A firm operating out of the small town of Blackfoot, Idaho, is one of the nation’s largest suppliers of finished products manufactured from construction and demolition debris. The company, Trestlewood, a division of Cannon Structures, has achieved that status by adopting a philosophy of treating C&D materials as the raw material from which superior wood products can be manufactured and supplied to the custom building marketplace.
|
The company, which once sold most of its product to be used in low grade applications, today manufactures and dries finished lumber used to make specialized products for high-end applications in homes, commercial buildings, and other structures where rare beauty and rare woods are desired and appreciated. In creating and successfully marketing its "Trestlewood" brand product, Cannon Structures has performed an environmentally sound service even as it demonstrates that C&D scrap can be profitably processed into high value commodities.
A BRIDGE TO NEW MARKETS
Trestlewood came into existence, according to Bob Cannon, vice president of sales for the firm, as the result of a project the firm’s parent company undertook in 1993: The deconstruction of the Lucin Cutoff Railroad Trestle over the Great Salt Lake.
The trestle, at nearly 12 miles long, had been built in 1904 as a shortcut to the historic Promontory Point section of the first transcontinental railroad.
Replaced in the late 1950s by a solid fill causeway, the old trestle—no longer maintained—began to deteriorate. As pieces sloughed off, it became both a maritime navigational and environmental hazard so, in the early 1990s the decision was made to remove the historic old structure from the lake.
The removal of the trestle was a major undertaking The job consumed seven years of effort and produced more than 30 million board feet of material. About 10 million feet of that fiber was in Douglas fir timbers, while two million board feet of redwood decking also came off the trestle. Twenty million board feet of Douglas fir resulted from pulling the old structure’s pilings out of the lake.
Originally, Trestlewood had little intention of doing much more than deconstructing the trestle. "We were going to focus on salvaging the wood and loading it onto trucks and railcars for shipment to companies better equipped to manufacture it into products," Bob comments. The problem, he continues, was that, "Manufacturers large enough to handle the volume of material being salvaged were used to dealing with new logs and lumber. They were looking for standard stock that they could run through standard processes and turn into standard products."
The trestle wood, however, was definitely not standard stock. Like much C&D debris it is, when fresh off the job, contaminated with considerable amounts of metal. Making this wood even more distinctive is the large amount of salt it contains as the result of nine decades of immersion in the Great Salt Lake. According to Bob, "Tests show the poles we pulled out of the lake sometimes consist of as much as 20 percent salt by weight, with the salt going all the way to the core of the pole."
All that means, Bob continues, that while the metal and the salt make for special challenges in manufacturing wood products from the recovered trestle stock, they also make for a very unique and rare product once the wood has been properly processed. Unique patterning and colors seldom seen in wood are the norm rather than the unusual. The company decided that, "To fully realize the potential of the wood we decided we needed to take an active role ourselves in identifying and creating markets and producing products that were ideally suited to the unique features of the wood from the trestle."
A PRECISE PROCESS
The business approach Trestlewood’s owners developed to best make use of the wood recovered from the Lucin trestle, as well as additional wood the company acquires from other sources, involves three approaches the firm considers fairly unique in the business.
First, the company does quite a bit more processing of the fiber than most companies are equipped to perform. Second, for many of its major lines Trestlewood maintains much larger inventories than many other firms ever consider carrying. Last, the milling and drying facilities the company built due to the lack of such facilities elsewhere allow for more flexibility in terms of product than most firms can provide their customers.The processing done on the trestle wood, as well as on other recycled woods sold by the firm is important to users, Bob explains, because "Cabinet makers, floor installers, and other craftsmen and women want a product that is not only beautiful but also reliably sized and stable when installed. In the past, those craftspeople haven’t always been able to count on that stability with recycled woods, so they have tended to avoid them. We make sure that when they order from us they are getting what they ordered and that it is manufactured to the exacting standards necessary to assure as much stability as is possible with wood products."
To achieve the characteristics crafters demand in a fine product, Trestlewood’s raw material, when appropriate, is put through exactly the same kinds of processes a sawmill producing lumber from logs direct from the forest will use, with some notable exceptions.
One of those exceptions is that when recycled wood is manufactured into product the first consideration is metal removal. At Trestlewood, that task is accomplished using a combination of traditional methods as well as some specialized tools invented especially for the project by one of Cannon’s important subcontractors, Emil Hein of Hein Timber Products, Tetonia, Idaho.
Once the metal is removed, wood destined for higher end products is rough sawn at the Greats Salt Lake site using standard circle sawmills in preparation for more sophisticated processing. Rougher wood or wood not suitable for better grades of product is prepared for market and shipped. Better fibers are processed further either at the lake or at Cannon’s processing facility in Blackfoot, Idaho.
Sawing and lumber drying are the keys to the secondary processing trestle wood goes through as it is shaped into finished product. The two processes, working together, result in a finished product that is fully comparable to that exiting a modern mill producing lumber from newly harvested logs, says Bob Cannon.
Sawmilling is accomplished using one of the two thin-kerf band saws that Trestlewood owns made by Wood-Mizer, Indianapolis, Ind. Wood-Mizers are portable band sawmills that have come into wide use in recent years for processing logs or timbers traditional sawmills are uninterested in or are unable to handle.
Trestlewood makes use of the mills, according to Bob, because they are cost effective both in terms of initial acquisition and in reduced blade costs when sawing in wood where metal is present. The saws are also far safer than circle saws in metal infested wood, and, most importantly, less wasteful in high value applications. "The thin kerf (width of cut) allows for significantly better recovery than we can get with the circle saws," Bob comments. Material as long as 32 feet in length can be sawn on the company’s Wood-Mizer units.Lumber drying is seldom utilized in the wood recycling industry but, Bob says, it has become a crucial part of his own company’s efforts to provide customers with consistent quality fiber that is as stable as it can be made to be.
Because of the high value of the wood being reclaimed and the need to provide a quality product, Trestlewood selected dehumidification kiln technology as the option of choice in their plant.
Dehumidification kilns are widely used in the hardwood industry because they are more gentle on the wood being dried in them; are easy to operate for even inexperienced personnel; are inexpensive compared to most other options; and are simple to maintain. Those are all factors that attracted Trestlewood to the technology.
Trestlewood chose Nyle Dry Kiln Systems of Bangor, Maine, to supply the kilns for their own recycling effort in part, Bob says, because of that company’s experience in providing drying equipment to other sectors of the lumber industry. "We can dry 30,000 feet at a time, which is a very large capacity for a recycling company," he says. "But we do a lot more drying than is common in the industry. Our customers are finding that the wood is very stable when dried, even more stable than newly manufactured lumber is. We normally dry the wood to a 6 to 8 percent moisture content. The timber framers have found they love it. They can cut a joint today and a year from now the joint is still tight. That is something they value. Cabinet makers have been equally pleased and, of course, the stability is very important to a flooring installer taking pride in his or her work."
The salt in the trestle wood leads to some special challenges in drying the fiber. Wood from the pilings especially, takes as much as twice as long to dry as typical green lumber. Even more challenging, the metals and salts in the fiber can be very corrosive in a kiln environment. The company worked with Don Lewis, the president of Nyle Dry Kiln Systems, and a recognized pioneer in the dehumidification dry kiln industry to address the issue of the corrosion caused by the salt in drying, eventually developing solutions to the problem that have worked long term.. "Working with Nyle we figured out a way to dry the wood without corroding out the refrigerant system," Bob comments. "We’ve had no trouble since."
STORING AND SHIPPING
The second prong of Trestlewood’s effort to build and serve the marketplace with its product involves maintaining a substantial inventory when possible. Bob points out that when an architect or a builder has created something special they want to be able to build on that so repeatability is important.
"We want to be able to cover our customers so we maintain what some might consider to be massive amounts of inventory in some product lines," he comments. "Our willingness to maintain large inventories is something that sets us apart in our business. It’s also something our customers have grown to appreciate." At any one time a million board feet of recycled wood might be on hand at Blackfoot with several million more available at the company’s Promontory Point facility.
Bob is quick to point out that some woods are quite rare and cannot be inventoried in the huge quantities he likes to keep in stock but, he contends, in general, his company will, for most product lines, have large inventories on hand.
The large inventories kept on hand and the ability to mill and dry lumber to exacting specifications allows Trestlewood to successfully achieve its third major goal, that of providing exemplary customer service and an array of products seldom seen in the C & D wood recycling business. Wood-Mizer sawmills can, with a few second’s adjustment time, slice lumber to nearly any dimension a customer might require. The Nyle dehumidification kilns Trestlewood uses for drying provide equal flexibility in addition to the stability they bring to the wood.
In addition to the trestle wood that has been the base of the company’s efforts for some years, Trestlewood also purchases other deconstructed wood products in large quantities so that customers have a wider variety of options. A visitor to the Blackfoot location might see wood recycled from huge pickle vats neatly stacked next to Southern Yellow Pine timbers recovered from Chicago’s Spiegel warehouse demolition, with both flanked by Douglas Fir recovered from a plywood plant in British Columbia, Canada. The ever-present trestle wood from the Great Salt Lake’s engineering marvel is also well represented.That extraordinary flexibility in both processing ability and in the quantities and variety of inventory, Bob points out, allows his firm to be a problem solver for its customers. If a contractor needs a product sized to match an odd dimension some independent miller decided on 150 years ago, Trestlewood can cut wood to the required specifications on its Wood-Mizers. Or if an architect wants ceiling material cut to match flooring, the fiber can be milled with the flooring dried to the necessary moisture content in the Nyle dehumidification kilns. "We are a small family business but we have some abilities many firms in our trade do not have," Bob comments.
In demonstrating that C & D scrap can be successfully and profitably recovered, manufactured into high value products, and sold, not as an equal to newly milled wood but as a superior product, Cannon Structures’ subsidiary, Trestlewood, is providing unique services not only to its customers but to the larger community.
While recycling might be an environmental preference, it becomes a more common option when it is also found to be economically viable. In its creative approach to processing and marketing the fiber it recovered from the deconstruction of the historic Lucin Cut trestle, Trestle-wood has shown that recycling can be both an environmental and economic solution on similar projects.
The Bellingham,Wash.,-based author submitted this article on behalf of Cannon Structures Inc.
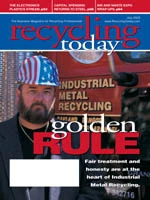
Explore the July 2003 Issue
Check out more from this issue and find your next story to read.
Latest from Recycling Today
- Steel Dynamics cites favorable conditions in Q1
- Hydro starts up construction in Spain
- Green Cubes unveils forklift battery line
- Rebar association points to trade turmoil
- LumiCup offers single-use plastic alternative
- European project yields recycled-content ABS
- ICM to host colocated events in Shanghai
- Astera runs into NIMBY concerns in Colorado