Many questions surround asphalt shingle recycling. Are the shingles recyclable? Yes. Are some people making money doing it? Yes, definitely. Are others breaking even at best? Also yes. (So why do it?) Do government agencies support it? Sometimes. Do they inhibit it? Sometimes.
If this makes the field of asphalt shingle recycling seem somewhat murky, confusing, and unknown, for many entering the industry it is. How to get the shingles, how to process them once you have them, what problems will be encountered when processing them, and most importantly, what markets are available for the finished products are the basics to be answered before entering the business.
There is no definitive tome on the subject, although several good resources do exist. Like in other C&D recycling segments, many of the recyclers who handle shingles are reluctant to tell too many of their practices for fear of losing an advantage they have on their competition. Fortunately, several shingle recyclers across the country have offered information so readers can gain some insight on what is happening in the industry.
Asphalt shingle recycling has been called the next big thing in C&D recycling. An estimated 11 million tons of waste shingles are generated every year in the U.S. The overwhelming majority of them are post-consumer, mostly from tear-offs. There is a limited amount of asphalt shingle recycling going on in North America at this time, for a variety of reasons. Some are:
• Resistance in the marketplace. Some potential markets don’t want to try the material, or say it is not economical.
• Lack of specifications for those markets. Some work has been done in that area, and more is being undertaken now.
• Fear of hazardous contaminants in post-consumer shingles. The largest concern centers on asbestos.
• Governmental regulations. Some of these are related to contaminants, others are caused by regulator ignorance and inertia.
Market Resistance
Large-scale recycling of asphalt shingles is a relatively new industry to North America. The shingles have been recycled for years in Europe where several markets are active, including the following, which are also found to a lesser extent in the U.S.:
Hot mix asphalt (HMA). This is considered by many to be the best potential market for recycled asphalt shingles.
When asphalt shingles are new they contain anywhere from about 20% to 36% liquid asphalt. Recycling waste generated by the shingle manufacturing process can yield that valuable, petroleum-based product back when used as an additive for hot-mix asphalt. In addition, the small aggregate pieces used for shingles tend to be cubical, a superior shape for binding in road surfaces.
A few official, state-Department of Transportation (DOT)-sponsored studies1 have shown the benefits of using as much as 5% or more recycled manufacturers’ waste back into new HMA.
According to the National Association of Home Builders (NAHB), Washington, 10 states allow for the material to be used on DOT jobs.
The advantages of using manufacturers’ waste shingles, rather than post-consumer, in hot mix asphalt is that the infeed has a more uniform level of emulsion and aggregate, making it easier to provide consistent mixes, the kind best suited for highway jobs.
An example of this concept in use is being done by Bituminous Roadways in Minneapolis, Minn.
Manufacturers’ waste is ground to ¼-inch and usually fed at a rate of 5% of the volume, sometimes 10%, into the hot-mix plant. The product is used for commercial jobs and in St. Paul, where the city street commissioner allow its use on city streets. “They have had no problem with the streets containing shingles,” reports Kent Peterson, company president. The only problem the company has had was when it only ground the shingles to 3/8-inch before feeding to the hot mix, and sometimes tabs would slip through and stick up in the pavement. “Since we went to ¼-inch, nobody can tell the difference between regular asphalt and the recycled shingle one—not the graders, not the paving crew,” he says.
Tear-off shingle waste has also been used successfully for hot mix asphalt. Raisch Products in San Jose, Calif., has used the material in its hot-mix plants.
“We did several tests, some with just shingles added, some with shingles and RAP (recycled asphalt pavement). All the passes we paved with them are still holding up, and they have been in place for more than two years,” says Raisch’s John Armando.
Ken Patterson, an Atlanta-based asphalt shingle and wood recycler and grinder manufacturer, says the recycled demolition shingle market can be difficult. “To do post-consumer you need a hot plant operator doing off-spec, non-highway jobs. That’s a perfect marriage,” he says.
Some hot-mix plant operators are still resistant to adding shingles to their mixes, report some recyclers. They say they have enough recycled asphalt pavement (RAP) in there already, or that it is not economically feasible.
Also, older plants often are not equipped to properly handle the emissions shingles generate.
However, private talks with a few operators reveal that many, but not all, asphalt plant operators are making a very good return on shingle recycling.
Indeed, the Construction Materials Recycling Association had trouble filling a panel on shingle recycling at next year’s ConExpo-Con/Agg, as none of the contractors already processing shingles wanted to tip their hand as to how they are making money doing it.
Temporary roads, parking lots, driveways. Under these related applications, recycled shingles are processed to a certain size and spread over a designated area to provide a surface on which to drive. Because the specifications are less strict than hot-mix asphalt, this a common market for post-consumer shingle waste
Temporary roads, etc., have been done several times, several ways. One interesting application that was experimented with by Falcon Waste & Recycling, Harvard, Ill., was to take a manure spreader for farming and use that to lay down the tabs of manufacturers’ waste, followed by a roller to tamp them all down. It works wonderfully with the tabs, and requires no grinding, according Katherine Powles of Falcon.
But that is unique. Most of the time some, type of grinding needs to be done in order to get the material to a good size to lay down and compact.
Commonly this has been a coarse grind, about to 2-inches minus or so. Caution is advised, however, especially with post-consumer shingles as they contain nails and other metals. One large mixed C&D waste recycler who used to contract out his shingle grinding had the sub do that size, but the subcontractor’s magnet on the grinder that day wasn’t working and he didn’t tell the recycler. The processed material was laid down as dust control on a country gravel road near some ballparks. The result was about 20 tire punctures and some sensationalist stories on the local television newscasts.
Now the recycler grinds the dust control product to ¼-inch, saying that 3/8-inch is not enough because he put a box of roofing nails in there with the screen set at 3/8-inch and about a dozen got through. None got through at when the screen was set at ¼-inch.
Usually the waste shingle is put through either a tub or horizontal feed grinder, as impact crushers have been tried and found lacking for the application. One exception to that was developed by the late Kenneth Pixley in Altus, Okla., where he put a load of shingles in an impactor, along with a load of RAP2. The final product made a great parking lot material, and this practice is being continued today by a few recyclers around the country.
Roadbase. Not commonly used by itself as base, processed shingles are blended in with RAP and concrete by some recyclers to make a roadbase product. The material provides some added bonding to the product.
Fuel. The recovery of the btu (British Thermal Unit) value of waste shingles is a long-time and well-established market in Europe. Only recently has the concept been tried in the U.S., reportedly under controversy because of concern over emissions. Yet the technology exists to make it safe in the Old World, and with fuel prices going up in the New World, this may become a more lucrative market.
Cold patch mix. Ground shingles can be used alone or mixed with virgin asphalt or other materials as a patch material on roads. New Jersey was the site of a spectacular early failure of this concept, and to this day there has been a stigma attached with the idea. However, some recyclers, such Commercial Recycling Systems, Scarborough, Maine, report they have had success developing the product.
Molded products. Examples include parking blocks and stepping stones. These are small markets that probably will remain niches, but could provide another outlet to shingle recyclers.
Specifications
As stated, several states have developed specifications for shingle use in HMA mixes. And some hot-mix plant operators have created their own mix designs using the material, mostly for off-spec work. But, like recycled concrete, there is no one size and performance specification for recycled shingle use in HMA, either for size or performance.
Of course, there is none for the myriad of other uses, unless the company making a final product from the recycled shingle has set one.
The Recycled Materials Research Center, Durham, N.H., is considering trying to develop a guideline similar to the one it is developing for recycled concrete’s use in roadbase and in concrete aggregate, but that project is not moving forward.
Doug Gleason of Commercial Recycling Systems is on a state committee developing a spec for Maine to use shingles in HMA. But a lack of recognized specifications could be hurting the HMA market.
The “A” Word
“One of the main stumbling blocks for increased shingle recycling in the United States is the perception that shingles may contain contaminants such as asbestos at levels that are of regulatory concern,” according to Paul Ruesch, U.S. EPA Region 5, Chicago. “There is a lack of understanding of waste shingles’ properties.”
It is acknowledged by the asphalt shingle manufacturers that between about 1963 to the mid 1970s some of their number did use asbestos, a deadly carcinogen, in the fiber mat of their shingles. How many batches of asbestos-tainted shingles were sold as a fire-retardant product and where they were used is information the manufacturers won’t divulge, for the obvious reason of potential asbestos litigation. (Consider the bankruptcy resulting from litigation being experienced by USG Corp., Chicago.) But the amount of asbestos used in shingles was between 0.02% and 0.00016%, and it was only in a small portion of the manufacturers’ production3. Hence, the amount of asbestos in the waste stream is miniscule, both in the shingle itself and the number of shingles in which it is present.
Thousands of test results of incoming asphalt shingle loads to recycling centers are available from asphalt shingle recyclers across the country. Overwhelmingly they show the incidence of contaminated loads to be miniscule. Most sites testing report no hot loads, and some no longer even are required to check for the material. Others that do find it are reaping small amounts. For example, Central C&D Recycling in Des Moines, Iowa, handles about 80 tons of shingles per day and tests every load that comes in (more than they are required to do), just so they can assure their customers there is no asbestos in the final product. They have found three hits in more than 3,000 loads sampled. (All test results will be available on new CMRA website. See sidebar on page 22.)
Government Here To Help?
The small amount of asbestos found has not stopped regulators in several states and localities from banning the processing of tear-off shingles because of a fear of asbestos.
While still in the shingle, the material is relatively benign and non-friable. When it is ground, it can become friable and airborne. So rather than find a way to deal with the situation, some regulators at all levels, including the feds, can and do require all post-consumer shingles to go straight to a landfill and will not consider recycling alternatives. “Governments say they want to promote recycling, but once somebody starts doing shingles, then it’s a problem to them,” says Ken Patterson.
Fortunately not all state and local regulators are short-sighted. The U.S. EPA is funding the CMRA website on shingle recycling. Several states have done studies on the feasibility of their use, or have tried the recycled products and found them workable. It has been said that if all HMA produced in the United States were required to have 2% to 3% recycled shingle content, well below the maximum current recommended level, then there would not be enough shingles to fill the need. Admittedly there are some difficult logistics involved and the technology is not all the way there to handle this, but that would be the way to divert all the recyclable shingles away from landfills and into a product where they can be used again and again.
Government interferes with shingle recycling in other manners. Gene Rieche, National Converting & Fulfillment, Ennis, Texas, says that markets for recycled shingles were difficult to develop at first, but the company has been successful in overcoming that and now has five recycling sites going.
However, his biggest obstacles now are nearby landfills and the local government. “The landfills say they have a franchise agreement with the cities for that industrial waste,” he says. “They say they are going to recycle the shingles, but they don’t. They threaten lawsuits to make sure they get the waste. So do the cities which get a part of the tipping fee for signing the franchise agreement.”
Probably the most egregious example of governmental regulation belongs to an East Coast recycler handling tear-off shingles. He is required to test for asbestos every load that comes in, be that a wheelbarrow or a 40-yard roll-off. In addition, each load must be inspected for three constituents: shingles, tarpaper, and roof cement. Obviously, those three are in virtually every load. If present, each item must be tested separately for asbestos, meaning three tests per load. Making matters worse, the recycler doesn¹t even want the tarpaper or mastic in his final product, which is going out for either hot-mix additive or road base. But even though he is separating and throwing away the tarpaper and mastic first, he has to test the materials for asbestos.
While awaiting the test results, the waste shingles must be kept covered. He puts the material into 30-yard roll-offs for the couple of days it takes to get the test results, providing a logistical nightmare. After a year of operation and 1,800 tests, there have been few hits, all in the tarpaper he doesn’t want anyway. “Asbestos testing is just a waste of money,” he says.
Not all recyclers have had negative interaction with the government while trying to set up a recycling plant. For two years Kathy Powles of Falcon Waste & Recycling in Harvard, Ill., worked to get a permit to process shingles. While she will admit to several frustrating moments during that time, she now feels she knows the bureaucracy better and what they want and expect.
What can the shingle recycling industry expect in the future? There is little doubt that shingle recycling will expand, despite the best efforts of regulators who fear asbestos contamination. There is too little contaminant in the overall waste stream, support of recycling is growing, and people can make money doing it. Anyone entering the business should be very careful to make sure they have at least one, and preferably two or more, markets for the finished product.
Asphalt shingle recycling remains an evolving industry, one that bears watching.
Footnotes
1. “Influence of Roofing Shingles on Asphalt Concrete Mixture Properties,” June
1993, Report No. MN/RC-93/09, Minnesota Department of Transportation;
“Roofing Shingles and Toner in Asphalt Pavements,” July 1996, Report No.
FHWA/TX-97/1344-2F, Texas Department of Transportation
2. Construction Materials Recycler, Volume 1, Number 20, Oct. 22, 1999
3. “From Roofs To Roads,” 1999, National Association of Homebuilders Research Center
Sidebar
CMRA/EPA WEB SITE
By the end of 2001 the Construction Materials Recycling Association (CMRA), thanks to a grant and research support from U.S. EPA Region 5, will have filled a Web site with all the information it has found on asphalt shingle recycling.
Included will be a list of studies and reports on recycled shingle use. In addition, test results gathered from shingle recyclers all across the U.S. will be summarized and accessible to show the threat contaminants pose in shingle recycling. Once set up, the Web site can be accessed through either www.shinglerecycling.org or www.shinglerecycling.net .
“We recognize that recyclers are ready to move ahead and process more shingles, and that governments would like more recycling, but it is not happening because of concerns of regulatory interpretation,” says Paul Ruesch of U.S. EPA Region 5, Chicago.
“The Web site is designed to increase the level of understanding of what the asphalt shingle waste stream is, and not what it is perceived to be.”
The CMRA Asphalt Shingle Committee will review the material before it is posted. The committee is made up of Kathy Powles, Falcon Waste & Recycling, Harvard, Ill.; Dale Behnen, Peerless Landfill, Valley Park, Mo.; Gene Reiche, National Converting & Fulfillment, Ennis, Texas; Ken Patterson, Patterson Services, Mableton, Ga.; and Kent Peterson, Bituminous Roadways, Minneapolis, Minn.
For more information on the Web site, contact the CMRA at 630/548-4510. In addition, at ConExpo-Con/Agg in Las Vegas next March there will be a special session on asphalt shingle recycling.
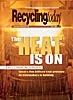
Explore the July 2001 Issue
Check out more from this issue and find your next story to read.
Latest from Recycling Today
- Steel Dynamics cites favorable conditions in Q1
- Hydro starts up construction in Spain
- Green Cubes unveils forklift battery line
- Rebar association points to trade turmoil
- LumiCup offers single-use plastic alternative
- European project yields recycled-content ABS
- ICM to host colocated events in Shanghai
- Astera runs into NIMBY concerns in Colorado