New Robot in Town
With a focus on meeting the client’s needs with the best possible plant or retrofit solution, Van Dyk Recycling Solutions has the most flexible offerings in intelligent and robotics sorting.

Van Dyk’s long-time manufacturing partner, Bollegraaf, has been working on its own robotic solution since 2005, and now offers the RoBB-AQC with a camera and NIR (near-infrared) materials identification system. But the customer also has the choice to outfit the RoBB-AQC with world-renowned Tomra Autosort recognition. The Tomra recognition offers a combination of sensors, including NIR, camera, AI (artificial intelligence) recognition, laser object detection and high-resolution metals sensors.
Through long-standing relationships with manufacturers of the best technology the recycling world has to offer, Van Dyk is able to find a solution that fits your needs and goals. In today’s world the integration of intelligent sorting solutions is becoming more and more necessary for MRFs to remain competitive. Equally necessary is for MRFs to evaluate the efficiency of their entire system before deciding on which type of new technology to invest in.
Expert Integration
Van Dyk visits MRF operations all over the U.S. and Canada to see first-hand the challenges these sites face. Highly contaminated inbound material streams; stream changes due to factors such as light-weighting, the Amazon effect, reduction of ONP, increase of film and trash; high maintenance costs; and increasing end product quality demands are just a few of them.

There also are challenges with respect to maintaining a safe working environment and manual sorting labor issues - like finding willing candidates to show up daily and dedicate themselves to working the sort line. These struggles make the allure of AI all the more appealing.
Whatever technology is being considered, it is critical to first examine all points in the sort line that could use improvement. A simple adjustment to a sizing screen, for example, can improve separation and prevent the start of a domino effect that ripples down the line and makes sorting conditions too challenging for any intelligent sorting device. The most critical factor to an optical sorter’s or robot’s success is that the infeed belt provides it an even, single layer of material—not deep piles. The more spread the material can be, the more accurate and successful the technology will be in recognizing, picking and sorting.
Running a recycling operation is a challenge with many factors. Van Dyk works with clients to integrate robots or other intelligent sorting solutions, while also ensuring the entire system design and process will deliver the desired results. When it comes to using the latest robotic or optical sorting technology, recycling facility operators should keep in mind that it is really all about the way the system is fed.
Put simply: intelligent sorting technology is only as good as the quality of its material feed.

New MRF Creates Opportunity
Mazza Recycling has roots dating back to 1964, when James and Dominick Mazza’s grandfather started a demolition and scrap company. Since those early years, the Mazza family has developed a range of businesses.
The current 55-acre facility in Tinton Falls, New Jersey, from which the firm operates, was purchased in the early 1980s. “My father and uncle operated here, primarily focused on the C&D transfer station, their demolition business, and also leasing a portion to a mulch producer,” James Mazza shares.
“In 2016, my cousin Dominick and I bought the business from our fathers. Defining the future trajectory of the business then became our responsibility,” he continues.
James and Dominick Mazza were no strangers to the recycling industry. James began working with his father when he was 10 years old. “He’d have me work on whatever needed to be done. I’ve torn down buildings, operated machines, cut scrap, and sorted cardboard,” he says.

When James and Dominick took over the business, they began expanding nearly immediately. They added roll-off service, then front-loader service for commercial accounts. Immediately, they saw the benefit of added recycling services.
“We purchased an old baler and began direct baling cardboard. We added a very simple commercial sort line, and we were off,” James Mazza says. Volumes continued to grow as the company saw tremendous opportunity in Central New Jersey.
“Three years ago, we began planning to build a recycling plant. Initially, we were thinking of a commercial plant. The more we researched and looked into it, however, the more convinced we became that building a single-stream plant would allow us to maximize recovery and best serve our local community,” James Mazza says.
The company began the process by touring numerous recycling plants supplied by a range of companies. “The first thing I looked at was the trash line,” James Mazza says. “If there were a lot of recyclables left on that, sometimes I just left. As I went around, one thing became clear to me, the plants supplied by Van Dyk had less residue, and they were doing a better job capturing more recyclables and producing cleaner commodities.”
Because Mazza Recycling was coming to the single-stream recycling business with no real experience, there was a lot to learn. “I understood recycling and the commodities markets, but I did not know single-stream,” James Mazza says. “The Van Dyk team helped a lot; they were very knowledgeable. Pete Bond was a great resource. He really worked with us to help build our knowledge.”
He continues, “The Van Dyk plants were simply better built, and clearly had a lot more understanding of what it takes to achieve and maintain production in the long term. That stood out to us. We’d upgraded our baling capacity a year ago to a Bollegraaf 120S, so we had some experience with the quality of their equipment.”
The new 26-ton-per-hour recycling plant opened in September 2020.
The Mazza Recycling plant features Lubo non-wrapping screens, a Lubo elliptical separator, Tomra optical sorters and numerous other components all integrated by Van Dyk Recycling Solutions.
“We’re thrilled with the plant,” James Mazza says. “It will allow us to offer our surrounding communities a far more economical recycling solution; we’re very excited about that opportunity. Recycling is the future, and we’re thrilled to be part of it here in New Jersey.”

VAN DYK Vision-AR™
Tired of costly service visits? Don’t want outside visitors in your plant? VAN DYK Vision-AR™ brings the most experienced service technicians directly to your plant at a moment’s notice.
The system uses augmented-reality to simulate an in-person service visit or training session. Your mechanic wears the headset and uses it to call the Van Dyk service line. Via the headset camera, our service desk streams your field of vision in real time. Our technician sees what you see and walks you through each step required to solve your issue. Augmented reality allows us to superimpose icons onto your field of vision (circles, arrows, text boxes) to give you clear directions and be absolutely certain we get the fix right the first time.
We can also upload images and videos to your tablet screen so you can reference them whenever you want. Saving equipment schematics or preventive maintenance videos can help you store troubleshooting tips and best practices for the future.
Advantages of Van Dyk Vision-AR™
- Receive immediate solutions with clear communication
- Eliminate service visits and associated costs
- Priority phone service (skip the line)
- Increased safety (our technicians can monitor and advise on safe practices while looking in on your plant)
- Noise-canceling headphones (communicate clearly by blocking out plant noise)
- 100% hands-free design lets you follow directives without halting communication
- Problems that happen intermittently can be immediately solved

SMICON – The ideal solution for source-separated organics!
SMICON depackaging machines flawlessly separate metallic and plastic food packaging from the organic material. Inputs can be grocery store or commercial food waste. The depackager decouples the packaging while screening the organics to create a pumpable organic stream. The packaging emerges as a relatively clean, dry material that can be sold to recycling or fuel markets. The organics are ideal inputs for composting or digester operations.

BeeFoam – Dust-free for up to 12 days!
The BeeFoam dust suppression system works wonders to reduce the massive dust created in glass beneficiation or C&D sites. Positioned on the infeed conveyor to the system, the BeeFoam dust suppression system uses a minimal amount of water mixed with a special liquid to create a foam that binds to dust and weighs it down for up to 12 days. This results in increased air quality in the plant while also increasing sorting efficiency and decreasing the cleaning frequency on optical units.

10 Reasons to Buy a Bollegraaf Baler
“With the HBC140 we can run the same tonnage as a facility twice our size. Right off the bat, it added 25 percent to our capacity with no signs of slowing down. The technological advancements on it are just tremendous.” Scott Jenkins, President, EFI Recycling
“Our HBC120S truly is automatic and an integral part of our high throughput and productivity. If you are serious about throughput and quality, get a Bollegraaf.” Mike Ferro, General Manager City Carting/WTI MRF
“There are many things that set Bollegraaf balers apart from the competition, but in my opinion, it is the organization as a whole. From sales to service and parts, to ownership, Van Dyk stands behind their equipment and provides a level of support that is hard to find in the marketplace.” Kevin Duncombe, President, Western Pacific Pulp & Paper

“We soon realized we purchased much more than a piece of equipment designed to bale material. The Bollegraaf has brought a confidence with it that radiates through the facility.” Rich Biondi, General Manager, YES Recycling Inc.
“The first time I saw a Bollegraaf operate, I was amazed by how fast the baling cycle was. In the 20-plus years that we have been running Bollegraaf balers, we have found them to be consistently dependable. I recently purchased my sixth one.” Rod Nicolls, Vice President of Operations, Urban Impact
“The pre-press flap allowed us to bale without shearing, so maintenance costs improved and downtime was significantly reduced.” Joe DiNardi, President, Colgate Paper Stock
“It produces dense, symmetrical bales that are perfect for export.” Michael “Recycle” Benedetto, President, TFC Recycling
“The 120S model packs a lot better than our previous baler with a lot less downtime.” Dale Schmidt, Recycle Manager, Loraas Recycle
“The engineering, construction and performance on the Bollegraaf is top of the line—the Cadillac of balers.” Frank Sánchez, Vice President, Town Recycling LLC
“We have an HBC120 for containers and an HBC140 for fiber. Both exceed our expectations of throughput and uptime for our 50tph system.” Brian Dubis, MRF Operations Manager, RIRRC
Get curated news on YOUR industry.
Enter your email to receive our newsletters.
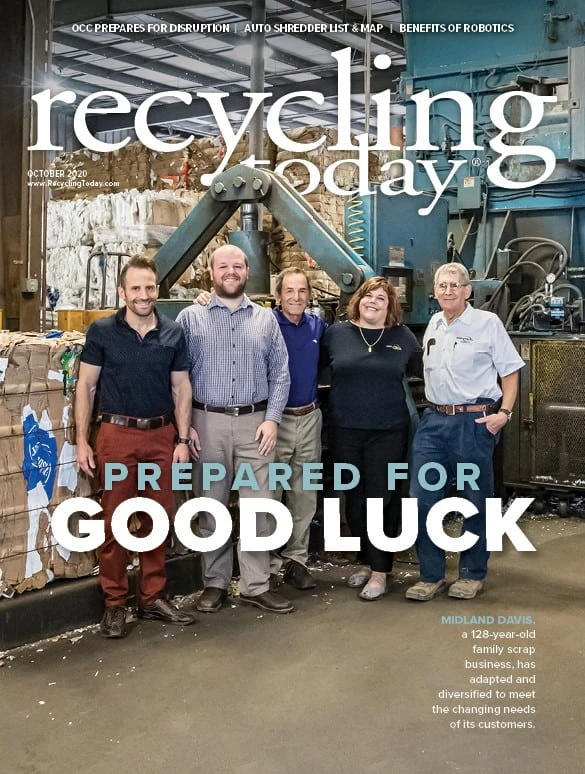
Explore the October 2020 Issue
Check out more from this issue and find your next story to read.
Latest from Recycling Today
- Fenix Parts acquires Assured Auto Parts
- PTR appoints new VP of independent hauler sales
- Updated: Grede to close Alabama foundry
- Leadpoint VP of recycling retires
- Study looks at potential impact of chemical recycling on global plastic pollution
- Foreign Pollution Fee Act addresses unfair trade practices of nonmarket economies
- GFL opens new MRF in Edmonton, Alberta
- MTM Critical Metals secures supply agreement with Dynamic Lifecycle Innovations