
In the United States today, fewer automobile shredders are operating as scrap metal recyclers face declining incoming volumes and lower metals prices, which are creating competition for available tons and narrowing margins.
For the first time in at least a decade, the number of auto shredders operating in the U.S. has dropped. That’s according to the most recent findings from Recycling Today, which publishes its U.S. Auto Shredder List and Map every two years, with the last list having been published in 2014. (To view the map in its entirety, click here.)
We have identified 274 shredder installations in the U.S., with 15 of those operations currently idled. In 2014, the U.S. was home to 297 shredders, only two of which were idled, marking the highest number of shredders running since Recycling Today began producing this list. (Including shredders in Canada and Mexico, the shredder count in North America climbs to 298.) For comparison’s sake, 292 shredders were installed in 2012; 290 in 2010; roughly 250 in 2008; and some 220 in 2006.
While the number of operating shredders is down, so are peddler traffic, industrial generation and scrap pricing. Of those shredders still operating, many have reduced their hours of operation.
Shredder operators say competition is tough. Although they might have lost competitors in their regions, competition has not eased up necessarily because less scrap is being generated.
Recyclers point to this decreased flow into scrap yards as the most significant reason for the nation’s idled and shuttered shredders. As ferrous scrap pricing has come down, volumes also have dropped.
As the price of ferrous scrap has dropped from an average of $360 to $220 per ton, it makes less economic sense for peddlers and industrial sources to make an effort to recycle scrap, says Mark Sweetman, chief financial officer of SA Recycling, an Anaheim, California-based metals recycler and processor. He offers an example where a demolition company that at one time would have removed concrete from rebar for recycling now sends that material to a landfill.
Sweetman says reduced material flows have forced recyclers that are still in the shredding game to compete harder for feedstock.
“The reduced flows have put more pressure on shredders to buy whatever feedstock they can economically reach,” Sweetman says.
He continues, “Competition is probably as aggressive or more so [today] than [in] 2014.”
State of overcapacity
Many scrap metal recyclers have been claiming that the U.S. has an overcapacity of shredders for a number of years and that rationalization was necessary. That appears to be occurring now, as nearly 30 auto shredders have shut down and are no longer in operation since Recycling Today last published its auto shredder list in 2014. At 15 total, 13 more shredders have been idled today than two years ago.
Texas again tops the list in 2016 with 25 shredders. The country’s second largest state lost half—two out of four—of the shredders located in Brownsville to closures over the past two years, with two additional shredders idled in the state.
With 16 shredders each, Ohio and Florida share the No. 2 spot for the largest number of auto shredders. The Ohio cities of Canton, Columbus and Toledo each are home to two shredder installations.
Pennsylvania rounds out the top three in 2016, with 15 shredders in operation.
The most notable change occurred in New York, which had half of its shredders cease operating over the last two years. As was the case with the 2014 list, New York saw the most shredder shutdowns than any other state.
However, unlike years’ past, few new shredder installations have opened or been announced in the last two years.
Gaining a competitive advantage
While Sweetman and several other recyclers interviewed for this article say investing in a new auto shredder today would “seem crazy,” a few proposed shredder installations could open soon. Two companies planning installations are Excel Recycling in Westport, Massachusetts, and Interstate Metal Recycling in Hazelton, Pennsylvania.
Total Metal Recovery Inc.’s (TMR’s) Laval, Quebec, mega shredder, the first large shredder project built from scratch in North America in several years, is expected to open by the end of 2016, says Wendt Corp., the Buffalo, New York-based supplier of TMR’s new shredder.
Wendt will supply the scrap metal recycling company with a newly designed 106-inch-by-115-inch shredder that features a Bowe disc rotor and a 6,000-horsepower motor.
TMR plans to process automobiles and other shreddable materials, producing 250,000 tons annually.
Claude Verret, TMR chief operating officer, said at the time of the announcement, “We wanted to gain a competitive advantage in a tough market.”
The company has recognized the need to recover more metals from the postshredder stream to stay competitive, so Wendt also will supply a nonferrous recovery system that includes TOMRA Sorting’s sensor-based Finder technology. The nonferrous system will recover traditional nonferrous metals, such as aluminum (zorba) and stainless steel (zurik), in addition to copper wires and minus-10-millimeter fines that contain precious metals.
Verret said, “In today’s market, you don’t have the choice not to get the latest technology because all of the margin is in ASR (auto shredder residue), and that’s the reason we purchased the system from Wendt. We have to get the maximum level of metal from the ASR to be competitive.”
Nonferrous recovery systems can help recyclers significantly improve their margins and are “extremely important,” Sweetman says.
He recognizes these systems are not inexpensive, yet downstream nonferrous and plastics recovery plants will become “more and more important,” Sweetman says. While the several-million-dollar investment may be tough for smaller operations to justify, shredder operators may find it difficult to compete without this component, he adds.
“I am not sure how you would compete in the shredding business today without nonferrous recovery plants,” he says.
Nonferrous metals recovery is so critical that one shredder manufacturer says “it is not possible to operate a scrap steel shredding plant profitably without capturing a significant part of the available value in the nonferrous metals that report to the ASR.” Scott Newell, CEO of The Shredder Co., based in Canutillo, Texas, says nonferrous metals now are considered a coproduct rather than a byproduct of the overall shredded stream.
Two recent installations illustrate the importance of these systems. In September, SMS Shredding, New Carlisle, Indiana, applied for two tax abatements with the County Council of St. Joseph, Indiana, for its planned $3.5 million shredder facility expansion project. The company is a subsidiary of Scrap Metal Services, based in Burnham, Illinois.
SMS Economic Development Director Bill Schalliol said at the time that the company’s project calls for equipment that will enable it to process more shredded metal from scrapped cars that would otherwise be landfilled as waste. The expansion also will include erecting a building to cover the new downstream system.
The shredder and downstream system installed at Ben Weitsman of New Castle in Pennsylvania includes separation technologies to recover wire, plastics, nonferrous metals and other materials, such as fines, from the shredded material.
Upstate Shredding – Weitsman Recycling, headquartered in Owego, New York, acquired the New Castle scrap yard, formerly known as Ferromet, at a bankruptcy auction in December 2012. The new shredder, full nonferrous downstream and retail scrap metal recycling facility opened in May 2016.
Becoming a smarter operator
Recyclers who have been around the industry for some time are aware of the boom and bust cycles that can affect scrap pricing. They have dealt with shifting market prices for the last two years.
As recently as September 2016, domestic mills early in that month paid some $25 to $40 less per ton for ferrous scrap, depending on the grade and mill location, according to the American Metal Market Midwest index, cited in the article “Unwanted Shift in Gears,” beginning on page 26 of this issue.
To make it through this cycle, recyclers say they have had to become smarter operators by focusing diligently on their operating budgets.
Some recyclers say their companies haven’t been able to grow as much over the last few years as a result of investing less in people and equipment.
“I used to fly out every month to go look at a facility or go learn from someone at seminars, and now it doesn’t make any sense to do that because we’re not going to do any capital improvements yet,” says a source with a scrap management and brokerage services company based in the Midwest. Once the market picks back up, he foresees his company allocating money for facility visits and additional training.
In an effort to improve their profitability, some scrap recylers have divested operations.
Sims Metal Management, which maintains executive offices in New York and in Sydney, sold operations in several states so far in 2016. In mid-August, Sims sold six facilities in Mississippi and Tennessee to OmniSource Corp., a subsidiary of Fort Wayne, Indiana-based steelmaker Steel Dynamics Inc. In mid-September, Detroit-based Ferrous Processing and Trading Co. (FPT) announced its purchase of two Sims operations: Sims Metal Management Detroit and Sims Metal Management Toledo in Ohio.
SA Recycling acquired Newell Recycling Southeast LLC, including a shredder installation in El Paso, Texas, and all of the installations in Georgia and Alabama, Sweetman says.
He says most recyclers have been on a push to cut operating costs wherever they can. “This of course has been the mantra for most since 2009, so it has become more difficult with each passing year to find ways to cut,” Sweetman says.
Get curated news on YOUR industry.
Enter your email to receive our newsletters.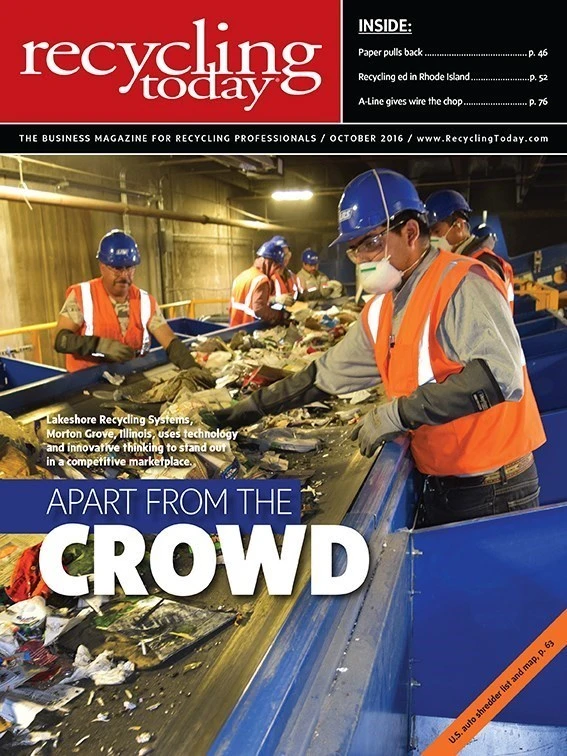
Explore the October 2016 Issue
Check out more from this issue and find your next story to read.
Latest from Recycling Today
- Li-Cycle reports 2024 financials
- PureCycle, Landbell Group working to advance PP recycling in Europe
- S&P Global launches mixed plastic scrap pricing for US, Europe
- Organizations call for coordination on product safety
- Circular Services acquires Waste Recycling Inc.
- Aqua Metals issues 2024 progress report
- e-Stewards, Bloom ESG release environmental benefits calculator
- RecycLiCo engages Fusion Projects to assist with facility site selection