
To much of the general public, the wrecking ball swinging on the end of a crane and the implosion of large structures are the images brought to mind when thinking about the demolition industry. But most demolition professionals know that implosions bring down less than 1 percent of all buildings and that the wrecking ball is becoming rarer in demolition projects in favor of controlled demolition.
Loosely defined, controlled demolition is the taking down of a building in a safe manner that allows the debris generated to be under the control of the demolition contractor as much as possible and not bouncing around the job site.
Controlled Demo at Work in the Windy City |
When Donald Trump comes to town, people notice. And when he came to Chicago to build one of the biggest buildings in the city along the Chicago River, people really noticed, including Mayor Richard Daley. On top of that, Trump wanted the building on the site of a venerable local landmark, the Chicago Sun-Times building, which meant even more scrutiny. It didn’t help that in the middle of the wrecking, "The Donald" and "Da Mayor" got in a public spat over the design and height of the new building. That was the microscope Brandenburg Industrial Service Co. was working under when it began demolishing the long-time headquarters of one of Chicago’s two daily newspapers. The company worked six days per week, 12 hours per day to quickly clear the site, all while recording no employee accidents. It could not be a more urban job: On one side was the Wrigley Building, on another, the IBM Building, on the third, a mostly residential luxury high-rise. The Chicago River made up the fourth side. The 1950s-era Sun-Times building was bigger than it looked, William Moore of Brandenburg says. Its 55,000 square feet and nine stories were L-shaped, meaning some of the structure wasn’t easily seen from the street. It was also sturdier than most believed, Moore adds. While most people thought it to be concrete framed, it turned out that concrete only sheathed a steel frame. In addition, as the building is right on the river, there was concern about debris falling into the water. Brandenburg tied up two barges right next to the building to catch any falling debris, purely as a safety measure. No material was loaded on the barges. The barges allowed for no scaffolding to be used, which would have been a much more expensive alternative. At the start, skid-steer loaders with hammer attachments were lowered onto the building roof to help gut the building and get the concrete off the steel. All the material was sent down a chute in the middle of the building into the basement for load out. About 62,850 tons of material was generated by the project, reports Moore. About 2,800 tons was waste, "about the only things that couldn’t be recycled," he says. Of the rest, 55,000 tons of it was concrete, 4,900 tons was steel and another 150 tons was nonferrous metals. All of it was recycled, including the concrete. "Why wouldn’t we recycle it?" says Moore. "We would have to pay $400 to $500 per load to dump it at a transfer station, as opposed to $10 to $50 per load at the recycling plants. And they are all closer than the transfer stations," he adds. Brandenburg’s part of the job was finished by the start of April 2005, but even before that, end caisson drillers were working on one side of the property while the demolition company finished on the other. Because Brandenburg did the job on time, safely and with no real complaints, Trump couldn’t use his famous line on the company: "You’re fired." |
Perhaps the best means for acheiving controlled demolition is to use modern demolition equipment—a high-powered excavator with a specialized attachment.
IN WITH THE NEW. "It used to be that excavators and loaders were only used to sort and load out materials," says William Gumbiner of Demolition Industry Consultants, Noblesville, Ind. "Now, with all the attachments, excavators are on the front line of the demolition job."
These machines are taking the place of the long-time industry stalwart, the crane equipped with a wrecking ball. According to some demolition contractors across the country, cranes are still being used, but not as much as they used to be for a variety of reasons.
First and foremost seems to be a dearth of skilled operators. There are few replacements for the large number of older operators retiring. "Everyone used to have a lot of crane operators," says Gumbiner. "They are just not around any more."
Berger Jostad of Viking Demolition, Glendale, Calif., is an industry veteran who says he "never did like that thing wobbling on the end of a string." He adds, "It didn’t seem to matter how experienced the operator was, he couldn’t always control the ball."
Jostad says he sees very few buildings being taken down with the wrecking ball anymore, in part because "cities won’t let you swing the ball any more; it is a violation of permit." When a wrecking ball is used, it is usually just dropped to break up concrete floors.
Drew Lammers of King Wrecking in Cincinnati uses an example of a 15-story building being demolished while flanked by 10-story buildings to illustrate the importance of control. "It takes much more experience to control the wrecking using a crane and ball."
Indeed, Lammers says he is of the opinion that the ball and crane are being phased out and may even be banned altogether one day.
MONEY MATTERS. Another reason the wrecking ball is not being used as much may be simple economics. Lammers says the cheapest way to demolish a smaller building is with an excavator and skid steers equipped with primary demolition attachments.
Gumbiner says cranes were needed in the past to get taller buildings down. "You can still do it that way," he says, "if you can find the operators."
Sponsored Content
Labor that Works
With 25 years of experience, Leadpoint delivers cost-effective workforce solutions tailored to your needs. We handle the recruiting, hiring, training, and onboarding to deliver stable, productive, and safety-focused teams. Our commitment to safety and quality ensures peace of mind with a reliable workforce that helps you achieve your goals.
Sponsored Content
Labor that Works
With 25 years of experience, Leadpoint delivers cost-effective workforce solutions tailored to your needs. We handle the recruiting, hiring, training, and onboarding to deliver stable, productive, and safety-focused teams. Our commitment to safety and quality ensures peace of mind with a reliable workforce that helps you achieve your goals.
Sponsored Content
Labor that Works
With 25 years of experience, Leadpoint delivers cost-effective workforce solutions tailored to your needs. We handle the recruiting, hiring, training, and onboarding to deliver stable, productive, and safety-focused teams. Our commitment to safety and quality ensures peace of mind with a reliable workforce that helps you achieve your goals.
Sponsored Content
Labor that Works
With 25 years of experience, Leadpoint delivers cost-effective workforce solutions tailored to your needs. We handle the recruiting, hiring, training, and onboarding to deliver stable, productive, and safety-focused teams. Our commitment to safety and quality ensures peace of mind with a reliable workforce that helps you achieve your goals.
Sponsored Content
Labor that Works
With 25 years of experience, Leadpoint delivers cost-effective workforce solutions tailored to your needs. We handle the recruiting, hiring, training, and onboarding to deliver stable, productive, and safety-focused teams. Our commitment to safety and quality ensures peace of mind with a reliable workforce that helps you achieve your goals.
Sponsored Content
Labor that Works
With 25 years of experience, Leadpoint delivers cost-effective workforce solutions tailored to your needs. We handle the recruiting, hiring, training, and onboarding to deliver stable, productive, and safety-focused teams. Our commitment to safety and quality ensures peace of mind with a reliable workforce that helps you achieve your goals.
But with today’s high-reach excavator equipment, a more than 90-foot reach is possible. (See sidebar, page 72.) And while commercial work can often be taller than that, almost all industrial demolition is shorter than that, making the excavators ideal.
Economics also favor modern demolition equipment because of labor savings. Gumbiner recalls the days when some jobs would require 80 torch operators to complement the crane, just to get the building down. "Now you might only see 10 on the job, so the excavator makes it safer," he says.
In fact, many demolition contractors say that projects where the ball is appropriate are dwindling, making operators difficult to find.
However, Dennis Wager of Impact Demolition, Vancouver, British Columbia, Canada, says that having cranes and operators make sense "if you can keep them busy."
Robert Elster Jr. of Apollo General Insurance Agency, Sonoma, Calif., says that a lot of insurers won’t insure the wrecking ball jobs anymore. "It is a perception from the old days," he says, "when everybody seemed to have a claim." He adds, "But if we have a good contractor with an experienced operator, we don’t have a problem getting him insured."
But Elster wonders why someone would want to use the crane "with all that great [new] equipment we have out there to do the job."
This new equipment, especially the hydraulic excavators and their primary demolition attachments, has helped reduce the number of claims and improve the demolition industry’s safety record.
Gumbiner says he thinks there always will be a place for the wrecking ball and crane in the marketplace. "Cranes will never go away," he says. "You still have buildings that are heavily concrete, very tall and can’t be shot. For those, the best option could be the wrecking ball."
This feature originally ran in Construction & Demolition Recycling. The author is associate publisher of that title and executive director of the Construction Materials Recycling Association. He can be reached at turley@cdrecycling.org.
Get curated news on YOUR industry.
Enter your email to receive our newsletters.
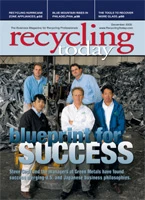
Explore the December 2005 Issue
Check out more from this issue and find your next story to read.
Latest from Recycling Today
- LumiCup offers single-use plastic alternative
- European project yields recycled-content ABS
- ICM to host colocated events in Shanghai
- Astera runs into NIMBY concerns in Colorado
- ReMA opposes European efforts seeking export restrictions for recyclables
- Fresh Perspective: Raj Bagaria
- Saica announces plans for second US site
- Update: Novelis produces first aluminum coil made fully from recycled end-of-life automotive scrap