
Since the invention of the wheel, humankind has used its mechanical inclinations to increase productivity. In the current era, this same interest has yielded such sayings as “Work smarter, not harder” and “Time is money.”
Just as the humble wheelbarrow moves a couple of hundred pounds of topsoil in the garden, mechanized steel is used to transport hundreds of tons per hour by way of conveyors in many sectors of the recycling industry. This lends credence to another saying, “You have to have the right tool for the job.”
Identify your goals
With the many different types of conveyors, such as steel belts, roller chain belts, flat idlers, flat sliders, oscillators, etc., which is the right tool for the job and how do you choose?
To ensure customers are choosing the correct conveyor types and system configurations, they need to identify application goals, familiarize themselves with their materials’ characteristics and communicate them to a reputable conveyor company. Only then can a recycling application be positioned for success.

It is important to consider the processing goals as the material is being conveyed. Shredders, shears, balers, bale breakers, furnaces and separation equipment all are examples of key system components that determine the end result. Whether the designed purpose is separating ferrous and nonferrous metals or baling mixed paper or old corrugated containers (OCC), conveyors and conveyor systems need to be designed appropriately so these components optimally contribute to the overall goal of the operation. Feed conveyors of inadequate design that are unable to handle stopping and starting under full burden can fail. Inappropriate conveyor speeds or widths can negatively affect a magnet’s ability to separate ferrous metals, decreasing yields. These are just a few examples of why a customer needs to be aware of how the cooperation of conveyors and these components affect the outcome.
Know your material
Material characteristics largely dictate how conveyors will be used in any application. Material density (measured in pounds per cubic unit, i.e., pounds per cubic foot) and throughput (measured in tons per hour, or TPH) are two critical figures in conveyor determination. These two important variables, along with other factors, enable engineers to determine speeds, widths, horsepowers and many other specifications necessary to effectively convey material.
Conveyor engineers also will look for information concerning the physical nature of the material. The size and shape of the material will influence material flow, affecting maximum incline/decline angles for elevation. Sharp or abrasive material might require heavy-duty belting or abrasion-resistant sides. Large bulky material can affect conveyors considerably, requiring a steel belt design for increased impact deflection. Materials that are fine or stringy might need conveyor features designed for additional containment.
Many more material characteristics can affect conveyor selection, but the point is clear: The composition of each individual material is different, and the customer can benefit greatly by acquiring as much knowledge as possible about the material being processed.
Get expert advice
With so many variables to consider, what does this mean for the customer when it comes to conveyor selection?
The most important thing a customer can do to select “the right tool for the job” is communicate with educated, experienced experts from a reputable conveyor company. Regardless of how much experience or knowledge a customer has or if the application needs one conveyor or 10 conveyors, trained professionals will assist in acquiring the required information to tailor a conveyor system to each individual application.
Customers should seek out companies with thorough engineering and design processes. Companies that highly prioritize the engineering and design phase of production are more likely to produce a solution that not only fits the task but that is the right fit. Initial costs involved with correctly engineered equipment often result in higher performing, longer lasting and more profitable solutions.
Everyone has had an experience where he or she has spent twice as much time, effort and resources on a project that should have only taken 30 minutes if the right tool had been used. In the recycling industry, where throughput is measured in tons and efficiency is measured in bottom-line dollars, identifying application goals, understanding your material and working with conveying experts will help get you the right conveyor for your operation.
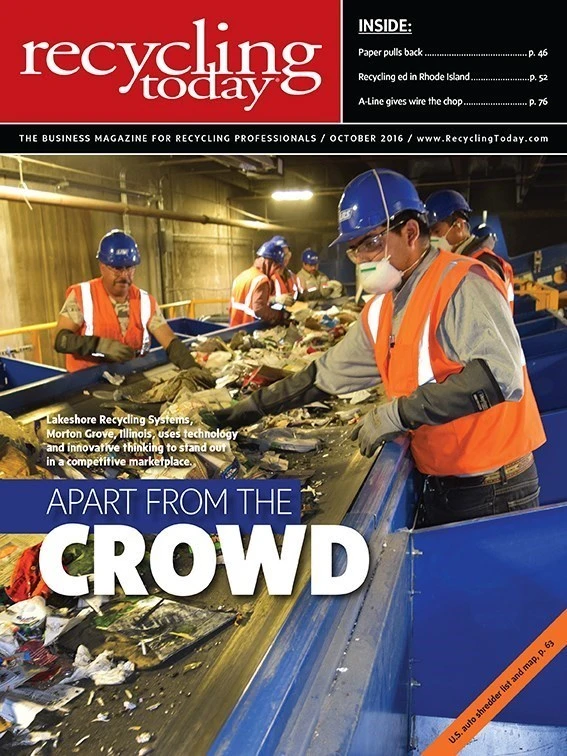
Explore the October 2016 Issue
Check out more from this issue and find your next story to read.
Latest from Recycling Today
- Hitachi forms new executive team for the Americas
- Southwire joins Vinyl Sustainability Council
- Panasonic, Sumitimo cooperate on battery materials recycling in Japan
- Open End Auto Tie Balers in stock, ready to ship
- Reconomy names new chief financial officer
- ICIS says rPET incentives remain weak
- New Jersey officials award $16.2M in annual recycling, waste reduction grants
- Linder Industrial Machinery announces leadership changes