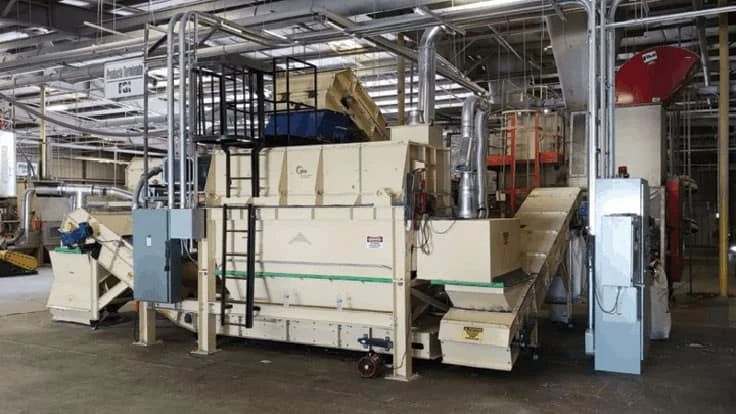
Allegheny Manufacturing
_fmt.png)
At Allegheny Manufacturing, we have been committed to providing application engineering, manufacturing, project management services and turnkey solutions for a wide range of bulk handling and size-reduction tasks in the recycling, mining and cement industries. While our company is relatively young, our employees have more than 25 years of experience working in equipment design and manufacturing in the aggregates sector.
Allegheny Manufacturing’s success lies not just in our technical expertise but also in the responsiveness of our staff. When you work with us, you’ll find that Allegheny Manufacturing’s design solutions, robust equipment and drive for excellence are unmatched among others in the industry. Allegheny Manufacturing’s team of dedicated professionals is detail oriented. Our engineering and production team collaborate on equipment, ensuring the best outcome for our clients. We earn our customers’ trust by educating them about their recycling options, even if they don’t directly benefit us.
Our material handling solutions include vibratory feeders, conveyors and rotary screens, while our size-reduction equipment includes our Bison hammer mills and Rotary Impact Separators. Through the combination of our original equipment manufacturer (OEM) partnerships and in-house proprietary designs, Allegheny Manufacturing offers the best equipment solutions for the most challenging size-reduction and bulk handling applications.
Our strengths
Our primary strength is being able to provide turnkey solutions and support to deliver systems that meet our customers’ requirements while using innovative equipment that also is economical to purchase and maintain. In many cases, we’re creating new products specifically to solve our customers’ problems. Custom solutions are what set Allegheny Manufacturing apart from traditional suppliers to the recycling industry.
_fmt.png)
Our customers include roofing shingle manufacturers, carpet recyclers, blown insulation manufacturers and plastics recyclers. When we’re approached with a new opportunity, our team goes to great lengths to produce complete recycling systems that make economic and environmental impacts.
We help with process design, providing process flow sheets and general arrangement, or GA, layouts. Engineering, fabrication, assembly, in-house logistics and surface preparation are all just a part of what we can offer our clients.
Down to size
Our Bison line of hammer mills and grinders are ruggedly constructed to provide our customers with years of low-cost production and are suitable for many applications. They can be used as standalone units or combined with the innovative Rotary Impact Separator machines for the ultimate in processing versatility.
Our hammer mill line includes the Bison (B) Series standard hammer mills for abrasive and coarse grinding applications; the Bison (F) Series fine grinding hammer mills for nonabrasive materials, such as pulp, wood, grains, minerals and fibers; the Bison (I) Series impact crushers, which are heavy-duty, smaller size units with big impactor features; and the Bison (R) Series heavy-duty recycling hammer mills, featuring our largest and heaviest hammers and multiple rotor options.
Allegheny Manufacturing focuses on product and process development using our customers’ desired applications and materials. We offer sample testing at our facility for our customers and provide detailed process analysis and solutions for difficult applications. This helps our clients know what type of mill to select to achieve the desired particle size for their applications.
Technological advancements
We’re committed to delivering new recycling technology like our Rotary Impact Separator. We have partnered with Broadview Group International LLC (BGI) on its Rotary Impact Separator technology. This patented system is revolutionizing the material reduction and separation industries by combining both these operations in a single machine for mechanical disassembly and separation in one unit. The process is strictly mechanical, requiring no heat, water or chemicals. The Rotary Impact Separator also offers low operating costs thanks to its rugged design and use of abrasion-resistant wear parts.
It was originally designed for disassembling carpet into its primary components. Carpet is a difficult product to deconstruct, but our unique technology separates the face fiber, backing fiber and calcium carbonate from the backing material. This unique processing technology keeps the various plastics and fillers out of landfills, allowing them to be reused to manufacture roofing shingles or in road construction and many more applications.
Since its inception, the Rotary Impact Separator has excelled in processing other materials, such as artificial turf, fiber, commingled paper and plastic and shingles, to name a few.
For example, this system has been able to successfully separate commingled paper from plastic to make cellulose insulation for a company. The task of separating and recovering the cellulose-based fibers from mixed paper is a tricky process. The technology begins by taking a contaminated mixed paper and mechanically beating the material with a specialized implement, which breaks up the more friable paper components while leaving the durable plastic pieces intact. The cellulose fibers transfer through the screen on the unit, while the plastic pieces remain on top of the screen, resulting in easy recovery.
For many companies, the Rotary Impact Separator is the key to transforming problem materials into resources. It dramatically reduces the personnel needed to hand sort material while also allowing companies to procure lower quality infeed materials at reduced costs.
As BGI's partner on this RIS technology, Allegheny Manufacturing is the sole manufacturer of this device. Our team is always up for a challenge and wants to help you convert a disposal problem into a resource.
From initial concept to installation to ongoing maintenance, Allegheny Manufacturing wants to be your single source for your process equipment needs. Contact us today to learn how we can help you succeed.
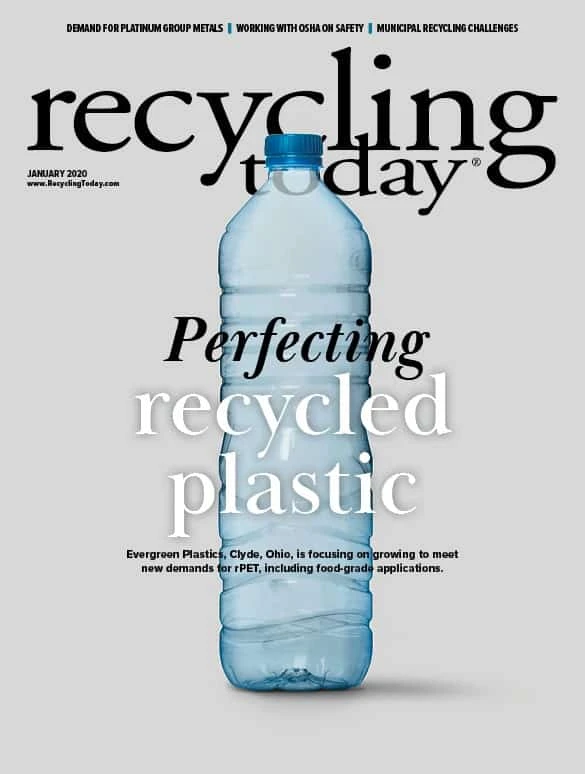
Explore the January 2020 Issue
Check out more from this issue and find your next story to read.
Latest from Recycling Today
- Aqua Metals secures $1.5M loan, reports operational strides
- AF&PA urges veto of NY bill
- Aluminum Association includes recycling among 2025 policy priorities
- AISI applauds waterways spending bill
- Lux Research questions hydrogen’s transportation role
- Sonoco selling thermoformed, flexible packaging business to Toppan for $1.8B
- ReMA offers Superfund informational reports
- Hyster-Yale commits to US production