
As material recovery facilities (MRFs) increasingly employ technology such as optical and robotic sorters and artificial intelligence (AI), more data on day-to-day operations has become available.
But, with so much data available, it can be difficult to determine which is the most actionable.
According to a panel of recycling industry veterans assembled at the MRF Operations Forum last October, sales pitches from equipment manufacturers have included bold performance claims, but the need for useful data remains.
“[Data collection] is something we’re more and more involved with,” said Jeff Nella, area recycling director – U.S., for Vaughan, Ontario-based GFL Environmental Inc. and moderator for the Advanced Opticals and MRF Data session. “We’re constantly collecting more and more MRF data, and we’re inundated with all types of manufacturers who are making all different types of claims about what information is available, what data they can provide to us and what we should be doing with it.”
Volker Rehrmann, executive vice president and head of Germany-based Tomra Recycling, a division of Norway-based equipment manufacturer Tomra Systems ASA, added that determining the valuable data can be difficult for both manufacturers and operators.
“What is the value of just collecting data and you can’t make any use out of it?” he asked. “You cannot improve your operations by using it. And that’s the challenge of where we’re at right now. … Collecting a lot of data is easy. Making business use out of that is a tough road.”
The right place
The panel, which included Riel Johnson, vice president of resource recovery at City of Industry, California-based Athens Services, and Ron Grinold, Great Lakes area manager at Phoenix-based Republic Services, agreed the placement of sorting technology within a MRF is important for data collection.
Nella, whose company runs more than 30 MRFs in North America, said optical units found a home on the container line, then migrated to fiber lines.
Grinold said there is room for improvement in terms of where opticals typically are located and suggested positioning an additional optical behind a first one to serve as quality control.
“I think there’s still room for advancement,” he said. “Layering the typical optical with artificial intelligence on top of that, that’s coming, and that’s going to be the next big push.”
Johnson has seen benefits to placing optical units on the last-chance line. “We always want to know what’s going into our trash,” he said. “If we’re losing good material, we want to be able to capture that data and, over time, [have] historical data. Right now, without the data collection, we have to do hand sorts and open up the trash compactors. I think that’s the best opportunity.”
Once data have been collected, the panelists agreed it is important to control and own that information rather than what Nella described as “leasing back that information from a vendor.”
“Also, I’m not a big fan of subscription fees,” Grinold said. “I think if you buy a machine, it should come with the AI already in it, the neural network already loaded up. I don’t think there are that many changes in the containers. … Maybe you pay for an upgrade, and you pay that one fee at one time. … But I’m not a fan of a continual needle in my arm to get my neural network to me.”
Athens Services’ Johnson compared optical sorters with smartphones, saying, “Every year there’s a new one coming out with a new technology. Does that require a subscription fee to be a part of that, or is that [an upgrade] you can choose to purchase?”
Some data collected in MRFs have been used to improve operations with the help of the supplier. Grinold, who oversees multiple MRFs across Michigan, Ohio and Indiana, said while upgrading opticals at one MRF, AI was used to provide feedback on picks that Republic could take to its system provider to make equipment adjustments.
“[We could see] the number of picks that were going by, like, for example, how many PET [polyethylene terephthalate] objects were going by,” he said. “You didn’t have to stand there with a clicker; you didn’t have to stand there and take samples. The AI was doing it live, and it was a great system.… What came out of that, too, though, is it set a bar for acceptability as well.”
Nella added that lots of high-tech information is moving back and forth, but many MRFs have older, standard optical sorters that measure square inches or square centimeters and provide feedback on what is on the belt. With newer systems, Nella asked, “Is that data that’s now just packaged in a little bit sexier format than what we’ve always had?”
Johnson, whose company operates several MRFs in the Los Angeles area, said it comes down to an operator’s trust in the data received. He and Nella suggested equipment manufacturers help manage operational controls for MRF systems to better manage the data.
“Quite frankly, none of us are scientists,” Nella said. “Is this stuff that we need to get off our plate and push back to some of our system providers, who are doing our operational controls for our systems?”
Grinold said, “By the time you’re getting your data at the end of the day, it’s too late. The day’s gone. If it’s live and it’s changing your screen angles, for example, or it’s changing the speed of your infeeds, that’s real stuff right there. And it’s immediate. As we know, each day’s a little different, and each load’s a little different, and to be able to not rely on an operator to crawl around the railing and say, ‘Hey, speed up this and slow down that,’ and let the artificial intelligence do that, that makes a lot of sense.”

Reality for robots
When it comes to robotic sorters, Nella recalled about five years ago the technology was considered a fad, but the units have since found a place on container and residual lines and continue to evolve, though their pick rates remain slower than optical sorters. “It’s something we use on the very last belt before the compactor, but upstream we have to go with a faster recovery technology.”
“Realistically, the robotic arms, when it comes to picks per minute, you can’t compete with an optic,” Grinold added. “The struggle, though, is that volume is king. That’s where you make your money. The last thing we want to do is slow down the system so the robotic arm can perform better. How do we get the robotic arm to meet our current standards?”
“We feel that, if anything, robotic arms are decreasing,” Nella continued. “In just the last three years, if we look at a MRF design, it may have five, six, seven robot stations in it. I can tell you, some of the newest MRFs that are performing as well as anything I’ve seen, they have zero robotic arms. We are looking at removing robotic arms and adding optical sorters, doing more with the flexibility of optical sorters with two and three tracks.”
The panelists agreed AI linked to robotics could be used to understand what is on the belts and make decisions based on that data rather than rely on them for capture. Still, Grinold said robotics could perform well on last-chance lines in place of human pickers as hiring and retention have become difficult.
Unpacking the black box
As an equipment developer, Rehrmann compared MRF operations to a black box that Tomra and other companies are trying to solve through the data their equipment collects.
In the future, he expressed hope that evolving sorting technology could allow MRFs to always function at a maximum level. “This is what drives us,” he said.
“Compared to other industries, we’re far behind when it comes to those types of systems where you have full control of your production process, making sure when there’s the smallest deviation somewhere in this black box, you notice it, and it would ideally correct itself automatically and, if not, you would immediately be notified ... and [could] be sure your plant always runs as close as possible to optimum level. I think that’s the highest level we as a supplier can give you.”
Rehrmann said data is the answer to improving technology, and more inexpensive sensors installed around a MRF could lead to breakthroughs. He highlighted Tomra Insight, a cloud-based digital solution that provides daily reports on a sorters’ performance as well as alerts when something goes wrong.
“In the future, I think we’ll get closer to using this data, making the data more intelligent,” he said. “Just data alone has no value. Someone needs to interpret this data into action for you. And this is what we’re working on.”
Get curated news on YOUR industry.
Enter your email to receive our newsletters.
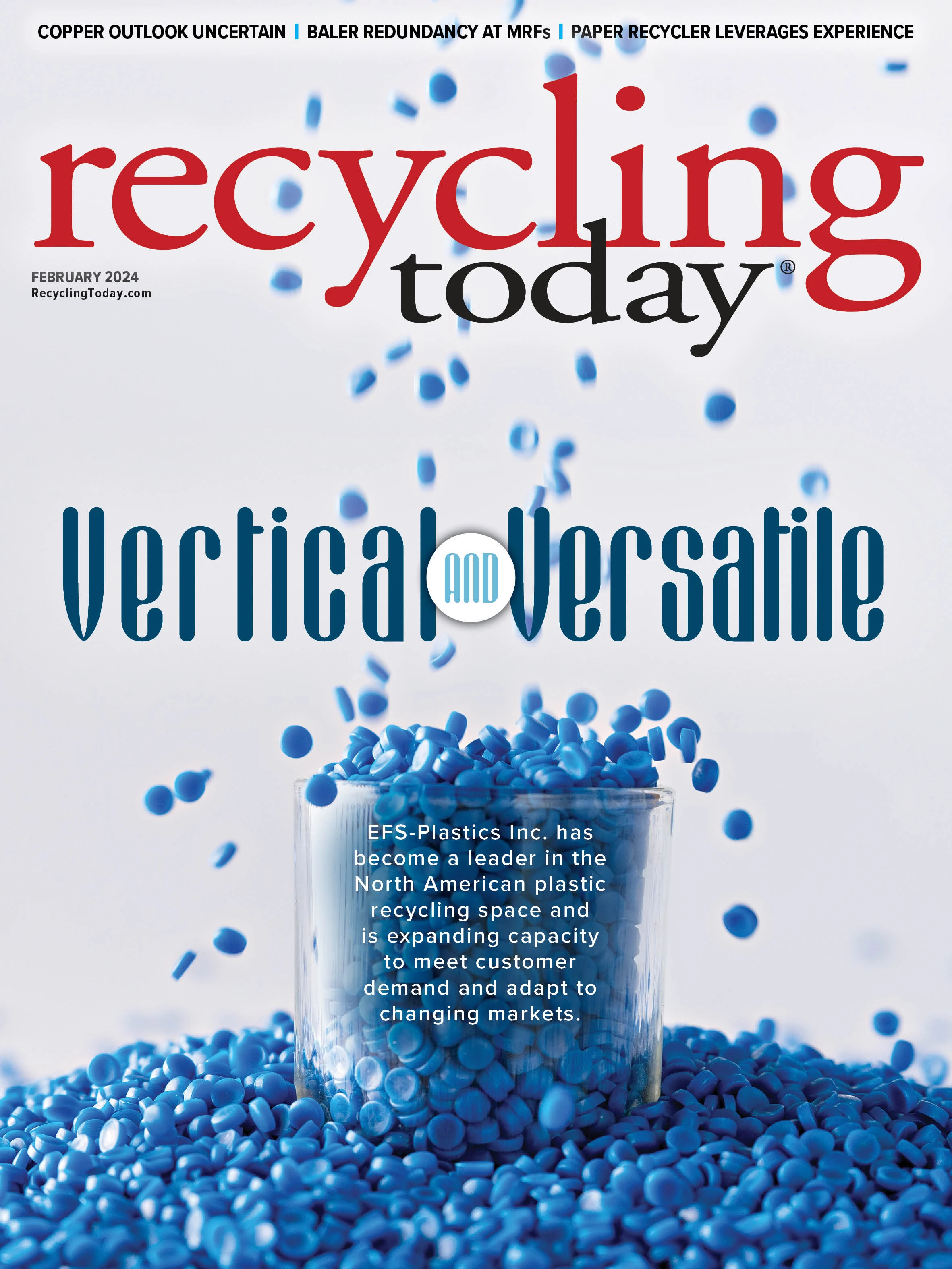
Explore the February 2024 Issue
Check out more from this issue and find your next story to read.
Latest from Recycling Today
- Toppoint Holdings expands chassis fleet
- Lego creates miniature tire recycling market
- Lux Research webinar examines chemical recycling timetables
- Plastics producer tracks pulse of wire recycling market
- Republic Services, Blue Polymers open Indianapolis recycling complex
- Altilium produces EV battery cells using recycled materials
- Brightmark enters subsidiaries of Indiana recycling facility into Chapter 11
- Freepoint Eco-Systems receives $50M loan for plastics recycling facility