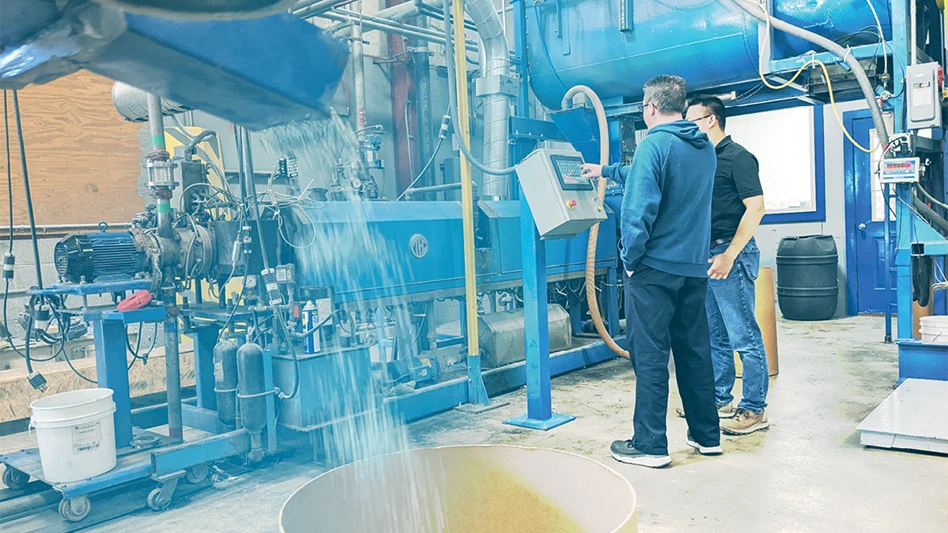
Photo courtesy of Ultra-Poly Corp.

Ultra-Poly Corp. was founded by Alan LaFiura in 1974 to provide toll processing of low-density polyethylene (LDPE) film scrap and has evolved over the last five decades into a custom compounder of recycled resins with 320 million pounds of production capacity and 220 employees. Innovation has played a significant role in its evolution, with the company continually seeking to expand its manufacturing capacity and capabilities.
Portland, Pennsylvania-based Ultra-Poly operates five plants, including two at its headquarters that house 10 extrusion lines, a twin-screw compounding line, postconsumer film and rigid plastics cleaning capacity, 22 silos and a research and development (R&D) center.
A plant originally located in Berwick, Pennsylvania, was the basis for constructing Building No. 2 in Portland. That facility was purpose-built to reclaim film used in the oil and gas industry and processes 200-square-foot pads made of medium- to high-density PE film with a minimum thickness of 40 mils that are used to line containment areas around natural gas wellheads. Agricultural film, lumber wrap and injection-molded parts and other films used in the oil and gas industry are examples of additional material streams the new plant can process. To clean the film, Ultra-Poly developed a dry process.
The company also operates two embedded toll processing plants in Bloomsburg, Pennsylvania: one with a Tier 1 automotive supplier that includes two extrusion lines, and one with a polyvinyl chloride (PVC) sheet manufacturer that includes size-reduction, pulverizing and postblending capabilities. Both sites have 35 million pounds of annual capacity.
In Scranton, Pennsylvania, Ultra-Poly operates a third embedded tolling plant inside a major building products manufacturer that features size-reduction, pulverizing and postblending equipment and two silos, processing up to 35 million pounds annually.
These embedded toll-processing operations illustrate how the company works closely with its industrial and commercial customers to help them reduce costs and increase efficiency by developing customized programs.
Embedded approach
Toll processing represents roughly 40 percent of Ultra-Poly’s volume, company President David LaFiura says. The company provides tolling services through embedded operations that involve installing and operating recycling assets in the scrap generators’ facilities as well as in its own plants.
“We like tolling in general because it eliminates inventory risk” associated with owning the material, he says. “We’re providing a service of converting scrap into pellets without the risk that’s associated with a [potentially] falling market.”
Vice President of Sustainability and R&D Kevin Cronin says toll processing “is strategically important because having a mix of both merchant production—compound production—as well as the tolling tends to even things out … which eliminates that inventory risk, but it also allows us to optimize capacity utilization. It allows us to swing that [capacity] depending on what’s going on in the marketplace.”
Cronin adds that Ultra-Poly began by providing toll processing and plans to maintain that service as a portion of its business because of the associated strategic advantages.
“But it is constrained by geography since transportation costs make up a relatively large portion of the overall cost,” LaFiura says. “That same transportation cost becomes a key factor in establishing our embedded tolling operations. When scrap volume is significant, the savings in transportation costs justifies the establishment of embedded tolling operations, providing economic benefit both for us and for our customer.”
Cronin mentions the company’s tolling customers recently have been asking for Ultra-Poly to compound rather than just reprocess their material to further enhance it.
“That would usually entail us taking their scrap and then adding something to it when we process it, whether that’s an additive or additional pounds of complementary material,” LaFiura explains.“What that really signifies is it’s a hybrid of the capabilities that we offer,” Cronin adds.
Processing enhancements
Recently, Ultra-Poly installed its first twin-screw extruder, expanding its capabilities in the compounding area.
Twin-screw extruders can be more efficient than single-screw extruders in providing homogeneous mixing of ingredients that include additives, fillers and liquids.
“We have a 110-millimeter Leistritz twin-screw compounding line,” Cronin says. “That is an installation that was put in specifically to enhance our capability for creating more of what I call ‘technically competent’ compounds based on recycled materials.”
The line was installed in 2019 in the main Portland plant and production began in 2020.
“There’s a lot of major differences between single-screw extrusion and twin-screw extrusion, and we had never done any twin-screw extrusion before,” LaFiura says.
Ultra-Poly had to learn not only the proper operation of the machine but also how to handle the pounds going through it, logistically, which involved the addition of silos.
“The volume on the line is large enough that you have to bulk-handle the materials; you can’t be dealing with packaging at all, either on the feedstock or the finished content side,” he adds. “So, we’re running out of silos and running into silos with the twin-screw.”

“I would say it has significantly sharpened our tools in the shed, if you will, for process automation,” Cronin says of the addition of the twin screw, noting Ultra-Poly has developed some of its own process control algorithms and systems to optimize machine operation. “That’s actually translated across the board into our other machinery as well. We’re more highly process-automated by a factor of two than we used to be.”
That automation includes using gravimetric feeding. “It’s the first time in our history that we’ve fed any material gravimetrically as opposed to volumetrically, measuring weights going into the line rather than volume, which is more sophisticated,” LaFiura says.
Cronin says this move has enabled Ultra-Poly to be more precise, doing color-matching to a Delta E (a measurement of how much a displayed color can differ from its input color) of two or less, for example.
While Ultra-Poly has a history of designing its own processing equipment, that was not the case with its twin-screw extruder from Somerville, New Jersey-based Leistritz Advanced Technologies Corp.
Because the company didn’t have previous experience with twin-screw extruders, it decided to go with one of the major manufacturers, Cronin says. “However, as we build out our plant No. 2 in Portland, nearly everything in that plant is being designed, built and installed by us, including the extruders,” he adds. “We do tend to still buy shredders and grinders … but we buy them as a base model and then we modify.”
The company also is adding a wet washing line at the new plant that LaFiura says will be used when necessary, adding, “Our intention is to use it as essentially a polishing step.”
He says the addition of the washing line will allow Ultra-Poly to address the growing momentum for postconsumer recycled content around the country, including new legislation in New Jersey that mandates recycled content in rigid plastic containers and plastic carryout and trash bags.
Ultra-Poly also has a letter of nonobjection from the U.S. Food and Drug Administration (FDA) that allows its recycled polypropylene (PP) to be used in food-contact applications, and its lab capabilities have expanded to include wet chemistry for FDA analysis, Cronin says.
“Right now, it’s seeing a lot of play in cosmetic applications,” he says of the material.
“One of the challenges is that it’s a relatively limited stream of material, and it’s in conjunction with a major retailer in the United States. They do a point-of-sale takeback of some of the products that they have in their operations.”
Cronin says the material totals roughly 1.2 million pounds per year, “which is a nice toe in the water, but it’s not a lot of volume for a lot of applications,” and adds that Ultra-Poly is working on additional submissions to the FDA for its recycled PE and PP materials.
The company is targeting new material streams, as well.
Bumper crop
Ultra-Poly has begun working with auto repair shops to collect bumpers for recycling.
Cronin says the driving force behind the move was a project the company worked on with the Washington-based Plastics Industry Association. “We saw an opportunity because they’re basically highly engineered TPO [thermoplastic olefin] compounds that are going into these bumper fascia, and that’s in our wheelhouse,” he says.
“We went out pretty aggressively and commercialized the collection, reprocessing and then, ultimately, getting this stuff back into good productive use,” Cronin adds, noting that Ultra-Poly uses the material as a compounding agent and as a stand-alone compound.
“We have successfully commercialized the recycled material from automotive bumpers that we are reprocessing, and it is going back onto an automobile,” he says. “We have gone fully circular with the material, not back into a bumper fascia, but back into an automobile in a nonappearance part.”
The company is using an innovative process to collect the bumpers from 150 automotive repair shops as of mid-April. “We are limited by radius right now, but we are working hard to overcome that,” Cronin says.
“The more weight we can get on a single haul, the further the radius will become,” LaFiura adds.

“In addition to being really good at recycling plastics, we’re also really good at reverse logistics,” Cronin says. “That’s what we’re leveraging here, and it’s something that is a bit of a challenge, but we welcome it. It’s something that we are pretty good at: being very creative and developing solutions for some of these harder-to-recycle materials.”
The other challenge comes in the form of metal attachments, such as clips and fasteners. Sometimes, wiring harnesses and wire also can be attached, which require separation. Parts made from other plastics also can be in the stream, such as acrylonitrile butadiene styrene grills.
He adds that marketing the recycled material to the automotive industry remains challenging.
“Perception can be a bit of a challenge,” Cronin says, “But we get very good consistent properties on an ongoing basis that reflect a very high percentage of the original properties.
“The key to this is that all the major OEMs [original equipment manufacturers] are using basically some variation on a theme of a TPO or a rubber-modified polypropylene material because sortation by OEM, for instance, is virtually impossible during collection.”
A measured approach
When it comes to expanding the range of materials the company processes, LaFiura says Ultra-Poly does so by spending the least amount of money possible to begin with. “That allows us to vet everything involved,” he explains. “So, that would include the process and technology but also the economics [and] the markets. Once we’ve vetted that, by using the lowest cost approach possible, we are willing and able to invest heavily into it in order to bring it to an efficient commercialization.”
LaFiura says the initial plant in Berwick to process film from the oil and gas industry is one such example.
“We validate volumes, we validate markets, we validate processes all before we invest heavily in a project,” he says. “Then, once we see all the boxes checked, we’ll go ahead. We’re kind of going through that process right now with bumpers.”
Cronin adds that Ultra-Poly’s work on the bumpers likely has progressed more quickly than the geomembrane recycling did because the company’s abilities have improved over time. “The time frame has gotten a little bit compressed because we’re better,” he says of the company’s abilities to assimilate and evaluate.
LaFiura adds, “I would say, throughout all this, there’s two guiding principles that we think about. One is that the goal is speed to market, so you want to be producing material that you can be selling as quickly in the process as you possibly can. The second is you never add resources ahead of need. Following that approach, it lets you iterate it. It allows you to figure things out as you’re growing.”
But, Cronin notes, “It does require you to be very nimble.”
Ultra-Poly’s R&D team plays a critical role in this area.
“In terms of dollar investment, we’ve grown the department and the resources dramatically over the past several years,” LaFiura says. “We’ve increased headcount in the R&D department significantly by a factor of 200 or 300 percent.” Using this strategy, Ultra-Poly remains ready to tackle the challenges other hard-to-recycle plastic streams offer.
Get curated news on YOUR industry.
Enter your email to receive our newsletters.
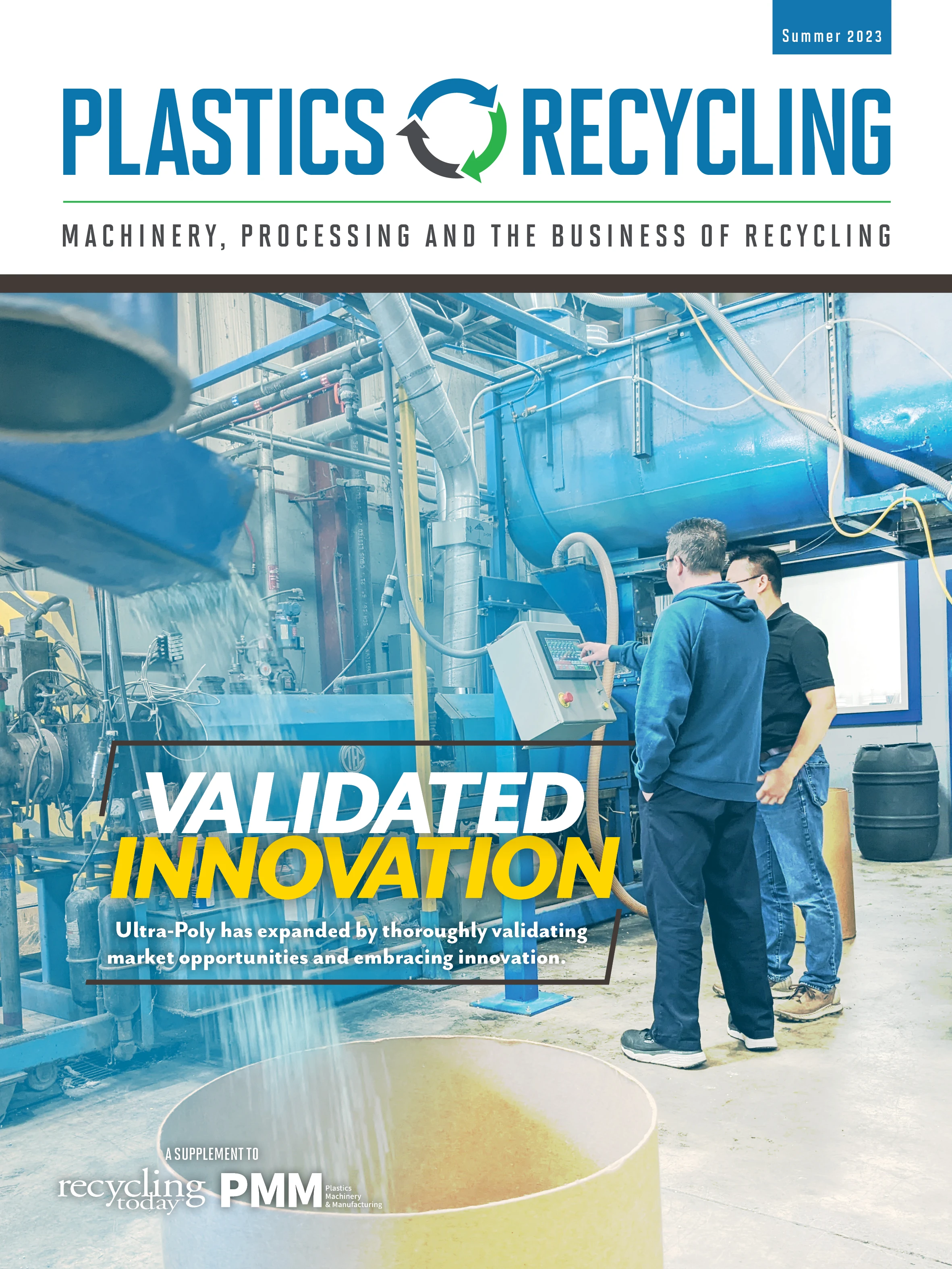
Explore the Summer 2023 Plastics Recycling Issue
Check out more from this issue and find your next story to read.
Latest from Recycling Today
- Nucor expects slimmer profits in early 2025
- CP Group announces new senior vice president
- APR publishes Design Guide in French
- AmSty recorded first sales of PolyRenew Styrene in 2024
- PRE says EU’s plastic recycling industry at a breaking point
- Call2Recycle Canada, Staples Professional expand partnership
- Circular Services breaks ground on north Texas MRF
- Tariff uncertainty results in choppy nonferrous scrap flows