen over the last handful of years, making sure that we were equally as diligent on the front end, screening that material coming in, has certainly been an area of focus for us. We use technology to centralize a lot of the screening processes. So, what we’re doing is we’ve used some strategically placed camera technology in our facilities where we can get a better view without having to expose as many folks to being on an active tipping floor. We’ve seen some success from that as well.
RT: Do you believe legislation plays a role in strengthening recycling and what form might that take?
JM: Minimum content requirements would certainly be one area. Minimum content requirements, at least in my mind, provide a base for those markets.
RT: Where do you see WM in five years?
JM: This is a strong company. We’ve been a public company since 1971. I think you’re going to see a lot of technological advancements. We talked a little bit about what’s going on in the recycling space, about what technology is doing to change that business. I think technology and other parts outside the recycling space are going to continue to evolve our business.
And when we think about attracting the workforce of the future and what the future work looks like, you’re going to continue to see technology take a more prevalent role in defining those jobs. And I think that’s the fun part.
Look at what is happening now around material processing, around remotely operating heavy equipment in some of our sites. When you look at the advancements around fleet, whether it’s going to CNG (compressed natural gas) or pilots where we’re dealing with electric vehicles, or you look at automation of the roles, whether it’s in the MRF or in the collection side of the house, I just think the rate of change is obviously increasing everywhere, but specifically for our industry.
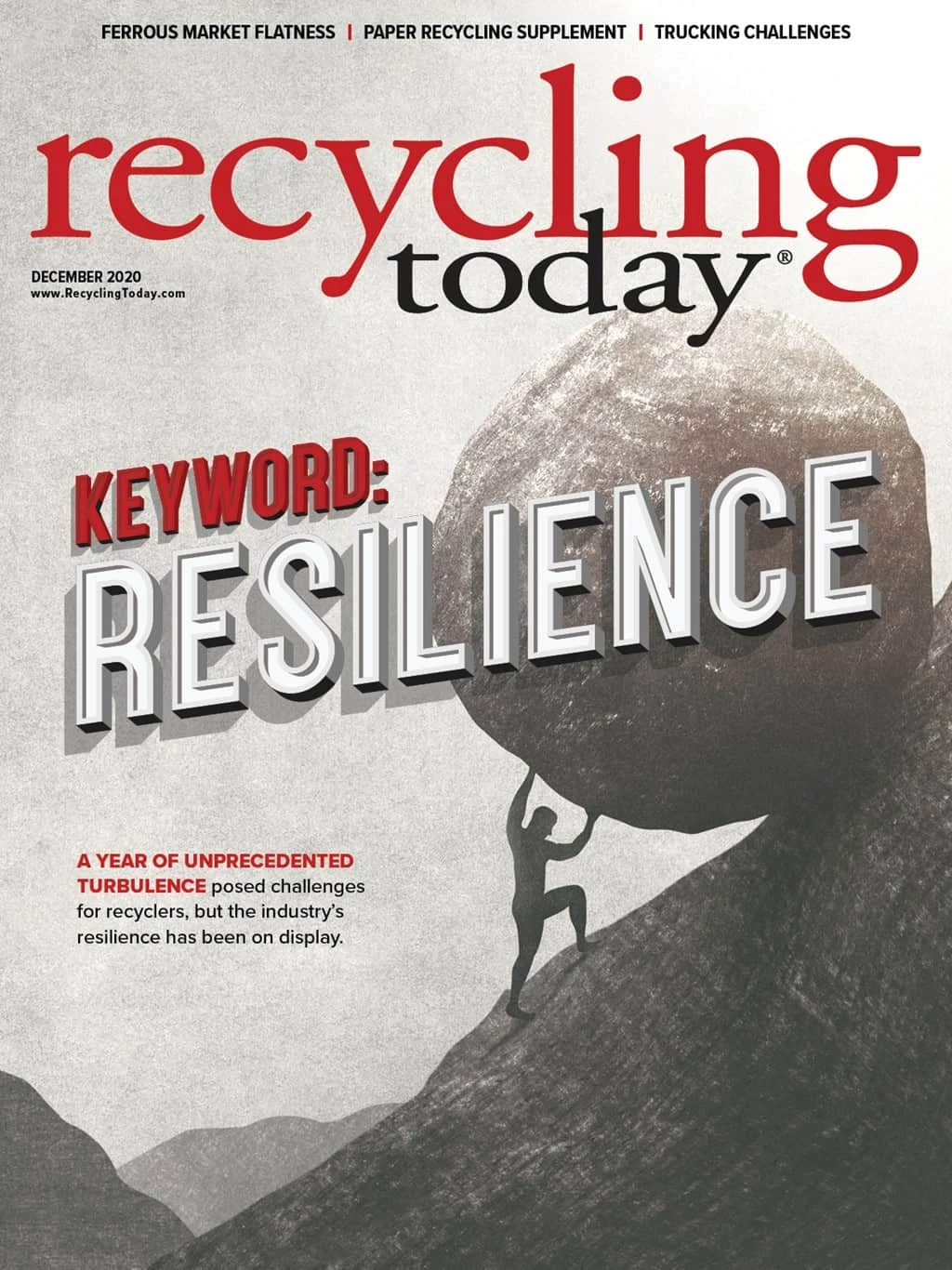
Explore the December 2020 Issue
Check out more from this issue and find your next story to read.
Latest from Recycling Today
- Athens Services terminates contract with the city of San Marino, California
- Partners develop specialty response vehicles for LIB fires
- Sonoco cites OCC shortage for price hike in Europe
- British Steel mill’s future up in the air
- Tomra applies GAINnext AI technology to upgrade wrought aluminum scrap
- Redwood Materials partners with Isuzu Commercial Truck
- The push for more supply
- ReMA PSI Chapter adds 7 members