Leaders are emerging in the quest to turn scrap tires into marketable secondary commodities.
(To view the Top 20 List Click on the following line -- Top 20 Tire Processors)One need look no further than The Simpsons to obtain the "pop culture" view of tire disposal and recycling. Episodes in the show’s first several seasons, created in the early 1990s, made several references to the ongoing Springfield tire fire, an animated tire stockpile complete with flames and plumes of black smoke.
Thankfully for legitimate tire recyclers, references to the site—one of several civic attributes that helped define the Simpson family’s hometown of Springfield as less than a paradise—have diminished over the years, perhaps a reflection of the progress recyclers and government agencies have made toward addressing the issue of tire stockpiles and fires.
Near Misses |
Several companies that did not make the list of the "20 Largest Tire Recyclers" are handling between 1 million and 2.1 million PTEs, putting them in a position to move into a spot on the list with some corporate growth. Among these companies are Manhantango Enterprises Inc. of Liverpool, Pa.; Watertown Tire Recyclers, Watertown, Wis.; Global Tire Recycling of Wildwood, Fla.; High Tread International of Lockport, N.Y.; West Coast Rubber Recycling of Gilroy, Calif.; Buckeye Tire Recycling of Youngstown, Ohio; and Tri-Rinse Inc. of St. Louis. Additionally, there are several companies believed to process enough tires to have made the list, but for which editors were unable to confirm a 2003 PTE number. Among these companies are Liberty Tire Recycling of Pittsburgh; Crumb Rubber Manufacturers of Compton, Calif.; CB Tyres Recycling Resources LLC, Glendora, Calif.; American Tire Disposal, Fontana, Calif.; Magnus Environmental Corp., Wilmington, Del.; Auburndale Recycling Center, Auburndale, Wis.; Alternative Fuel Source Inc., Odessa, Mo.; J.P. Routhier & Sons, Littleton, Mass.; and Merrick Construction Co., Cottonport, La. And there are consumers of significant amounts of tires, such as RB Rubber Products Inc., of Portland, Ore., that are performing some of their own processing and would make a separate list of largest tire consumers. |
Beyond winning a public relations battle, the next hurdle for the tire recycling industry to clear, some would suggest, is for the secondary commodities produced by scrap tires to have a greater value to end users. Only then can tire recycling move into the ranks alongside metals and paper recycling as a serious secondary commodities business.
PROFIT MOTIVE. In many other nations (including in some provinces in Canada), legislated mandates and funding mechanisms have been put in place to keep tires out of landfills and to discourage the illegal dumping of tires.
Legislators in most U.S. states have also enacted programs (often funded by per-tire recycling fees collected when new tires are purchased) to discourage dumping and to encourage tire recycling.
These programs have helped establish collection and processing infrastructures in most states, as well as the critical end markets needed to close the loop in some locations.
The state programs as well as the tipping fees tire recyclers can charge to take in whole tires that are not usually welcome at landfills have helped provide a workable model for tire recycling companies. But the nature of the U.S. political climate will most likely mean that for tire recycling to establish itself on firm footing, it will need to continue to seek out higher-value end markets that can yield a heftier revenue stream.
Right and Wrong |
More than 30 of America’s 50 states have created funds and/or enacted fees as a means of addressing the illegal dumping and stockpiling of tires, according to Michael Blumenthal, senior technical director of the Rubber Manufacturers Association (RMA), Washington. While the intentions of legislators were good in almost every case, not every state program has succeeded in boosting the efforts of tire recyclers in collecting, processing and nurturing end markets, says Blumenthal. A common problem the last three years—as state after state has seen black ink turn to red in its overall budget—is the practice of states pillaging their tire funds to divert the money to other purposes, often critical social or educational programs. In addition to the emergency re-direction of funds, some states don’t direct the funds toward actual recycling efforts in the first place, according to Blumenthal, citing Pennsylvania as an example. In Texas, money went toward a concerted effort to shred problematic stockpiles. But, says Blumenthal, not much consideration was given toward the development of end markets for the shreds, or even for the hauling of the shreds off site. The result is stockpiles of whole tires turned into stockpiles of shredded tires, he says. Among states offering better models are Florida, Iowa, Illinois and Minnesota, says Blumenthal. He says one hard-working, knowledgeable regulator or public official can make a critical difference in any given state. "Each one of those states have or had a champion in their state environmental agencies who oversaw the scrap tire program," he declares. |
That goal is certainly on the mind of the CEO of the largest tire recycler in the U.S., Recovery Technologies Group Inc. (RTG), Gutenberg, N.J. "In every material stream, you have to get to those higher-value chains," RTG CEO Marty Sergi told Recycling Today for an October 2003 story. "Purely as tire-derived fuel (TDF), I don’t think this industry can ever be very attractive to investors. Economically, we want to keep moving the ladder away from TDF. If you can sell a product for $300 to $500 per ton instead of $50 per ton, you no longer have a waste product."
Michael Blumenthal, senior technical director with the Rubber Manufacturers Association (RMA), Washington, concurs with Sergi’s statement. "That’s exactly what we’re trying to do—create a commodity," he remarks. Part of the role his organization can play is to create and to help uphold standards for commodities derived from scrap tires, whether they are used as a turf additive, an asphalt pavement ingredient, playground material or as manufacturing feedstock. "Without these commodity standard formats, we’ll always be at the bottom of the food chain. With standards and information, you go up the food chain."
Blumenthal notes that tire-derived fuel, "is the biggest market now," but says that unless the higher-value crumb rubber and clean shred markets can be expanded, it will be difficult for tire recyclers to expect greater revenue for their end products.
However, owners of for-profit businesses must also be wary of flooding end markets that aren’t truly hungry for processed materials. America’s third largest tire recycler, GreenMan Technologies, Lynnfield, Mass., has built its business up by marketing itself as a reliable supplier of TDF to cement kilns and other TDF users. In many cases, GreenMan is supplying whole tires as kiln feedstock.
"We needed to focus on established markets and develop products for those markets," GreenMan chief financial officer Chuck Coppa told Recycling Today in a 2002 feature, regarding a GreenMan corporate board decision in 1997 to focus on the TDF market. "We [had been] devoting valuable corporate resources toward developing markets for products instead of products for markets," he says of earlier GreenMan efforts to make retail products from its scrap tire stream.
TAKING IT IN. To be among the largest tire recyclers in North America as of 2004, companies are either tapping into the end-of-life tires collected by retailers, cleaning up the stockpiles left by earlier mismanaged collection efforts or combining the two approaches.
RTG Inc. has worked to develop relationships such as those it has with Ford Motor Co. and Wal-Mart to help it recover newly-generated scrap tires. (See "Home Field Advantage," Recycling Today, Oct. 2003.)
Lakin General Corp., based in Chicago and with its Lakin East and Lakin West subsidiaries based in West Haven, Conn., and Santa Fe Springs, Calif., respectively, also serves some of America’s largest retailers. According to its Web site, Lakin uses a fleet of trucks as well as rail shipping to direct scrap tires toward its processing centers. The company resells some tires, makes die-cut synthetic products from others and produces TDF from the remainder of its collected scrap tires.
GreenMan Technologies is among the companies tapping into both streams. Coppa told Recycling Today that GreenMan has "relationships with all of the large tire manufacturing companies" as a means of tapping into the 280 million scrap tires turned in annually to dealerships and repair shops. At the same time, GreenMan seeks out clean-up projects to help procure tires, especially in the seasonably slower months for retail tire generation.
On the East Coast, Emanuel Tire Co. of Baltimore produces some 124,000 tons of secondary commodities with the tires it collects, serving the TDF market and also making playground and horse arena covering material.
On the Pacific Coast, Tire Disposal & Recycling Inc. of Portland, Ore., keeps three processing facilities busy churning out shreds for TDF and civil engineering applications as well as crumb rubber.
Florida Tire Recycling Inc. of Port St. Lucie, Fla., handles the equivalent of 33 percent of the scrap tires generated in the Sunshine State. In addition to TDF, the company also makes crumb rubber, a playground surface material and its RubberRock® drainage aggregate-substitute product.
In Winston-Salem, N.C., TIRES (Tires Into Recycled Energy & Supplies) Inc. focuses on crumb rubber production, selling the crumbed product into asphalt paving, athletic field and compression molding applications, according to TIRES president David Forrester.
Integrated Inc., with locations in Buffalo, Pittsburgh and Bayonne, N.J., serves a chain of potential end markets, starting with resalable used tires and also including civil engineering applications and TDF.
According to the company’s president, Guy Mozzicato, Meridian Inc. of Plainfield, Conn., was able to sell many of the 4.5 million tires it handled last year for reuse. Others were turned into casings or used as TDF.
Further west in Fountain, Colo., Midway Tire Disposal/Recycling concentrates on baling tires into 1-ton bales for civil engineering applications, such as road base or lightweight fill.
Mac’s Tire Recyclers of Saltillo, Miss., collects scrap tires throughout the Southeast, according to the McPherson family, which operates the business. A low-speed, high-torque shredder followed by another secondary shredder convert Mac’s 4.2 million PTEs (2003 figure) into a consistently-sized chipped TDF product.
Cleaning up stockpiles is an important source of tires for Champlin Tire Recycling Inc., Concordia, Kan. The company handles 4 million PTEs annually—many coming from stockpiles in Kansas and bordering states. A portion of the company’s scrap tires are converted into manufactured products, such as outdoor tables and benches.
Sacramento, Calif.-based Waste Recovery West Inc. collects scrap tires in several western states and churns out a variety of end products at its four processing facilities, including crumb rubber, TDF, re-treaded tires and civil engineering products.
Also based in California, Golden By-Products Inc. specializes in 2-inch TDF, ¾-inch ground cover and tires prepared for civil engineering applications. The Ballico, Calif.-based company handled some 3.8 million PTEs in 2003.
In White Pigeon, Mich., Entech Inc. specializes in handling truck and off-road vehicle tires. In addition to producing TDF, the company makes crumb rubber for turf applications and a drainage product used with septic systems and at landfills.
Utah Tire Recyclers strives to convert as much of its 3.5-million-PTE stream into crumb rubber. The company also serves TDF customers as well as providing alternative daily cover (ADC) for landfill customers.
Monte Niemi and the staff of First State Tire Recycling, East Bethel, Minn., concentrate on serving civil engineering markets, including using use scrap tire chips as lightweight fill called Recycled-Tire Engineered Aggregate. The R.-T.E.A. has been approved for road repair use in Minnesota. First State Tire collects more than 3 million PTEs annually, including using portable shredding equipment to service remote locations.
BAS Recycling Inc. of San Bernardino, Calif., focuses on crumb rubber, including handling tire buffings produced in the re-treading process. The company sells some of the 35 million pounds of crumb rubber it makes annually to makers of molded products, such as producers of parts used in friction brakes.
In Flint, Mich., Environmental Rubber Recycling obtains many of its 3 million PTEs from stockpiles and concentrates on TDF markets with its end product. On its Web site (www.primary power.com), the company says its scrap tire feedstock helps generate 128 megawatts of electricity annually.
Bill Vincent’s Colt Inc. of Scott, La., collects 2.5 million PTEs annually, with tires processed to serve the TDF and civil engineering markets. Vincent credits an effective tire collection program in the state of Louisiana for keeping tires away from illegal dump sites and directing them toward the facilities of legitimate recyclers.
Using a variety of collection methods, processing techniques and end market focuses, entrepreneurs are finding ways to turn America’s unwanted tires into products that are worth a second look.
The RMA’s Blumenthal notes that many of the older tire stockpiles are disappearing from the American landscape, thanks in large part to state governments reacting to the high-profile tire fires and mosquito breeding grounds (immense stockpiles) of the past.
The best remedy to keep those high-profile problems from re-occurring will be an effective and profitable scrap tire recycling infrastructure.
The author is editor of Recycling Today and can be contacted via e-mail at btaylor@RecyclingToday.com
Among the Missing?
If you work for or know of a company that you suspect should be on this list but was not contacted (or did not respond), please let us know and we will make sure to let our readers know. Editor Brian Taylor can be contacted via e-mail at btaylor@RecyclingToday.com.
Get curated news on YOUR industry.
Enter your email to receive our newsletters.
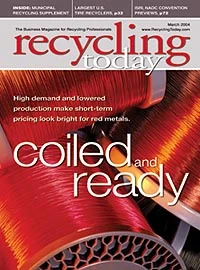
Explore the March 2004 Issue
Check out more from this issue and find your next story to read.
Latest from Recycling Today
- LumiCup offers single-use plastic alternative
- European project yields recycled-content ABS
- ICM to host colocated events in Shanghai
- Astera runs into NIMBY concerns in Colorado
- ReMA opposes European efforts seeking export restrictions for recyclables
- Fresh Perspective: Raj Bagaria
- Saica announces plans for second US site
- Update: Novelis produces first aluminum coil made fully from recycled end-of-life automotive scrap