
Delivering the best solution

Van Dyk Recycling Solutions has evolved with the recycling industry. Originally founded in 1984 as Van Dyk Baler Corporation, in 2012 the name was changed to Van Dyk Recycling Solutions (Van Dyk) to reflect the firm’s successful movement into recycling system integration.
Van Dyk’s original mission, to represent Bollegraaf balers in North America, reflects what still drives the company today; to offer best-in-class processing solutions.
“We’ve always been driven by a collaborative approach with our customers to understand their requirements and provide processing technology to meet that need,” says Pieter van Dijk, founder and president.
“We have invested a great deal to understand what technology is available but also to understand how it can be best applied and then integrated into a cost-effective recovery plant,” says Pieter van Dijk.
“That’s the hard part, getting the integration correct and seamless. We have decades of experience doing that, more than any other provider,” shares Erik van Dijk, executive vice president and COO.
While Bollegraaf Recycling Solutions equipment provides the core success to Van Dyk’s designs, Van Dyk has continually leveraged cutting-edge technology from other globally leading suppliers like TOMRA and Pellenc (for optical sorting) and Walair (for air separation systems).
As material streams continue to evolve, it drives the need for new and different processing methodologies. Van Dyk has always been committed to diligently researching new technologies that could help improve its customers’ bottom lines.
“Today, we’re seeing the value of auger screens, and Van Dyk has partnered with Günther screens, the global leader and originator of spiral shaft screening technology,” Erik van Dijk says.
“We are constantly searching the globe to find the best solution for our clients. We compare the technology out there to the customer’s goals and needs and put together the design we know will work best,” says Pieter van Dijk.
The culmination of experience

Van Dyk’s newest startup, a 40-tph facility built for WM in Houston was modeled after the company’s successful designs of the recent past. Pieter van Dijk led the design team by posing this question: “How can we take a design that we already know works and use today’s technology to make it more highly automated and more efficient?”
The resulting system incorporates 14 optical sorters cleaning up paper and containers to make clean SCN, SRP and mixed paper grades. All fiber and container grades are sorted and quality controlled by optical sorters. There are only 7 human sorters needed throughout the facility (4 on presort, 2 on OCC quality control and 1 on aluminum QC).
A standout of the system’s state-of-the-art technology is DEEP LAISER, an artificial intelligence device that can recognize and eject black plastics (which cannot be seen on the infrared spectrum). DEEP LAISER is implemented on the SCN sort line.
“This is the best system currently running in North America,” says Pieter van Dijk. “It is the culmination of all knowledge and experience gained from our facilities built to date.”
Van Dyk University

A level of training unavailable elsewhere
As material recovery facilities (MRFs) and downstream processing operations become increasingly automated and sophisticated, understanding the technology and maintaining the equipment are vital.
Seeing this, Van Dyk Recycling Solutions made an industry-leading investment in training. In 2016 it opened Van Dyk University to educate customers on the ever-evolving technology in modern MRFs. Located right next to the company’s 19,000-square-foot test facility, Van Dyk University offers both classroom and hands-on education.
Programs include baler and optical training. Coursework includes electrical, mechanical and hydraulic systems. Troubleshooting and maintenance are always part of the curriculum.
“These programs are designed to train our customers to become self-sufficient in supporting their equipment,” comments Mark Neitzey, sales director at Van Dyk.
The customers’ view

“Top notch, very knowledgeable and very informative instructors,” says Anthony Ortiz of Republic Services’ Fort Worth, Texas, MRF, of the Van Dyk University staff.
Van Dyk University benefits from instructors who are steeped in industry knowledge. This ensures they have the technical knowledge and industry background to break it all down for course attendees.
“The instructor’s expertise is amazing, and he was very effective in explaining things clearly,” says Ernesto “Neto” Valencia of Homewood Disposal, Chicago.
“It was great. Every topic was taught in-depth, then the hands-on troubleshooting was good to gain experience,” continues Valencia.
“The training was easy to follow but still in-depth,” says Justin Carnes, Murphy Road Recycling, Berlin, Connecticut. “[We received] great feedback on our questions. The instructor was obviously full of knowledge and experience.”
“By training our customers’ technical teams on how to do routine maintenance and troubleshoot their equipment, we help them to increase uptime availability and lower costs,” says Pieter van Dijk.
“Our baler rebuild facility, a 9,500-square-foot facility in an interconnected building, is adjacent to the Technology Center and allows participants in a training program to also work on balers,” adds Neitzey. “You can’t do that anyplace else.”
Investing for the future
“Our job has always been to provide customers with the best possible processing technology and the knowledge and understanding of how to maximize that investment,” says Pieter van Dijk.
The Material & Technology Center on Van Dyk’s Norwalk, Connecticut, corporate campus includes Van Dyk University, its industry-leading test center and its baler rebuild shop. The complex provides resources to keep pace with the ever-changing marketplace.
He says, “We understand that our customers face an evolving ton in terms of material composition. We’ve seen the changes because of our long experience in the industry. We also appreciate that labor shortages, productivity demands and recovery and purity requirements create a very demanding operating environment.
“Being in touch with our customer demands led us to make the investments in not only a university-quality training facility but the testing facility, which allows hands-on training. Having our baler rebuild shop right there also made sense, again creating an opportunity to train but also to get hands-on experience,” says Pieter Van Dijk.
“It was a huge investment, but it was the right thing to do to support our customers and the industry’s future,” he continues.
Comprehensive test capabilities

The 19,000-square-foot test facility is the industry’s largest and most sophisticated. It is outfitted with a processing line capable of replicating in-plant operations.
The processing line boasts a pit conveyor that feeds a line with four optical sorters, two screens, an elliptical separator and an air system.
“This is the largest testing facility of its kind in the world,” shares Pieter van Dijk. “It’s designed to allow our customers the opportunity to test any equipment configuration on their material to precisely know the results that can be achieved.”
The test facility is complemented by an 18,000-square-foot receiving and storage facility for material to be tested. This allows customers, brand owners and others wishing to conduct tests to have their materials delivered to the test center. Once materials are on-site, tests can be run to demonstrate results.
Typical tests might be how SOP (sorted office paper) can be made from mixed paper, to understand the recoverability of packaging for certain CPGs (consumer packaged goods) from the material stream, to validate the purity levels of RDF fuel products and more.
The second generation widens its involvement

Growing up, Florian van Dijk was always exposed to the company founded by his father, Pieter van Dijk. He’d learned a lot about the business through family conversations and meeting many of the people who worked there. Florian had his first real exposure to the business of Van Dyk Recycling Solutions, however, after graduating from Tufts University in 2019. He did an internship working directly for his father.
The project was to help create a vision and scope document looking at the company’s future. That project helped him understand the tremendous opportunities the company had.
Florian van Dijk says, “There was never pressure to join the family company. The opportunity was there, but it was clear we really had to want it. It wasn’t expected.”
Florian set out to chart his own course, first doing some work in politics and then taking a job in the mortgage business.
“It was a great opportunity at the perfect time. The mortgage refinancing business was hot, and we were able to help a lot of people by lowering their mortgage payments.
“It felt good,” he says. “And it taught me that building relationships and trust is one of the most important aspects of running a business. One of the things I hope to carry on at Van Dyk is that dedication to our customers.”
Making the commitment
Florian officially joined Van Dyk as sales specialist last spring, following his brother, Maarten van Dijk, who has been operations manager since 2017. Immediately, Florian was struck by how much the MRF systems have changed from the ones he remembers visiting in years past. “Each one of these projects, whether it’s a new system or a baler installation, is a tremendous undertaking,” he says. “It takes an incredibly talented team to put these things together.”
Committed to learning all aspects of the business, Florian has clocked hours so far in accounting, logistics, sales and shipping, and currently is assisting in service and installation crews.
“When I joined the company, I thought I knew a fair bit about it. As I’ve moved through the various departments, I’ve realized how much I have to learn,” Florian says. “But studying all aspects of the business has been invaluable. Every role here is critical to the success of the company and to serving our customers.
“I’m looking forward to what’s next,” he says. “Van Dyk has a really strong future ahead. ”

Van Dyk organic solutions
As more states pass legislation mandating organics diversion from landfill, more waste processors are in need of solutions for separating this material. Van Dyk is in partnership with Smicon, a manufacturer of depackaging machines.
SMICON
A powerful food-waste solutionSmicon systems are used to recycle food waste from commercial businesses, such as supermarkets, restaurants, caterers and food industry surplus. They turn organic food waste into a slurry that can be used for animal feed, compost or to produce methane gas for renewable energy.
For waste that is still in its packaging, the machines liberate the organics without pulverizing the containers. The depackager decouples the packaging while screening the organics to create a pumpable organic stream.
The packaging emerges as a relatively clean, dry material that can be sold to recycling or fuel markets. The systems are adept at handling robust material, such as canned goods, as well as delicate material, such as flexible packaged goods.
Commercial-scale processing is being done with Smicon systems in the U.S. as well as internationally. Learn how to conquer organics processing with this efficient, effective and proven solution.
The HAAS line of shredders
Powerful tools for processing wood waste, commercial waste and C&D material
With stationary and mobile platforms, the HAAS line of shredders processes the toughest material.
HAAS has an intelligent two-shaft shredding system that sets it apart from other industrial waste shredders. Two independently driven shafts can move in either direction simultaneously to keep the infeed material constantly in motion.
Material is shredded in forward and reverse rotation, ensuring maximum throughput at all times while also preventing jams. When processing heavy C&D debris or industrial waste, the shafts automatically reverse themselves to properly handle the material.
Shred, break or chip even the toughest material with HAAS. Like all the machinery offered by Van Dyk, these machines are meant for pure production and designed for minimum downtime and wear.
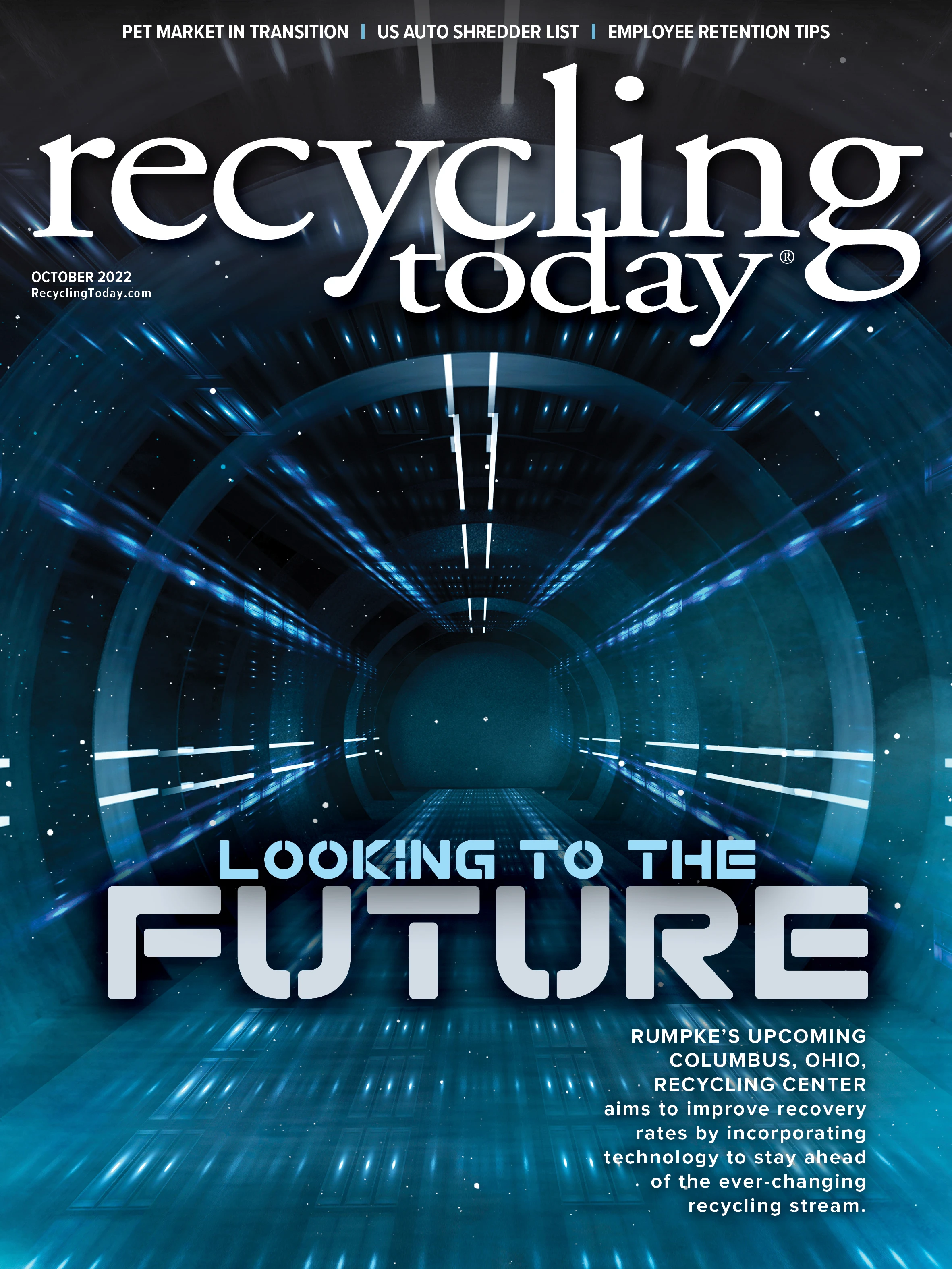
Explore the October 2022 Issue
Check out more from this issue and find your next story to read.
Latest from Recycling Today
- New recycling grant program launches in Massachusetts
- Tire Recycling Foundation names executive director
- Dock 7 named 2025 Exporter of the Year at New Jersey International Trade Awards
- Waste Connections reports ‘better than expected’ Q1 results
- Commentary: How EPR is transforming the packaging industry
- Acerinox names new North American Stainless CEO
- Greenwave closes 2024 books with red ink
- Steel Dynamics nets $217M on record shipments