Millions of pounds of turnings are generated every year in the production of wrought and cast metal parts. Although improvements in casting and forging technologies (such as the adoption of “near net shape” methods) have reduced the ratio of turning scrap to starting material, the tonnage is still huge and represents a significant portion of the scrap stream.
The recycling of turnings presents unique challenges for dealers and processors. In both instances, quality is the main factor in determining the buying and selling price. Thus, achieving and measuring the quality of turnings needs to be determined as accurately as possible to maximize profits.
COSTLY ENDEAVOR
There is no question that the costs associated with moving turnings from the lathe to the furnace are higher than the costs of taking solid scrap on the same journey.
Turnings are usually purchased at a discount from the solids price. The rationale behind this is that there will be a moisture component with turnings coming from an operation that used coolant. The percentage of moisture in a load of turnings is a function of several variables.
With the introduction of near net shape casting and forging techniques, turnings have gotten thinner. This results in more surface area per pound and, consequently, the ability for the turnings to hold more moisture. The amount of moisture is also dependent on how much rain or snow the turnings have been exposed to before reaching the processer. When buying turnings, moisture must be determined accurately, or the buyer will be paying alloy prices for water.
But moisture is only part of the story. Often, nonmetallic materials and trash are included in a turnings shipment. The cost of removing and disposing of this material must be considered in the settlement price. Usually alloy solids are inter-mixed with the turnings. Processers often look at these solids as a bonus, as they would normally pay a higher price for solids than for turnings.
What they are not considering is the labor cost associated with removing the solids before crushing as well as the cost of replacing crusher grates should a few pieces get past the solids pickers. The high square footage required for processing turnings, the need to capture and dispose of water runoff and the cost of the necessary analytical and processing equipment can quickly eat into the margin between the buying and selling price.
The good news is that careful analysis and planning can control these costs. The use of existing equipment and personnel can have a significant impact on per-pound costs. The careful layout of a facility will minimize handling and also hold down costs. Most importantly, the use of a comprehensive blending program can allow for the absolute maximum profitability in the utilization of an existing inventory.
Properly configured, a blending program can aid in defining the desirability of various materials and indicate pricing parameters for those materials. All of this profitability from a blending program, however, depends on an accurate knowledge of the chemistry of the blending materials. This brings us back to the statement in the first paragraph that knowing the quality (chemistry) of the turnings being bought and sold is the key to profitability.
An accurate understanding of the quality will allow the blending and sale of increasing volumes as melters experience and confirm the consistency of the product. This will result in a reduced operating cost per pound and allow the blending program to do its magic on the material costs.
ACQUIRING SKILLS
The challenge starts at the point of production. Skilled machinists will be focused on the value and precision of the parts they are producing. The scrap turnings they are creating are an inconvenience, and in many instances considered to be “trash.” This can result in little concern for scrap segregation at the point of origin and create contamination issues that diminish the value of the turnings.
Arguably, the most important effort a buyer of scrap turnings can make is to interact closely with the supplier. This interaction needs to be both a learning and a teaching experience. First, a buyer must learn about the suppliers’ products and the alloys used. This information will aid in the second part, the teaching.
As stated above, a machine operator may have little regard for the scrap turnings being generated. Relative to the parts being made, the scrap is of little value and it might be handled in that way. It is very beneficial to both the generator and the buyer to have the operators made aware of the value of the scrap and of the importance of not cross-contaminating alloys.
Until a company has a history with a supplier that shows it has an effective scrap management program, it will be necessary to thoroughly test all inbound shipments for contamination. The first step in testing is the same regardless of whether the turnings will be accumulated by alloy for sale to a processer or if the testing is to be performed prior to crushing by a processer.
The material must be spread out and visually inspected for obvious nonmetallic contamination. This contamination can be in the form of wood, trash, plastic and even spent coolant. (A witness once told of seeing a scrap generator pour two drums of spent coolant onto a truck of turnings to avoid the coolant disposal costs).
The next step is to examine the material, looking for visible differences in the metal. A color difference would be the most obvious indication of alloy contamination, though this also can be caused by variations in the machining process and may not be a problem. Significantly different cuts indicated by the thickness and shape of the turnings could point to a different alloy and should also be tested. The testing can be done with a magnet, a torch and acid or preferably with a handheld alloy analyzer.
After material arriving from the generator is examined and tested, it is moved to an accumulation pile if it is in the hands of a dealer or advanced to a crusher if it is in the hands of a processor. Turnings must be crushed to be sold to a melter. Although a melter may charge small quantities of uncrushed home scrap into its furnace, melters are generally restricted by density considerations to buying only crushed turnings.
The most suitable sample that can be collected on a shipment of turnings is collected at the crusher. This is because all of the material will pass through the same location—the discharge chute of the crusher—and will be of a similar particle size.
Professionals use several techniques to collect the crushed sample. They range from having a worker occasionally grab material from the discharge to locating a pipe in the stream to divert some of the material to a collection point. The argument can be made that most of these methods have a built-in bias.
By far, the best sample will be taken by an automated device that samples the entire cross section of the turnings stream on a fixed interval, with the only human interaction being the setting of the interval. The gross sample collected at the crusher can be reduced to a workable size by “quartering” using a shovel or a commercially available sample splitter called a “riffle.”
At this point, it is recommended that the sample be consolidated and homogenized by melting the sample into a small ingot or button. If all of the sample collection steps are performed correctly, the melted sample should have a chemistry that accurately reflects the chemistry of the shipment.
The chemistry of the melted sample must be known as accurately as possible. The recommended methods of analysis are with an X-ray or emission spectrometer using well-characterized standards. Small amounts of tramp elements can go undetected if the sample is tested with an instrument designed to be primarily an alloy sorter, since some of these tools will not register certain types of contaminating elements. The worst-case scenarios involves tramp elements making it through at levels that can destroy a heat in the melter’s furnace.
WORTH THE EFFORT
Although the costs associated with producing a scrap turnings product are high, this can still be a very profitable business.
That profitability depends on careful attention to facility layout, equipment and personal utilization and—when those factors are optimized—on volume.
The volume is driven by sales, which has a direct relationship to the quality of the product produced. The more consistent the product, the more desirable it will be to the melter.
The required consistency can only be achieved through an accurate characterization of the incoming materials using carefully executed testing and sampling techniques.
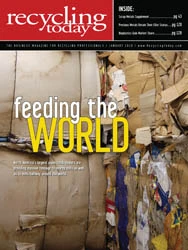
Explore the January 2010 Issue
Check out more from this issue and find your next story to read.
Latest from Recycling Today
- Nucor receives West Virginia funding assist
- Ferrous market ends 2024 in familiar rut
- Aqua Metals secures $1.5M loan, reports operational strides
- AF&PA urges veto of NY bill
- Aluminum Association includes recycling among 2025 policy priorities
- AISI applauds waterways spending bill
- Lux Research questions hydrogen’s transportation role
- Sonoco selling thermoformed, flexible packaging business to Toppan for $1.8B