
Making a MRF safe
High-level automation delivers superior safety and improved recovery and purity of recyclables.
In March, Waste Connections started up a new material recovery facility (MRF) in Plainfield, Illinois, replacing a previous plant that had suffered a devastating fire. The new plant was built by Van Dyk Recycling Solutions and features equipment from Bollegraaf and Lubo with Pellenc optical sorters.
“We rebuilt the entire facility from the ground up,” says Tim Horkay, director of Recycling Operations for Waste Connections. “We were replacing a facility that had an 18 ton-per-hour (TPH) capacity and, in constructing the new building, we had to stay within that same footprint, which constrained us a bit. The new facility is handily processing 37 TPH.”
Process automation is key
“From the outset, our mission was to build the safest MRF in America,” says Dan Kurtz, executive director, recycling, at Waste Connections. “Part of that meant limiting the number of workers in the plant. The more we could automate, the more we could avoid putting our team members in harm’s way.”
The plant has four manual sorters and consistently processes 37 TPH. That’s made possible by a tremendous level of automation, including a revolutionary front-end design that eliminates manual presorting.
Material flows into the system through a traditional metering bin before passing over a Günther SPLITTER spiral shaft screen, which produces two fractions, a plus-5-inch fraction and a minus-5-inch fraction. The overs fraction is inspected by two sorters to remove noncompliant items. That fraction then passes over a LUBO 880 OCC (old corrugated containers) screen, after which are the second two sorters who remove any remaining noncompliant items.
After material passes through the plant’s front end, it is staged in mid-plant bunkers that meter material to the container line, which features five of the plant’s 11 Pellenc optical sorters. “We elected to use the Pellenc opticals because their performance is fantastic,” Horkay says. “They are extremely precise and reliable in their sorting efficiency. Equally important, however, is the fact that they have a superior design for access to clean and service the units.”
“For opticals to perform well on an ongoing basis, it’s essential that they are serviced,” Kurtz says. “Having an access design that allows our team members to safely and easily get in to clean them and perform any necessary ongoing maintenance played an important role in our selection process. Again, an overarching mission was building the country’s safest MRF.”
Collaborative design
“The Van Dyk team was great to work with. They listened closely to our needs and were extremely collaborative in designing the plant,” Horkay says. “Because we had to remain within the footprint of the preexisting building when we constructed the new building, we did not have all the room you might have in a pure greenfield build. We were building a plant with roughly twice the capacity. It meant we had to be very creative in how we did things.”
He adds, “This plant was also designed with four layers of fire protection. We have the traditional sprinkler system with oversized sprinkler heads, Fire Rover detection and cannons, in-vessel fire suppression in areas like bunkers that are hard to see, and we added 1.5-inch water mains every 50 feet with fire department-rated hoses on reels. It’s all designed to prevent any fire from spreading, but if one does, we’re prepared to extinguish it as soon as possible.”

Greyparrot: Enhancing operations and recovery
A new era in materials identification and plant optimization arrives.
In February, Bollegraaf Recycling Solutions invested in Greyparrot, a London-based company recently named to the Global Cleantech 100 list.
Through its close affiliation with Bollegraaf, Van Dyk Recycling Solutions offers Greyparrot’s technology platforms to its customers. The system offers a wide range of benefits that include materials characterization, proactive plant management and connected operations.
“We’re thrilled to be offering this innovative technology to our customers,” says Pieter Eenkema van Dijk, president of Van Dyk Recycling Solutions. “It offers plant operators a level of visibility into the operational efficiency of their plants as well as recovery rates and material purity that has never been available.”
A platform like no other
The Greyparrot analyzer uses artificial intelligence to capture materials identification in real time. Through a range of customizable reporting, it then allows MRF operators to turn that data into actionable intelligence.
Implementing Greyparrot yields numerous benefits:
Spot trends and issues as they arise. Through customizable alarms and reporting, plant operators and owners instantly know if recovery drops for a specific material or throughput fluctuates, allowing immediate action.
Deliver higher quality recyclables with the data to prove it. Through real-time analytics, MRF operators can ensure ongoing material quality and provide specific reporting of exact levels for nonconforming materials.
Automate materials sampling and reporting. Provide quality and/or contamination feedback to communities or other stakeholders for the materials entering your facility.
Monitor equipment performance over hours, days, weeks or months. Through real-time ongoing monitoring, operators can identify fluctuations in machine performance immediately across the plant environment, allowing proactive maintenance or machinery adjustments.
Reduce valuable material in residue. Because specific residue levels and characterization can be measured continuously and in real time, you avoid the risk of valuable commodities slipping into your residual stream.
Learn more about Greyparrot by visiting with your Van Dyk representative. Don’t be left behind. Greyparrot provides a proven pathway to the MRF of the future.
Processing for the PROs
Ontario’s contracted processors have selected Van Dyk Recycling Solutions for their recycling systems.
The Made-in-Ontario Plan shifts waste diversion to a producer responsibility model. Product and packaging producers must contract with a producer responsibility organization (PRO) to facilitate recycling or establish their own programs.
The PRO Circular Materials awarded processing contracts to two companies: GFL and WM, which are building new plants designed and built by Van Dyk Recycling Solutions.
These plants must recover an incredibly wide range of packaging.
“All the plants will make extensive use of optical sorting to ensure they are effective with the initial material stream and adaptable enough to adjust to how packaging will change as the program matures,” says Van Dyk Process Engineer Ryan Cournoyer.
Nova Circular Solutions
Nova Chemicals selects Van Dyk for its mechanical recycling plant.

Nova Chemicals, headquartered in Calgary, Alberta, is a top-five producer of petrochemicals in North America and strives to be the leading sustainable polyethylene producer. The company, through Nova Chemicals Circular Solutions, is building a 450,000-square-foot mechanical recycling plant in Connersville, Indiana, and has selected Van Dyk Recycling Solutions to construct the front-end processing system.
“The facility will process plastic films and produce recycled polyethylene in pellet form,” says Alan Schrob, director of mechanical recycling for Nova Chemicals. “There is high demand from retailers and brand owners to use our recycled polyethylene pellets. RLLDPE [recycled linear low-density polyethylene] is one of the most commonly used materials for flexible food packaging and can be used for the full scope of applications, including pantry staples, refrigerator items and freezer packaging.”
The completed plant is forecast to produce more than 100 million pounds of rLLDPE by 2026. The preparation system Van Dyk supplied consists of four lines, the first of which is to be operational in January 2025.
Each line will perform dry front-end processing that includes bale breaking, dewiring, initial size reduction, magnetic and optical sorting to remove contamination and color sort material to prepare it for further downstream repolymerization.
The plant’s four lines are independent of one another to add flexibility and efficiency in the materials preparation stage. This also allows material from different suppliers to be independently processed for quality assurance purposes.
“We selected Van Dyk because they are one of the premier recycling facility OEMs. The equipment we are using from Van Dyk is state-of-the-art to ensure we can produce the highest-performing recycled polyethylene for the most demanding applications,” Schrob says.

Freepoint Eco-Systems
Van Dyk supplies the front-end system for an advanced recycling plant.
As a global provider of commodities trading, financing and physical management services, Freepoint Commodities LLC is involved in products ranging from energy to agriculture and plastics to metals. Its affiliate, Freepoint Eco-Systems LLC, was established in 2020 with a mission to address the global plastic waste problem.
Part of its investment to build a circular economy involves constructing an advanced plastics recycling facility in Hebron, Ohio. The plant is being built to recycle some 90,000 tons of polyolefins annually, developing a renewable pathway in support of a circular material stream.
To operate effectively, the advanced recycling plant requires feedstock that is totally free of contamination. Van Dyk Recycling Solutions was commissioned to supply that plant.
Inbound materials include MRF film, bulky rigids, purge patties, MRF residue and other highly contaminated polyolefins. To meet the rigorous quality requirements, Van Dyk designed a multistage purification plant.
Included in the process is bale breaking and dewiring, size reduction, metals removal, fines removal, advanced optical sorting to remove remaining contamination, which includes other plastics that might be in the stream. Finally, the system ushers the material through a densification process to provide a highly densified, consistent feedstock for the advanced recycling plant.
“These lines have to provide the cleanest possible material,” says Adam Lovewell, process engineer at Van Dyk Recycling Solutions. “Because Freepoint is refining these recovered materials back into a pyrolysis oil product, there is no room for error or contamination.”
“Bringing online Freepoint’s flagship facility in Ohio later this year marks the next big step in expanding our advanced recycling footprint in the United States and across the globe,” says Jeff McMahon, managing director of Freepoint.
“From construction to the launch of operations and beyond, the facility will have a positive impact both broadly and in the Ohio community through plastic recycling, job creation and greenhouse gas reductions. Ultimately, we are working to contribute to a more sustainable circular economy.”
All recycled plastic feedstock produced by the Freepoint facility will be sold to Shell in connection with the companies’ long-term supply agreement.
Günther screening

The Günther SPLITTER is the original spiral shaft screen, patented in 2004, and offered exclusively in North America by Van Dyk. It is a star performer in processing material that wraps easily. Items that are notorious for wrapping around screen shafts will not wrap on the SPLITTER at all.
Say goodbye to your presort station. Available in three designs, these screens are the foundation of a fully automated front-end system at single-stream recycling facilities. They are also ideal for processing MSW, C&D, organics and yard waste, soil cleanup and especially for C&I.
These powerful, self-cleaning and wear-resistant spiral shaft screens effortlessly master the most difficult tasks that push other separation technologies to their limits.
Centriair

When odor reduction is needed, nothing performs like Centriair.
Proven technology that can deliver up to 99% odor reduction. Its small footprint allows unintrusive installation in a facility. You’ll be able to reduce environmental and health impacts for your workers and neighbors and save energy and space, with high performance results assured.
Van Dyk Recycling Solutions is the exclusive North American supplier for this proven technology. For guaranteed results for odor or VOC reduction, look to Centriair.
SSO Processing with Smicon
Boost organics recovery by 75% with Smicon organic depacker.

To comply with state mandates for organic recovery and landfill diversion, one source-separated organics (SSO) processor recently installed a Smimo 120 organic depacker to turn food waste into organic feedstock and a Smimo 15 grinder to grind the slurry into a finer fraction. The finer fraction makes the feedstock saleable to a wider pool of buyers, which includes composting, sewage treatment and anaerobic digestion plants. The Smicon system has increased throughput and organics recovery.
The facility processes 80 tons per day of residential and commercial SSO. Previously, the site recovered 15% of the organics from incoming SSO—its current organic recovery has reached 90%. A walking floor, large feeding bunker and overall high capacity of the equipment greatly reduce unloading times. The previous system took 45 minutes for a truck to unload, whereas the new system takes under five minutes.
Get curated news on YOUR industry.
Enter your email to receive our newsletters.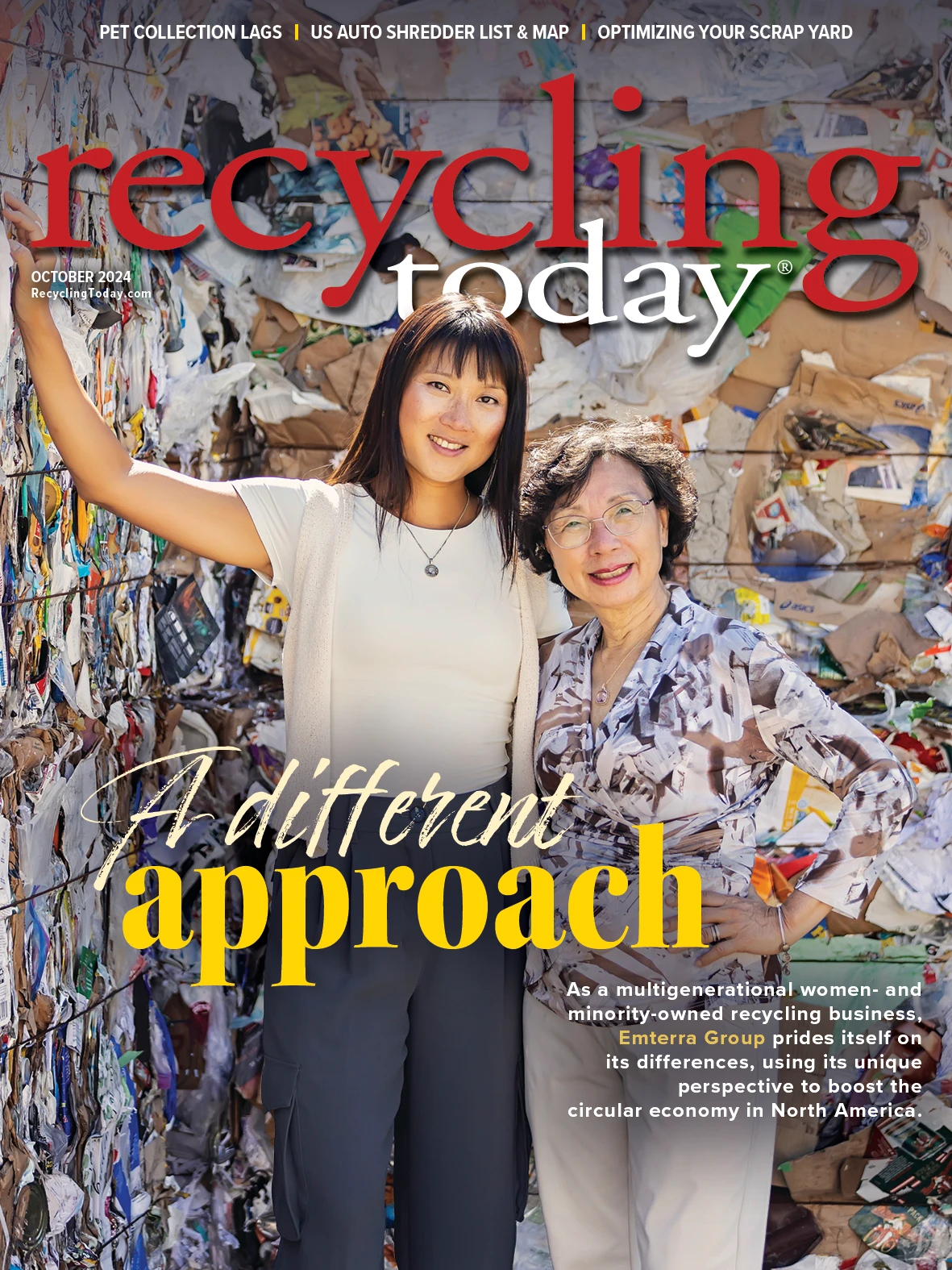
Explore the October 2024 Issue
Check out more from this issue and find your next story to read.