Steve Silver, president and chief executive officer of FutureMark Paper, is frustrated. The paper mill, located just outside of Chicago, is surrounded by a vast supply of recovered fiber that the company needs to run its machines. While the company’s products are in high demand by forward-thinking publishing houses and environmentally conscious corporations, FutureMark continues to struggle to obtain clean furnish at a fair price from its suppliers.
In addition to quality problems, Silver also decries the huge flow of recovered fiber to offshore sources, primarily China, which leaves domestic paper companies, including FutureMark, at a disadvantage.
The company, which manufactures coated mechanical printing and writing paper with as much as 100 percent recycled content, operates a mill Alsip, Ill., a suburb of Chicago, amid many of the largest printing plants in the country.
THE ROUTE TO RECYCLED CONTENT
The history of FutureMark may not be as long as that of many other paper companies, but it has seen the changing fortunes of the paper industry. The original mill at the Alsip location was built in 1968 to manufacture recycled newsprint. As the newsprint industry started to sour in 2000, the mill was purchased by the Finnish firm Myllykoski. The new owner invested more than $200 million to convert the mill’s production line from newsprint to lightweight coated mechanical paper, typically used in magazines. In 2002, when the facility opened its coated production line, it became the only mill in North America making recycled coated mechanical paper.
In 2009, a Boston-area private equity firm, the Watermill Group, bought the mill, renaming it FutureMark Paper Co.
Silver says being owned by a private equity firm offers significant advantages. “We can move quickly as a private equity firm. We also don’t come in with a pre-conceived notion of how the business is done. And, we have pushed hard, including heavy marketing for our products.”
This is key, he says, as the opinion of many other paper industry veterans is that paper is basically a commodity that does not require significant marketing. FutureMark’s publication papers contain more than 90 percent recycled fibers, with 30 percent of the total fiber mix coming from post-consumer sources. FutureMark notes that the average recycled content for coated magazine paper is less than 10 percent.
Steve Smith, vice president of operations for FutureMark, says the company uses a range of recovered fibers for its furnish, including old magazines (OMG), old newspapers (ONP), coated groundwood sections and a grade Smith calls “printers’ mixed waste.”
Smith estimates that FutureMark purchases approximately 110,000 tons of recovered fiber per year, with shipments arriving exclusively via truck. He says the company prefers receiving the material in loose form, which makes it easier to integrate with other raw materials.
While most of the raw material that feeds the mill comes from the Chicago area, Smith says FutureMark’s supply range extends to Milwaukee in the north and to western Indiana in the east.
While many paper companies have shuttered plants or even filed for bankruptcy protection, FutureMark has been operating at capacity, landing a number of large accounts in light of its unique position as North America’s only recycled coated groundwood paper producer.
Silver estimates that one-third of its finished products goes to coated paper for magazines, with the other two-thirds of production going to the catalog business. And, while many paper industry analysts have been forecasting the end of these two segments, Silver says the company continues to see strong orders for its finished products, adding that many of these predictions are overblown. “We have talked to a number of publishers, and they are telling me that they are selling their products.” He adds, “We are sold out for the rest of the year.”
Silver says FutureMark provides the coated recycled-content paper for Every Day with Rachel Ray, one of the fastest growing consumer magazines in the United States. The deal demonstrated that FutureMark could provide recycled-content coated paper of high enough quality to compete with virgin paper.
Furthermore, in the past several months, FutureMark has focused its sales and marketing efforts on companies with strong environmental programs. So far in 2010, the company has landed business from retailers Whole Foods, Staples and Walmart. FutureMark also produces specialty paper that is used for can labels to further diversify its product line.
Helping to keep the company’s run schedules strong is the fact that more magazines have embraced the call for the use of recycled-content paper. “There is a huge demand for recycled paper,” Silver says. “And we have proven it.”
Smith concurs. “It is a huge opportunity. We have taken the message of high recycled content paper and marketed it to Fortune 500 companies. They liked it.” He adds, “We are well positioned to take advantage of the green movement.”
NAVIGATING THE CURRENT LANDSCAPE
This good news, however, does pose concerns for the domestic paper industry going forward. Silver feels that if this push toward recycled-content coated paper can’t be met domestically, consumers will buy from overseas suppliers.
Glenn Davis, vice president of business development for FutureMark, also sees significant changes occurring in the paper industry. He questions the paper industry’s adaptability to the new dynamic, where paper companies are not only competing with local firms but also with companies in China, India, Mexico and other locations around the globe.
Silver says he feels that the overseas routes many recovered paper dealers are taking pose grave concerns, not only for his company, but for the U.S. paper industry in general.
“We have proven that there is a demand for recycled coated paper. However, the problem is that 70 percent of the collected U.S. fiber is going to China,” Silver says.
While this move may help paper stock dealers in the short term, Silver says, the potential longer-term problem could be far worse.
“The U.S. paper industry may not be competitive because U.S. paper manufacturers are being discouraged from investing in what U.S. customers want, and that is clearly recycled products.”
With so much material being shipped offshore, recovered paper prices have been driven up to the point where companies can’t justify installing new manufacturing capacity unless they have government subsidies, Silver says. “In a few years when China figures out how to collect their own recovered paper, they won’t need ours. Who will the collectors sell to if there are only a handful of domestic recycling mills?” he asks.
While many paper stock dealers say they would love to supply local consumers, Silver says FutureMark constantly struggles with its suppliers to get the right mix of material at a price that allows the company to prosper.
What makes this more challenging is that the company runs with minimal inventory. And, Davis adds, because the mill is in an urban environment, FutureMark does not have the flexibility other companies have in switching to a virgin pulp furnish if recovered fiber prices climb too high.
CHALLENGES TO BE CONFRONTED
In addition to concerns about the volume of recovered fiber being shipped offshore (especially to China), FutureMark is concerned about the quality of the material collected. Silver challenges the notion that the single-stream method of collection has been fully embraced and is the future of the paper recycling industry. “Maybe I am just Don Quixote,” Silver laughs, “but I don’t necessarily think single stream is going to be the way forward.”
He says the quality of quite a bit of the paper being collected is “terrible.” After extracting the contaminants, “5 to 10 percent of the material we’re paying for isn’t usable,” Silver says. He estimates that after pulling out contaminants and cleaning up the material the company is shipped, FutureMark pays an additional $8 to $10 per ton for the material.
Smith agrees that getting quality material is the foremost challenge. “With single stream, the waste has gone up, and the contaminants have increased.”
Davis adds that the lower grades of recovered fiber often generated via single-stream programs can be borne by mills in developing countries such as China that can afford to pay people to perform additional sorting of fiber loads. However, in the U.S., it is less economically feasible to undertake hand sorting at the mill.
Contaminated paper disrupts production and creates costly inefficiencies. Dealing with outthrows causes manufacturing downtime as well as more than $1 million per year in materials loss, disposal costs and remediation activities.
Going forward, FutureMark is focusing on improving its efficiency while getting good quality material, Smith says. “We have world-class equipment to make a world class product,” he adds.
The author is senior and Internet editor of Recycling Today and can be contacted at dsandoval@gie.net.
Get curated news on YOUR industry.
Enter your email to receive our newsletters.
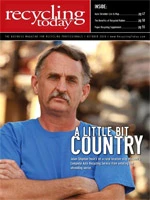
Explore the October 2010 Issue
Check out more from this issue and find your next story to read.
Latest from Recycling Today
- ReMA board to consider changes to residential dual-, single-stream MRF specifications
- Trump’s ‘liberation day’ results in retaliatory tariffs
- Commentary: Waste, CPG industries must lean into data to make sustainable packaging a reality
- DPI acquires Concept Plastics Co.
- Stadler develops second Republic Services Polymer Center
- Japanese scrap can feed its EAF sector, study finds
- IRG cancels plans for Pennsylvania PRF
- WIH Resource Group celebrates 20th anniversary