Proper processing equipment is one important key to keeping scrap yards and recycling facilities functioning at peak efficiency. If there truly is "a place for everything, and everything in its place," then for small-to-medium size yards – those that process less than 150 tons of ferrous and nonferrous scrap a day – a piece of equipment called the shear-baler seems to have found its place.
As its name implies, the shear-baler takes two distinct scrap metal processing functions, shearing and baling, and combines them into one piece of equipment. By doing so, the shear-baler is packaged as an affordable item that saves a processor manpower time and cost, ultimately making the yard more profitable.
HOW IT WORKS
Shear-balers on the market today come with shearing forces ranging between 300 and 800 tons. Bale sizes usually are 24-inch cubes, and most of the equipment can make logs (long bales) of various sizes and length. Capacities are dependant on the material being baled and the density of the bales, or the material being sheared.
The shear-baler can be either stationary or portable. Some come with attached cranes, and are even capable of full operation via remote control. They can cut scrap like an ordinary guillotine shear, or bale sheet iron like a high-density baler.
For baling, metal is placed in the open charge box. The charge box then closes using two hydraulically-operated sizer or wing doors that fold over one another and compress the material down-ward. A ram then compresses the material horizontally, pushing it to the throat of the machine where the shear comes down and cuts the scrap during the shearing process. The pusher cylinder presses the scrap against the hold down, making the high-density bale. After reaching full pressure, the bale is ejected out of the throat by the pusher ram.
For shearing, metal is placed in the charge box as with baling, but as the ram pushes the material toward the throat, the shear continuously works to cut the metal.
Shear-balers can process many types of ferrous and nonferrous metal, and some can even shear or bale a whole car.
"It’s a versatile piece of equipment," says John Sacco, president of Sierra International Machinery, Bakersfield, Calif. "It opens up markets and gives the processor more options. One customer may want bales, another may not – but the capability is there to do either."
Making logs is another capability of the shear-baler. According to Sacco, one processor makes logs that are sold to another company which shreds them in a heavy-duty shredder. "Again, the processor is adapting to the market with the shear-baler," he says.
Sierra claims to have introduced the first shear-baler to the industry in 1985. Sierra shear-balers, sold under the Idromec name, range from 300 to 700 tons of shearing force and can be fitted with attached cranes. "We are scrap processors ourselves, so we have the hands-on experience in the yard," says Sacco. "We knew what worked and what didn’t, and it gave us a good idea of what was needed in the market."
FOR SMALLER YARDS
The shear-baler was designed with the small-to-medium size scrap processor in mind, according to the suppliers and manufacturers of the equipment. It is recommended mainly for a yard that processes between 20 and 150 tons of scrap a day. If an operation is doing much more than 150 tons a day, the shear-baler may become under-utilized because the throughput capacity is not there to handle the increased amount of scrap.
"If you buy it and find that you are only using it to shear or bale, then you are not getting your full use out of it," says Sacco. "Many times a dealer will underestimate the amount of material he processes per day, then end up purchasing the wrong piece of equipment."
Although some processors like having the option available to either shear or bale, Jim Langland, vice president of sales for Al-jon Inc., Ottumwa, Iowa, warns processors to make sure the equipment fits into their operation. Al-jon sells a shear-baler made by Vezzani, Italy, that can be fitted with an attached crane and be operated via remote control. The two models have shearing forces of 500 and 800 tons, respectively.
"If you are just going to shear, then buy a shear," says Langland. "If you are just going to bale, then buy a baler. I would recommend a shear-baler for a yard that is doing about 3,000 tons a month and under."
The shear-baler is for a "select market," reinforces James Farrow, southeast regional sales manager for Harris Waste Management Group, Peachtree City, Ga. Harris makes two models of shear-balers in the 300- and 500-ton shearing capacities. "It’s a popular piece of equipment," he says, "but for the smaller scrap dealer who wants to minimize capital outlay and maximize production." Farrow recommends the shear-baler for yards that are processing about 5 to 10 tons of metal an hour.
Processors have to be sensitive to the limitations of a shear-baler, particularly a throat that is less than 30 inches wide, according to Gunn Phillips, vice president of sales for Lindemann Recycling, Charlotte, N.C. He also recommends comparing shear speeds.
"The equipment is designed for a processor who may not have enough material to be shearing all the time, or baling all the time," he says. "It is definitely for the smaller processor who needs that multi-purpose capability at an economical price."
Lindemann has had good success with selling shear-balers in Europe (they are manufactured in the United Kingdom), and recently sold its first two shear-balers in the United States. Lindemann shear-balers basically operate in the same fashion of other shear-balers, but also use an extra door, or platen, that slides in front of the shear blade for baling.
"The sliding door absorbs the baling force and helps protect the shearing bale assembly," says Jeff Zack, sales representative for Lindemann. Lindemann shear-balers and others can also be fitted for remote control operation, and can be fitted with an attached crane, but Phillips likes a separate crane for more flexibility in the yard, and for higher capacity.
PREVENTING BALER JAMS |
Mike Tryon, president of Harris Waste Management Group, Peachtree City, Ga., offers some solid advice for avoiding baler jams. Nothing robs productivity in a baling operation more than a jam. The chief cause of baler jams is an overcharged bale chamber. That is why operators must monitor a baler’s pressure gauges and indicators to make sure that the baler is being properly charged. And there are other steps that can be taken to reduce those productivity-robbing jams in your baler. First, make sure all regularly scheduled maintenance and adjustments on the baler are performed. Properly maintaining a baler goes a long way toward eliminating jams by making sure that all systems are in good working order. Yet once the baler is operating according to the specifications, success in avoiding jams revolves around proper flow management. Regulate the move-ment of material into the hopper so that the flow remains even and steady. The operator should always stay alert during baler operation to quickly detect problems and make adjustments. Operators also need to make cer-tain that the baler is set for the correct density of the material being baled. Many jams occur when shifting from one material to another. To prevent jams when switching materials, stop the supply of the first material to the feed conveyor. Then, bale the remaining material in the feed hopper and on the conveyor. Once all the previous material has cleared the feed conveyor, turn the feed system off. Before the final bale is completed, cycle the main ram several times to make sure that the feed hopper is cleared. Next eject the bale and apply the wire ties. Then cycle the ejector ram to make sure the bale chamber is cleared. Finally, change the material and restart the feed conveyor. Some balers have a bale release that reduces the severity of the jam and the amount of production time lost during the clearing procedure. The bale release mechanism allows the operator to eject overcharged bales without shutting down the machine. If the baler lacks a bale release when the jam occurs, stop the feed conveyor or material feed process. Retract the main ram, and observe the material in the hopper to see if it falls away from the shear knife. Then cycle the main ram forward to see if the jam clears. This process may need to be done several times to free the bale. If the jam fails to clear, retract the main ram approximately half way. Shut the machine down and lock it out according to recommended shut down procedures and OSHA, ANSI requirements. Then clear the obstruction.. |
REPORTS FROM THE FIELD
For the small- to medium-sized yards, it is difficult to go wrong with the shear-baler because the machine is so versa-tile, says Sacco. Mike Lewis, president of Lewis Salvage, Warsaw, Ind., agrees. Lewis owns a shear-baler that he has had for seven years. He says he was one of the first processors to purchase the machine in the late 1980s. "Back then, we were a small yard, doing only a few hundred tons a day," he says. "Now we are up to 3,000 tons a day, and the shear-baler has helped us achieve that capacity. It has helped us compete with the larger processors who have bigger operating budgets and millions of dollars worth of processing equipment."
Affordability of the shear-baler is a major selling point, according to Lewis. He says that he has been able to recover the cost of the machine in just five years, and expects to keep it for many more years.
Sponsored Content
Labor that Works
With 25 years of experience, Leadpoint delivers cost-effective workforce solutions tailored to your needs. We handle the recruiting, hiring, training, and onboarding to deliver stable, productive, and safety-focused teams. Our commitment to safety and quality ensures peace of mind with a reliable workforce that helps you achieve your goals.
Sponsored Content
Labor that Works
With 25 years of experience, Leadpoint delivers cost-effective workforce solutions tailored to your needs. We handle the recruiting, hiring, training, and onboarding to deliver stable, productive, and safety-focused teams. Our commitment to safety and quality ensures peace of mind with a reliable workforce that helps you achieve your goals.
"In a small town, or in a rural area, this machine helps you be profitable and competitive," adds Lewis. "You can do your shearing and baling all in one place and don’t have to do any extra handling of material."
Because of the shear-baler combina-tion, fewer workers are needed to operate the machine. Maintenance is also a snap, according to Lewis. "All we do is oil and grease it," he says. "And that is important if you are a small yard because you can’t afford to have maintenance people on payroll. Why spend more than a million dollars on separate pieces of equipment when you can have one of these for far less money?"
Most of Lewis’ bales go to steel mills, but he also makes smaller bales called "slabs" for foundries.
Another processor who now sells to foundries with the help of his shear-baler is Ken Kohart, owner of Kohart’s Surplus & Salvage, Paulding, Ohio. Kohart has had his shear-baler for one year and says he has already seen "tremendous" results.
"If I knew of what value this piece of equipment was going to be to me, I would have bought one sooner," says Kohart. "I have already seen an incredible return on my initial investment."
Kohart makes #1 and #2 bales for mills and foundries, but says it has been his increase in foundry business that has really helped. "With the shear-baler we are able to make the special grades for the foundries that they want and package it for them," he says. "The foundries are nearby and pay a higher price for the grades that we are now able to supply."
The capacity of Kohart’s shear-baler has been averaging about 40 to 60 tons a day. Overall, the yard’s output is about 3,000 tons a month. Because of the shear-baler, Kohart’s ton-per-person rate has increased considerably.
Another processor, Jay Lamb, operations manager of Swenson Metal Inc., Spanish Fork, Utah, also praises the shear-baler. The company installed one in June.
"It has definitely made us more competitive in the tin and light iron areas," says Lamb. "It has reduced our price per ton preparatory costs."
Swenson Metal, like the other yards with shear-balers, categorizes itself as a small-to-medium size yard, processing about 100 tons a day of various ferrous and nonferrous metals.
A HOT SELL AHEAD?
As with any major equipment purchase, processors should first review their needs and their customers’ needs before buying a shear-baler. Study equipment and service contracts and maintenance histories from as many suppliers as possible. And finally, get references from other processors who already have the equipment before making a final decision.
Expect shear-balers to be a hot sell in the near-term future, says Langland, simply because of the reduced manpower requirements and the faster return on a processor’s investment.
"You can spend close to one million dollars for a shear and a baler, if bought separately, but only half that for a shear-baler combination," he says. "You don’t have to be an economist to figure that one out."
The author is managing editor of Recycling Today.
Get curated news on YOUR industry.
Enter your email to receive our newsletters.
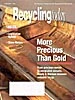
Explore the February 1996 Issue
Check out more from this issue and find your next story to read.
Latest from Recycling Today
- Recycled steel price crosses $500 per ton threshold
- Smithers report looks at PCR plastic’s near-term prospects
- Plastics association quantifies US-EU trade dispute impacts
- Nucor expects slimmer profits in early 2025
- CP Group announces new senior vice president
- APR publishes Design Guide in French
- AmSty recorded first sales of PolyRenew Styrene in 2024
- PRE says EU’s plastic recycling industry at a breaking point