

Sweed wants your scrap samples
Gold Hill, OR—Sweed has built a new state-of-the-art nonferrous separation system for their testing facility in Oregon, which the company says is “an integral part of Sweed’s continued growth within the recycling industry.”
The new test system provides three functions for Sweed’s long-term goals. “First, it offers a functional, hands-on setting to test materials to determine the most effective solution and ensure end-product quality. It also serves as a teaching tool for training prospective and existing customers,” says Chris Salyer, Engineering Director. Christopher Simon, Sweed’s recycling system sales representative, adds, “The new system also allows us to utilize different flow diagrams to mimic what will work best for the customer.”
Our Facility
The testing facility comprises a myriad of Sweed equipment, including a PCR1048 single-shaft shredder, an SG1826 granulator, the TM1815 turbo mill and two 3G air tables.
Auxiliaries complementing the processors include a steel magnetic cross belt on the first conveyor incline into the granulator, three sifting tables to sort material by size and a HISC separator at the end of the first air table to ensure the purity of the material. Additional bypasses are included to accommodate an array of material types and processing objectives.
Creating Custom Solutions
Recyclers can ship their scrap material to Sweed’s test facility to be processed. Based on engineering analysis and results, Sweed will recommend the most suitable system configuration or retrofit for the customer’s sorting requirements and goals. “Sweed’s new test system provides much flexibility. With the bypasses we’ve incorporated into the system, we can process scrap through the whole system or just one processor if customers want to isolate their material through one component,” Salyer says.
Sweed is calling on recyclers to send their material for processing and evaluation. “We are excited to launch the new test system. It allows us to continue providing new separation solutions for tough scrap challenges. Wire and cable are our specialties; however, our systems also successfully process ASR, ACR, auto wire harness, transformer sheeting and coils and even lithium-ion batteries, recovering the steel, copper, aluminum and black mass containing valuable cobalt,” Simon says.
Sweed wants your scrap samples! Visit bit.ly/testmyscrap.
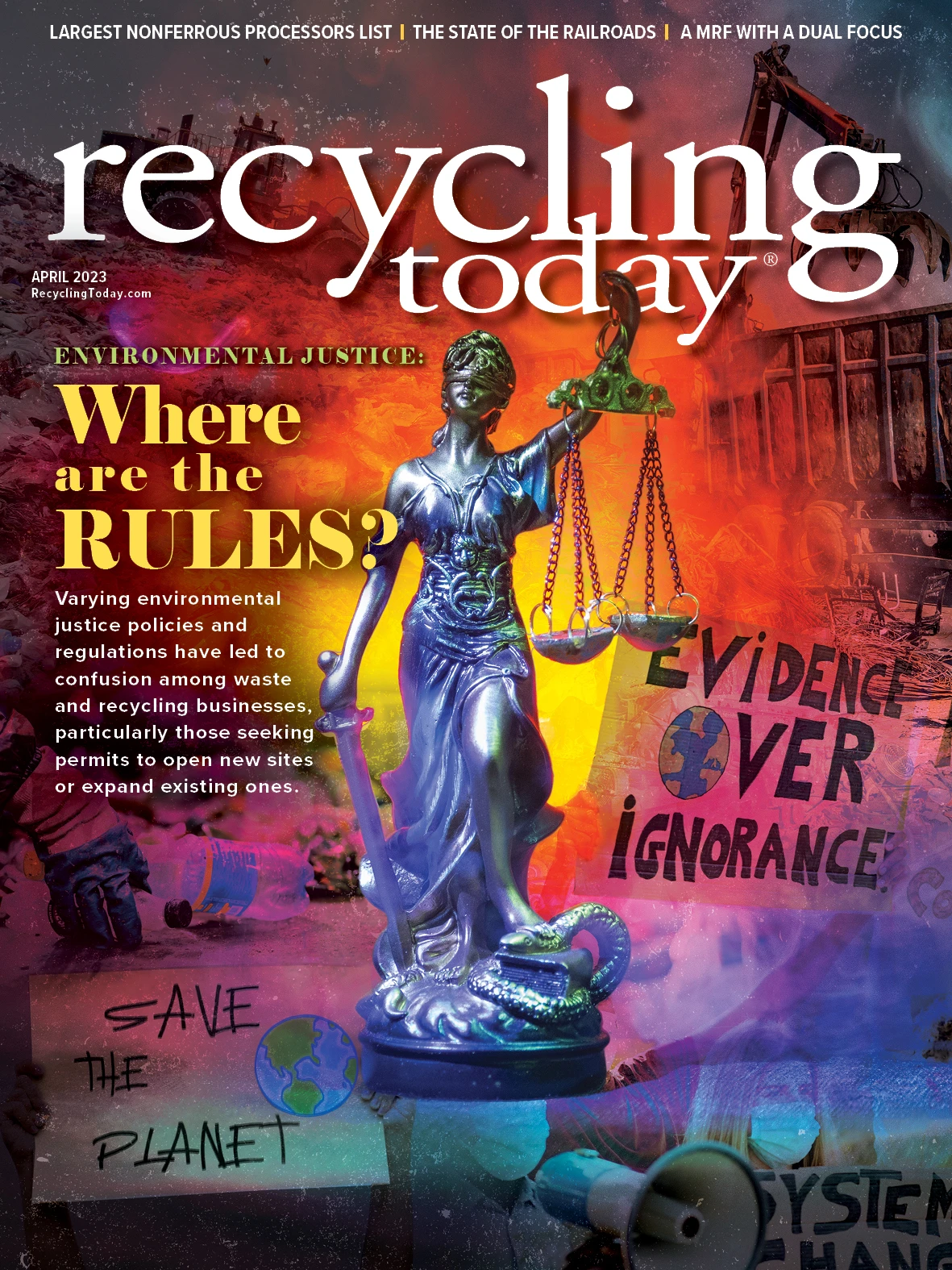
Explore the April 2023 Issue
Check out more from this issue and find your next story to read.