
When San Francisco-based Brightmark LLC was looking for shredding equipment to use in its feedstock preparation system at its Ashley, Indiana, plant, the company prioritized consistency of particle size at the throughput rate required for commercial operation. Its turnkey system provides that consistency, despite variable feedstock, as well as redundancy, says Mike Dungan, the company’s feedstock development director.
As of early 2021, the company’s $260 million “plastics renewal facility” in Ashley is ramping up operations. The facility will recycle 100,000 tons of mixed plastics annually into ultra-low-sulfur diesel, naphtha and wax using a form of pyrolysis invented by RES Polyflow, which Brightmark acquired in late 2018.
Unlike similar technology, Brightmark’s technology can accommodate up to 3 percent polyvinyl chloride (PVC) by weight in its mixed plastics feedstock.
Before the mixed plastics can head to Brightmark’s plastic conversion units, they must be processed by the company’s feedstock preparation system, which was supplied by Vecoplan LLC, Archdale, North Carolina.
Mixed plastics bales that enter Brightmark’s Indiana facility are dewired and audited, with the baling wire and the obvious contaminants removed while the material is on the tipping floor, Dungan says. The material is blended and loaded onto a conveyor, where sorters further remove obvious contaminants by hand. The material then passes through optical and magnetic sorting technologies. At this point, the mixed plastics encounter the first of two Vecoplan shredders.
Dungan says the VAZ 2000 MFTV preshredder achieves a homogenous particle size before magnetic separation is employed for a second time.
After the metals liberated by the preshredder are removed, the plastics are fed to the second shredder, a Vecoplan VEZ 2500T, where they are reduced to particles less than 2 inches in size.
Additional system components include an optical sorter to identify and remove PVC and drying, pelletizing and material handling equipment that Vecoplan integrated. The system is rated for 12 tons per hour and can produce up to 280 tons in a 24-hour period.
Dungan says the systems’ fluidized bed dryer removes excess moisture from the plastics before a pelletizing system reduces the bulk density of the material. “Drying is the final step before we pelletize,” he says. “High moisture material is run through there,” he says of the fluidized bed dryer, “and we can turn the heat up or down based on the condition of the material.”
Brightmark began shopping for the feedstock preparation system almost six years ago. The company issued a request for proposals but received few offers that proposed turnkey solutions, Dungan says. Brightmark tested equipment from four shredder manufacturers, running material in a series of trial shredding campaigns. The company assessed the machines’ performance, ease of operability, construction and maintenance.
“The turnkey aspect of the system was the most appealing, but it was supported by good equipment,” Dungan says.
While Brightmark is still commissioning the equipment, installation was substantially completed as of the start of the year. The system will be tasked with creating the final specification for the pellets that will be used in Brightmark’s PCUs, including “size, shape, bulk density and moisture level,” Dungan says, from an ever-changing stream of incoming material that includes mixed plastics from material recovery facilities as well as postindustrial plastics, plastics from electronic scrap, car seats and boat wrap.
He says the shredders in the feedstock preparation system are broken into two lines to create redundancy. “In the event one machine failed completely, we’d still be able to operate at 50 percent capacity on the other line.”
Brightmark can “turn up” the system following planned downtime to produce more pellets during a shift to “catch up quickly,” he adds.
The feedstock preparation system’s shredders play a key role in the efficiency of the overall process.
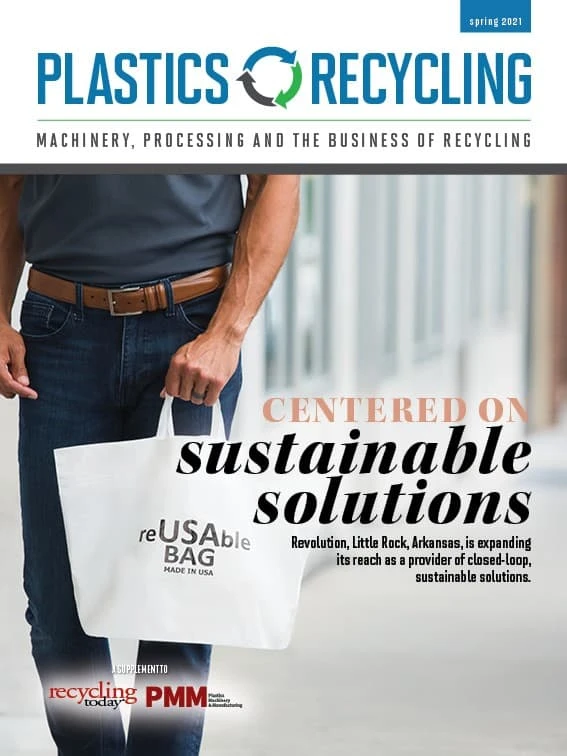
Explore the Spring 2021 Plastics Recycling Issue
Check out more from this issue and find your next story to read.
Latest from Recycling Today
- Aqua Metals secures $1.5M loan, reports operational strides
- AF&PA urges veto of NY bill
- Aluminum Association includes recycling among 2025 policy priorities
- AISI applauds waterways spending bill
- Lux Research questions hydrogen’s transportation role
- Sonoco selling thermoformed, flexible packaging business to Toppan for $1.8B
- ReMA offers Superfund informational reports
- Hyster-Yale commits to US production