
In the last year, actions occurring in China have brought a great deal of turmoil to the plastics recycling industry in North America. First, China introduced its National Sword campaign in February 2017, which cracked down on imports of scrap into China. Then the Chinese government banned imports of
These actions have left some material recovery facility (MRF) operators and plastic scrap traders that relied heavily on that export market considering their options.
Some traders have decided to vertically integrate their businesses by adding the technology and know-how needed to produce recycled plastic pellets. Two examples are GDB International of New Jersey and Avangard Innovative of Houston. Both companies collected, sorted and traded plastic film from retail and grocery stores. Now, they also are producing recycled pellets from the film they collect.
Sunil Bagaria, president of GDB International, says his company made the move in response to China’s actions and to show its generators more value can be realized and shared in plastics recycling. “We will help them see that recycling can pay. It has to make economic sense; only then will the recycling story be successful.”
Avangard manages approximately 100 million pounds of low-density polyethylene (LDPE) film annually from the retail sector and other generators. Avangard Chief Operating Officer Jon Stephens has said that roughly 50 percent of the LDPE scrap the company handles will flow through its pelletizing operation.
Vertical integration has been taking place in the manufacturing sector even before China’s scrap import restrictions. Composite lumber manufacturers Trex and Fiberon are two such examples. Trex added recycled linear low-density polyethylene (LLDPE) pellet production in 2015, while Fiberon began recycling high-density polyethylene (HDPE) and LDPE into pellets in 2014. (See “Becoming its own supplier” for more on Fiberon’s operations.) There’s also Unifi, which recycles polyethylene terephthalate (PET) bottles in North Carolina to produce its Repreve fabric.
MRF operators also are exploring the production of recycled plastic flake and pellets. The subject of this issue’s cover story, Urban Polymers, is a division of Canada Fibers Ltd. – Urban Resource Group, a Toronto-based MRF operator
“We chose to enter the reprocessing space to complement our sorting services at our Ontario MRFs in a way that secures local end markets for these commodities and makes Urban Resource Group vertically integrated, adding more value for our customers,” says Daniel Reshef of Canada Fibers Ltd. – Urban Resource Group.
Added value is a theme that runs through many of these companies’ decisions to vertically integrate, prompting the question: How are you adding value
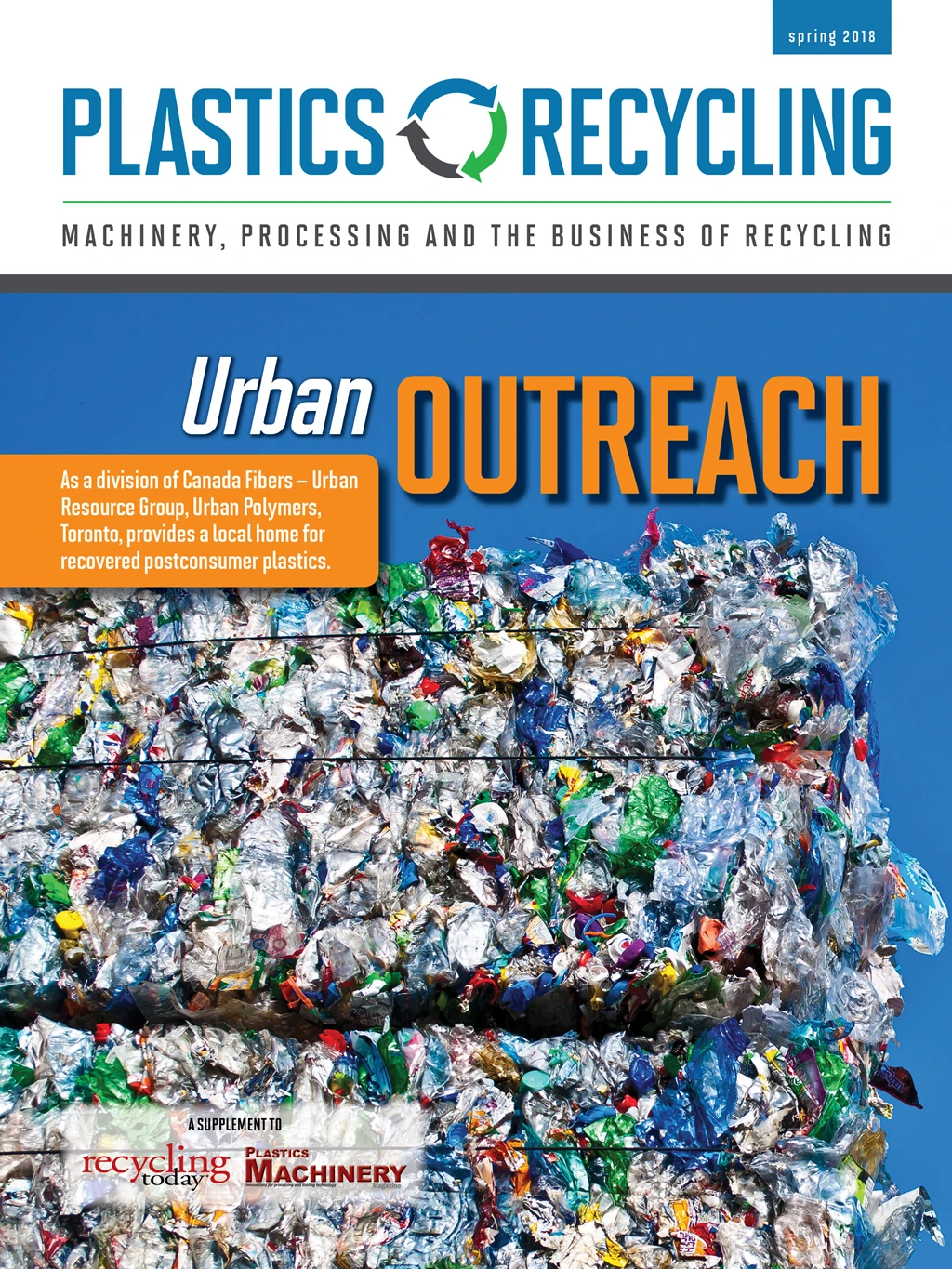
Explore the May 2018 Plastics Recycling Issue
Check out more from this issue and find your next story to read.
Latest from Recycling Today
- Hyundai adds dealer in Wisconsin
- Study finds recycling symbols largely recognizable
- Reworld announces executive leadership transitions
- Longtime paper industry veteran announces retirement
- Aurubis CEO says its metals play vital role
- Steelmakers await impact of tariff policy
- Radius loses money, says merger on track
- Electrostatic technology vies for role in ASR sorting