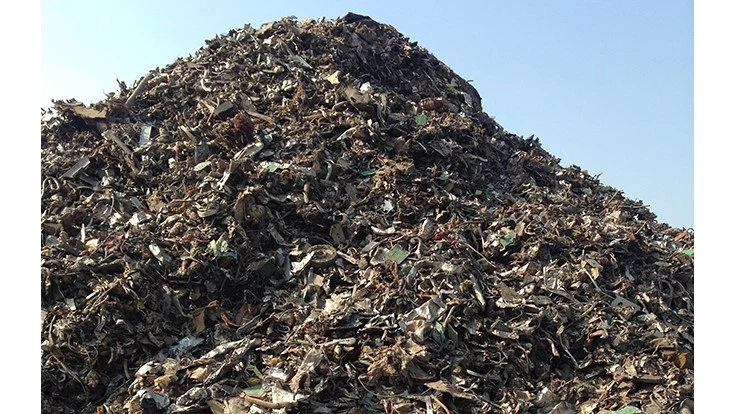
Photo by Recycling Today staff
In a late July earnings report conference call with steel industry analysts, executives from Pittsburgh-based United States Steel Corp. talked about the state of its growing electric arc furnace (EAF) presence and the metallics used to feed its EAF plants. Largely missing from the conversation, however, was scrap.
U.S. Steel President and CEO David Burritt, Senior Vice president and Chief Financial Officer Christie Breves and Senior Vice President and Chief Strategy and Sustainability Officer Rich Fruehauf were among the executives who offered comments and fielded questions during the call.
Burritt said, “The United States remains the leader in sustainable steelmaking as many in our industry have embraced the electrification of the steelmaking process, which is the most sustainable way to make steel.”
He added, “The well-timed Big River Steel acquisition has outperformed expectations. Our new minimill segment now represents nearly 30 percent of our domestic flat-rolled steel EBITDA [earnings before interest, taxes, depreciation and amortization]. It’s lowering our capital and carbon intensity and is expected to deliver more consistent results.”
Ferrous scrap has long been the mainstay raw material in EAF steelmaking in the U.S., with EAF producers such as Nucor Corp., Steel Dynamics Inc. and Commercial Metals Co. not only melting millions of tons of scrap each year but also processing it at sizable yard networks. Even fellow blast furnace\basic oxygen furnace producer Cleveland-Cliffs now owns a network of scrap facilities.
Comments by Burritt and the other two executives, however, focused on pig iron, direct reduced iron (DRI), hot briquetted iron and other virgin materials metallics often used by other EAF producers as scrap additives or alternatives.
“As we expand our low GHG [greenhouse gas] emissions electric arc furnace footprint, raw materials will be a key differentiator,” Burritt said, adding, “While 10 percent of our metallics are in-sourced today, that number could increase to 40 percent by 2024 with addition of pig iron at Gary Works and the proposed Granite City pig iron facility in collaboration with SunCoke.”
Burritt continued, “We’re also expanding our metallic strategy by upgrading our iron ore pellets. We’re investing to upgrade our capabilities at Keetac [in Minnesota] to make direct, reduced-grade pellets. These actions will allow us to become increasingly self-sufficient to feed our minimill segment with key metallics.”
The only mention of scrap came from Fruehauf, who commented, “Having these virgin iron ore metallics in our footprint and able to supply the EAF fleet is a huge advantage for us because then we won’t be as exposed to the ups and downs of the scrap market or cut off of supply or price spikes in pig [iron].”
Regarding pig iron pricing, Breves said a scramble for the material after Russia’s invasion of Ukraine has been a balance sheet factor at U.S. Steel. “We continue to work through more costly inventory and therefore expect meaningfully sequentially lower EBITDA at Big River Steel in the third quarter,” she commented. “In Europe, the conflict in Ukraine and the negative impact on raw material and energy prices are reducing industrial and manufacturing demand. As a result, in the third quarter, our [Europe] segment is experiencing significant margin compression as steel prices have softened while raw material costs remain elevated.”
Going forward, though, Fruehauf said U.S. Steel is “focused on pig first and foremost” while considering DRI “an opportunity for the future. It’s not a question of if, it’s when and where.”
While scrap metal recycling seems not to be receiving foremost attention in the U.S. Steel mix, Burritt nonetheless closed the conference call by commenting, “We look forward to growing with you toward a greener future.”
Latest from Recycling Today
- Partnership to bring local recycling instructions directly to consumers
- ReMA notes the benefits of recycled materials on America Recycles Day
- Tozero raises 11M euros in seed funding to ramp up battery recycling efforts
- Critical Mineral Consistency Act passes House
- Alberta recycling group selects Diversys to digitize its beverage container recovery program
- Recycling Today Media Group hires Mallory Szczepanski
- Berry increases recycled PE use by 36 percent
- Bower, Varta join forces on AI-powered scanning for consumer batteries