
The recycling industry is at a crossroads. North American recycling operations are having a tougher time accessing reliable overseas markets for their recovered fiber products. Rising global purity standards can be unobtainable using traditional recycling methods or too costly to meet by adding more manual sorters.
China’s National Sword and Blue Sky policies effectively closed the door of the world’s largest purchaser of recovered paper—and that was just the beginning.
“Markets like Indonesia, India and Japan are all following China’s example and demanding the same high purity standards for recycled material,” says Los Angeles-based Nick Doyle, recycling area sales manager North America West, Tomra Sorting Recycling.
Recovered fiber supply is high and demand is low. This has driven down the price of mainstay material recovery facility (MRF) recovered fiber products, such as mixed paper and old corrugated containers (OCC). For much of this year, mixed paper consistently has sold at a negative value or zero (at best) per ton in most markets. OCC is trading at the lowest levels seen in a decade. “It’s the simultaneous drop of both commodity prices that is hurting MRFs,” says Dan Gee, senior associate with Moore & Associates, an Atlanta-based consulting firm specializing in the paper recycling industry.
Market indicators show this being a long-term trend rather than a short dip in the market. “There is no quick fix for mixed paper,” Gee adds. “Most estimates are it will take a minimum of two or three years, possibly longer, for mixed paper to recover, and recycled paper quality required from MRFs will increase.”
Gee says he sees MRFs handling these current market challenges in several ways. Some are renegotiating contracts with their municipal customers, if possible. Others are simplifying the types of recyclables they will accept, while some are sending unmarketable material to the landfill. “Lexington, Kentucky, stopped accepting paper altogether,” he says. Still others are biding their time and hoping for a market rebound.
Hope is not a strategy
The U.S. recycles roughly 58 million tons of fiber products annually. With MRFs processing high volumes of fiber daily, sitting back and waiting for a market rebound could be a costly strategy.
“My customers tell me roughly 70 to 75 percent of their volume received is fiber,” Doyle says. “Most of the material inflow is sorted into products the operation either has to pay someone to take, or the value is a fraction of what it has been.”
If the paper market takes years to recover, Doyle questions the ability for MRFs to survive long term. Private companies receive hauling fees to take in recyclables, so this might be propping up some businesses. However, he suggests that MRFs start sorting paper differently to survive.
“Further sorting mixed paper to remove OCC will help to boost profitability.” – Nick Doyle, sales manager, Tomra Sorting Recycling
“While there isn’t money in mixed paper, there is money if this commodity is further separated,” Doyle says.
Mark Neitzey, sales director for Van Dyk Recycling Solutions, a builder of turnkey sorting systems based in Stamford, Connecticut, also tells his customers to examine the market from a supply-and-demand angle. “Say you run a soup business, and for years your customers wanted this one soup recipe; it was your cash cow,” he says. “Unfortunately, demand for that recipe has vanished, but there are opportunities for you to switch to other recipes and make more money.”
This metaphorical soup—mixed paper—has evolved over the years from a variety of fiber leftover after recovering other more desirable paper grades to now include corrugated boxes, chipboard, newspaper and office paper. Sold as mixed paper, this material has little-to-negative value in today’s market; but, if sorted further, these products demand higher value.
Doyle says, “Mixed paper sorted into individual components can result in much more revenue for the MRF, measured in the thousands of dollars per day.”
Rethinking separation
To survive, MRFs must rethink their recycling streams and practices to focus on making more profitable products that are in demand. “One MRF manager in the Southwest put it well when he said, ‘We are no longer in the business of making commodity grades. We are in the business of making products,’” Doyle says.
Estimates show approximately 40 percent of Americans shop online several times a month, resulting in the “Amazon effect,” where a significantly higher percentage of smaller OCC ends up in the single-stream residential recycling stream.
“We are not seeing as much large cardboard in single stream anymore,” Neitzey says. “Virtually everything comes in boxes today, so there are a lot of small boxes and chipboard in the stream.”
However, existing MRF sorting systems were designed to remove larger cardboard boxes. Doyle says small boxes act like paper, so more cardboard and chipboard ultimately end up in mixed paper. “Further sorting mixed paper to remove OCC will help to boost profitability,” he says.
Moore & Associates’ Gee says some MRFs are producing sorted residential papers and news (SRPN) rather than mixed paper. SRPN consists of newspaper, junk mail, magazines, printing and writing paper and other acceptable paper recovered from residential material. Depending on the region, this grade was selling for about $55 per ton as of early June.

Intelligent separation
Investing in sorting technology can help to improve recovered fiber revenue streams. Aware of today’s market trends and tightening purity standards that MRFs must manage, optical sorting equipment manufacturers have responded with new technological advancements to meet the sorting needs of today’s MRFs.
While robotics is a hot topic in the recycling industry, Neitzey says the savings from replacing manual sorters with robots only go so far. “While upgrading existing circuits is not as flashy as robotics, investing in intelligent separation through upgraded technology and rethinking sorting practices have the potential of saving the MRF hundreds of thousands of dollars a month in lost revenue,” he says.
For example, laser sorting technology promises to help deliver cleaner recovered paper grades, such as SRPN. Most MRFs include near-infrared (NIR) technology to positively or negatively sort paper. “NIR works great for sorting newspaper, white paper, magazines, PET (polyethylene terephthalate) bottles, milk jugs, etc.,” Neitzey says. “However, this technology cannot see the black bowl from a to-go container or glass from the belt, allowing some of this material to end up in SRPN as impurities or prohibitives.”
Laser technology, such as Tomra’s Laser Object Detection (LOD) and similar equipment from other manufacturers, identifies and removes these materials from the paper stream, helping MRFs to pass a mill customer’s sight test for bale quality.
This type of detection technology can be added onto an existing line or as a stand-alone unit on a new circuit, says Carlos Manchado Atienza, regional director Americas for Tomra Sorting Recycling, who is based in Shelton, Connecticut.
Consider the office
Commanding more than $100 per ton domestically and much more in certain markets, sorted office paper (SOP) may be the Holy Grail to help MRFs survive today’s mixed paper market. This product consists primarily of white and colored groundwood-free paper that is also free of unbleached fibers. It cannot contain more than 1 percent prohibitive materials and outthrows, plus prohibitives cannot exceed 5 percent.
SOP can be separated from the residential paper stream, but there is a catch. Unless the MRF has contracts with businesses or receives shredded paper, the percentage of white paper found in single-stream recycling can be limited and is market dependent.
Doyle is a proponent for MRFs sorting SOP and changing their business practices to take in more white paper. “Say the MRF receives $148 per sorted ton of SOP but is paying $2 per ton to offload mixed paper. That’s a $150 per ton swing toward profitability,” he says.
New optical sorting technologies also can aid in separating office paper from mixed paper. For instance, some technologies, including Sharp Eye from Tomra, can look through paper into its makeup to create a cleaner paper sort. Doyle says this type of technology offers customers the flexibility to choose between standard resolution for regular sorting and high resolution to recover products such as SOP.
Neitzey says tipping floor management also is key when it comes to separating office paper. “Blending everything together on the floor will reduce the amount of white paper an operation can separate from the mixed paper,” he says. “It’s best to sort out as much of the white paper as possible on the floor. Some customers currently do this and dedicate two or three days a week for sorting office paper.”
While targeting high-value products within the fiber stream isn’t new, the consequences of not doing so within the confines of today’s market conditions could be the difference between profitability and survival for a MRF.
Get curated news on YOUR industry.
Enter your email to receive our newsletters.
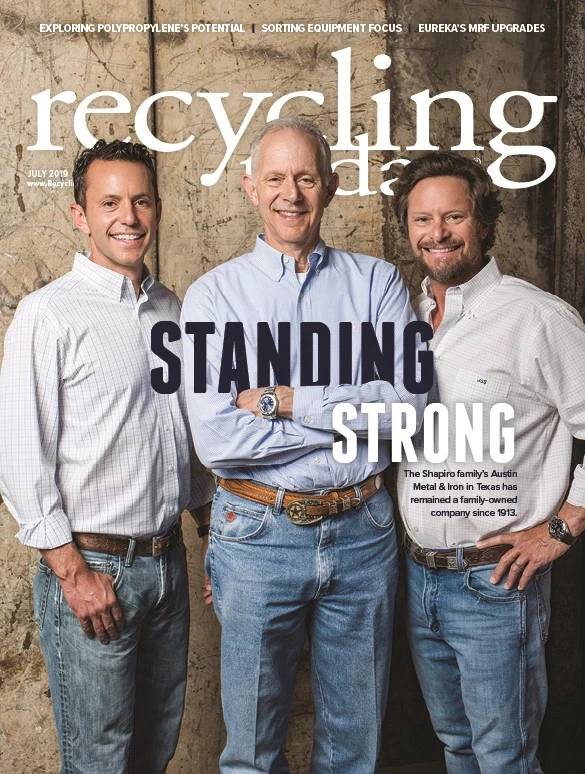
Explore the July 2019 Issue
Check out more from this issue and find your next story to read.
Latest from Recycling Today
- Returpack reports increased DRS activity in Sweden
- Trade groups align against European export restrictions
- Construction, auto sectors show mixed signals
- Politics in Turkey threaten recycled steel outlet
- Toppoint Holdings expands chassis fleet
- Lego creates miniature tire recycling market
- Lux Research webinar examines chemical recycling timetables
- Plastics producer tracks pulse of wire recycling market