
An integrated approach
Urban Polymers operates a 110,000-square-foot plastics recycling plant that produces tens of millions of pounds of recycled plastic flake and pellets annually in the form of polyethylene terephthalate (PET), high-density polyethylene (HDPE) and polypropylene (PP).
The plant’s feedstock comes in part from MRFs operated by Urban Polymers’ parent company, Canada Fibers Ltd., two of which are located on the same 27-acre campus on Arrow Road in Toronto that Urban Polymers calls home, explains Daniel Reshef, manager of steward relations and sustainability for Canada Fibers Ltd. – Urban Resource Group. The campus’ buildings cover a total area of nearly 500,000 square feet.
“We saw a unique opportunity to vertically integrate our operations at one complex,” he says. “Materials sorted at both of the MRFs on-site can be brought next door to our plastics recycling facility, Urban Polymers. This gives customers confidence in complete product traceability, security of supply and consistent quality, not to mention a low carbon footprint from less handling and transportation.”
Canada Fibers did not take the express lane to vertical integration; it was something that evolved over time. The company was established in 1990 as a paper recovery and trading firm, providing its services primarily to commercial and industrial customers. In 1998, Canada Fibers was awarded a contract with the city of Toronto to process curbside-collected paper, marking its foray into postconsumer MRF operations. Additional contracts to process residential recyclables for other area municipalities followed. Today, the company says it processes, markets and ships more than 600,000 metric tons (nearly 661,400 short tons) of recyclables, or more than half of all the blue-box material recycled in Ontario.
In July 2015, Canada Fibers founded Urban Resource Group to produce products, including compounded plastics, garden mulch
Reshef says, “We chose to enter the reprocessing space to complement our sorting services at our Ontario MRFs in a way that secures local end markets for these commodities and makes Urban Resource Group vertically integrated, adding more value for our customers.”
Canada Fibers further integrated its operations in 2017 with the purchase of HGC Management, Brantford, Ontario. In addition to adding seven MRFs in eastern and southwestern Ontario to the company’s portfolio, the purchase provided Canada Fibers with new curbside collection capacity in the form of 75 trucks that collect recyclables and mixed waste from homeowners in Ontario.
Today, Canada Fibers owns or operates 18 recycling facilities, comprising 14 MRFs, its Urban Polymers plastics recycling plant

From bale to pellet
Canada Fibers has cross-docking established between its Arrow Road MRFs and
Once bales arrive at Urban Polymers, the company engages in additional sorting that includes screening, magnets
Urban Polymers operates two grinding and chemical hot washing lines. Reshef says that in peak season, which is summer, Urban Polymers has the flexibility to increase its capacity to process additional incoming PET material.
The flakes produced on these lines can then be extruded into pellets using the company’s twin-screw extruder.
Reshef says this type of extruder offers benefits when processing recycled plastics because of its filtration and venting capabilities, which further help Urban Polymers to produce what he describes as “a homogenous, pure and high-quality product.”
The company’s compounding extruder also allows Urban Polymers to provide
While he declines to share information pertaining to the company’s bale yield, Reshef says, “Because of our vertical integration, we are capable of getting a higher yield because we are making the bales and, at the end of the day, can create a pure stream of material, which benefits our yield on the washing and grinding lines.”
The recycled plastics Urban Polymers produces are sold to packaging producers, film extruders and to manufacturers serving the construction sector. The recycled PET and PP are sold throughout North America, while Reshef says the recycled HDPE the company produces is sold within Canada.
“Local manufacturers have been great partners over the years, and we look forward to growing alongside them in Canada,” he adds.
While Urban Polymers does not have letters of no-objection from the U.S. Food and Drug Administration (FDA) or Health Canada that allow its recycled PET pellets to be used in food-contact applications, Reshef says its PET flake can go into these applications. “Because we chemically hot wash, our PET flake can go on to become a food-grade product,” he says. “Companies we sell flake to make an FDA-approved product out of it.”
Reshef adds that Urban Polymers would like to explore securing no-objection letters for its recycled HDPE pellets, which currently are being sold into industrial applications.
“We are always striving to reach high-grade applications and expand capacity to meet expected demand surges,” he says.

Demand concerns
While legislation mandating recycled content can help to push the needle on demand for recycled plastics, Reshef says Urban Polymers is focused on making quality products that appeal to plastic consumers without the help of such legislation. “We are pleased to see more and more companies committing to use recycled content ahead of legislative requirements.”
However, he acknowledges that concerns about the quality of recycled plastics still can hinder their use.
“In the case of plastic, there are still preconceived notions that PCR (
He continues, “It’s important for business not to think of PCR as a low-cost alternative to prime grade but rather as a value-add to the bottom line for increased corporate sustainability and new marketing opportunities.”
Sustainable solutions
In his role at Canada Fibers – Urban Resource Group, Reshef works to establish strategic relationships with companies that want to increase their corporate sustainability efforts through integrated resource management and PCR use.
“I am also a major advocate for innovation and collaboration in the recycling industry,” he says. “I would love to see more brand owners and manufacturers working alongside recyclers to create circular supply chains that advance the application of postconsumer material and increase waste diversion.”
One such company that Urban Polymers has worked with is Lush, a manufacturer of personal care products and cosmetics using vegetarian ingredients. (See Product Pull-Through for more information on Lush’s use of PCR.)
While Urban Polymers supplies Lush with recycled plastics on an ongoing basis, the companies also are involved in an effort to recycle ocean and beach plastics.
Reshef says the biggest challenge in processing this material can be effectively sorting it because the material includes everything ranging from packaging to buoys and other items that do not include resin codes.
Additionally, the grit from the sand clinging to this material “takes a toll on our washing lines,” he says.
Recycling ocean plastics, therefore,
While Reshef says Urban Polymers has found that interest in recycled plastics is growing, more work remains to be done.
“We would like to see more brand owners demand postconsumer recycled content in their packaging, products and ‘work-in-process’ (WIP) items,” he says. (For details on the Association of Plastic Recyclers program that targets increasing demand for recycled plastics in WIP items, see the sidebar, at left.) “This demand pull is integral in establishing a local circular economy and strengthening the recycling industry.”
For more information: Urban Polymers, 416-253-0400, www.canadafibersltd.com/urban-polymers
Get curated news on YOUR industry.
Enter your email to receive our newsletters.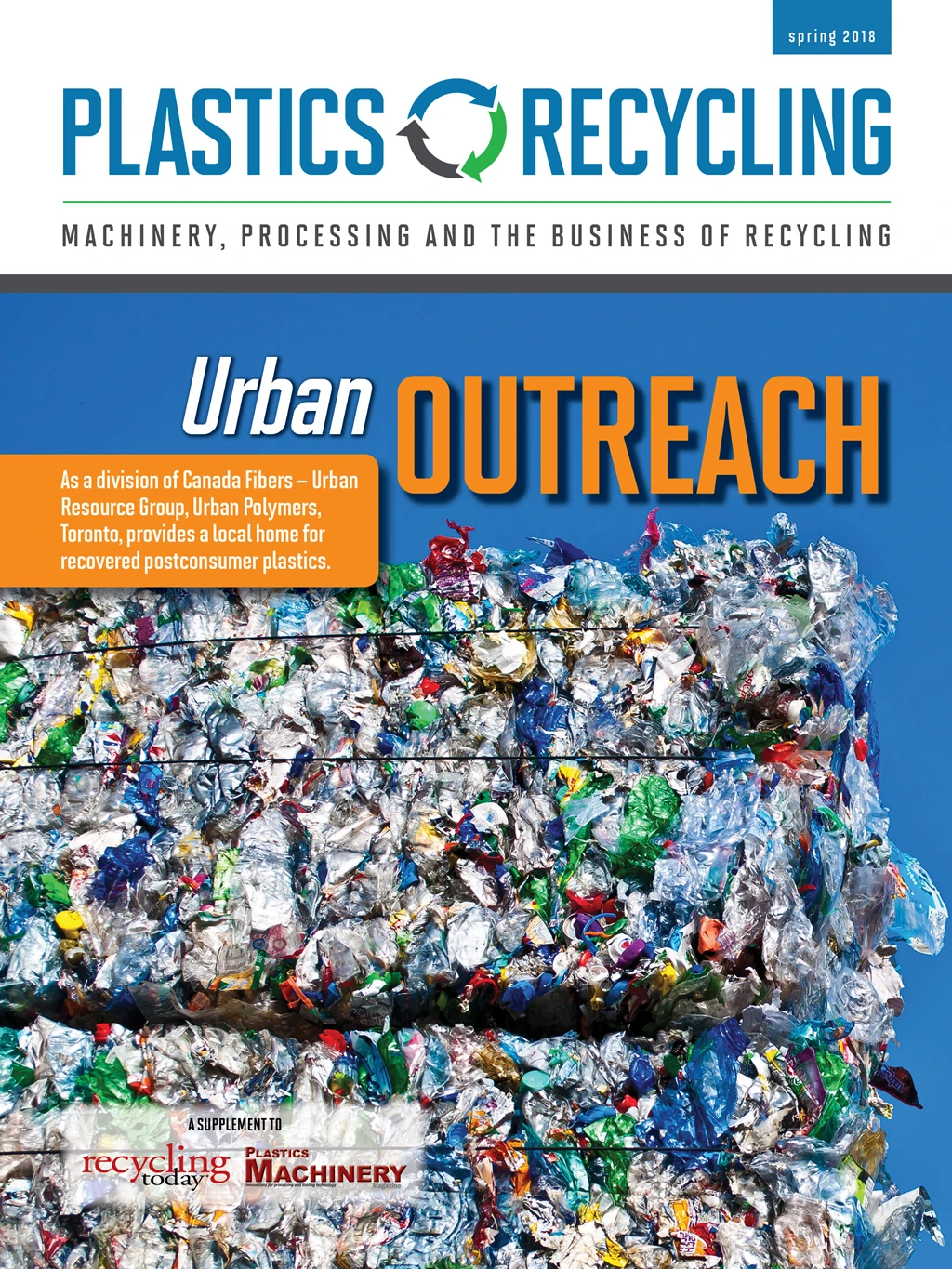
Explore the May 2018 Plastics Recycling Issue
Check out more from this issue and find your next story to read.
Latest from Recycling Today
- Reconomy names new chief financial officer
- ICIS says rPET incentives remain weak
- New Jersey officials award $16.2M in annual recycling, waste reduction grants
- Linder Industrial Machinery announces leadership changes
- First phase of EPR scheme launching in Alberta
- Veolia technology helps PetStar with water conservation
- Athens Services terminates contract with San Marino, California
- Partners develop specialty response vehicles for LIB fires