A
s a kid, I worked in my father’s scrap yard without picturing that one day I’d run a similar business. At the time, I certainly wasn’t aware of the number of regulations that would eventually control them, nor did I imagine that I’d be responsible for meeting these regulations or that the runoff from the facility would be regularly tested to confirm compliance.My brothers and I run Mazza Demolition, Transfer, Recycling and Scrap Metal in Tinton Falls, N.J. The company was founded by our father in 1964 and currently employs 50 people. Today we process or recycle demolition debris, scrap metal, tires, concrete, yard debris and other recyclable materials.
One of the toughest challenges that we face is controlling runoff from oily scrap metal and oil that drips from trucks and heavy equipment in our yard, which could pose a serious threat to the environment around us. Contaminated stormwater running off our facility has the potential to mix with and compromise groundwater.
Unlike the scrap yards of the past, we know the environmental damage that can be caused by polluted runoff and we do our best to minimize it.
CHANGING REQUIREMENTS. Keeping current with all the New Jersey Department of Environmental Protection (NJDEP) regulations is a challenge. The regulations cover everything from litter to stormwater runoff, making it tough for any recycling operation to stay on top of every regulation, especially at a large facility like ours.
In 1980, we moved our operation from Long Branch, N.J., to 55 acres in a manufacturing area near Tinton Falls. This facility borders on a wetland that edges onto our property. At the time we moved, any water that flowed off our site met the NJDEP requirements. Later, however, the regulations became tighter.
The topography of our site and the nature of our business divide the facility roughly into three parts—one for recycling wood, concrete, mulch and other materials; another for recycling scrap metal; and a third for construction and demolition material transfer.
The transfer station is a 46,000-square-foot building at the center of our site. Here our customers bring concrete, scrap metal, tires, brush, mulch, tree stumps and construction and demolition debris into our facility. Our demolition division also brings in construction materials, and our employees separate recyclables from materials for disposal.
A few years ago, like all recycling operations in New Jersey, our business was required to meet a new environmental regulation called the New Jersey Pollution Discharge Elimination System code (NJAC 7:14A), which falls under the state Solid Waste Management Act. The statute includes regulations for the remediation of all contaminated sites. This made it necessary to find a way to control the stormwater running off our property.
Because the storm runoff drains into a wetland, the scrap metal operation created the biggest challenge in meeting the new environmental regulations. Although we try to make sure that all the metal on site is clean and oil free, minor oil leaks from our customers’ trucks and our equipment is inevitable. We knew that even slight amounts of oil might pass into the wetlands through runoff and, therefore, sought a way to prevent this.
In 2001, we took steps to comply with the NJDEP regulations. We began working with Schoor DePalma Inc., a New Jersey engineering firm with more than 30 years experience in storm-
water treatment and conveyance systems. The Schoor DePalma engineers helped us design a stormwater system to meet the stringent NJDEP requirements.
Examining our site, Schoor DePalma engineers found it unique because of the variety of recyclables and the relative flatness of the property. They also confirmed that our scrap metal recycling fell under federal regulations, and that the variety of materials at the facility put us in a "position to pollute," as it’s called in some regulations. Both meant that we needed to put a stormwater system in place.
ACHIEVING COMPLIANCE. To meet these and other regulations, as well as to reduce the site’s "potential to pollute," the engineers suggested that we install the Stormwater Management StormFilter, a StormGate Separator and a detention pond. They also recommended that we use catch basins to collect some of the runoff. Together, this system would address potential environmental concerns about runoff containing debris, dirt, metals, oil and grease.
Working with Schoor DePalma engineers and Stormwater Management Inc. of Portland, Ore., in May 2002, we settled on this stormwater system design. The StormGate Separator was designed to treat runoff from the equipment maintenance area. Treated runoff from the maintenance area and runoff from other catch basins were piped to the detention pond. Overflow from the pond was piped into the StormFilter that discharges into the wetland.
We dug the detention pond and the holes for the StormGate Separator and StormFilter and sculpted the land to promote drainage. Then the engineering team dropped in the precast StormGate Separator and StormFilter vaults. The media-filled filter cartridges were placed in the StormFilter vault last.
The Stormwater Management systems were relatively easy to install, and the team completed all the work in about a week. The system installation didn’t even interrupt our normal operations.
The team installed the 6-foot-by-12-foot precast StormGate Separator in the ground behind our maintenance and office buildings near an equipment maintenance pad. There it can catch oil dripping from our equipment during maintenance and oily waste from the scrap processing area. During a rainstorm, the StormGate Separator divides oil and water, as well as some dirt and grit.
By doing some minimal grading, a few swales and ground contours were created to help direct water from the rest of the site to the holding pond. The water that flows through the separator joins runoff from the rest of the site and flows into a holding pond where more pollutants settle out.
Downstream from the pond, we buried an 8-foot-by-18-foot precast StormFilter vault that holds 30 cartridges for removing pollutants from the pond overflow. During the heaviest rainfall, the pond helps control the amount of runoff going into the Storm-
Filter. When the pond floods, the runoff drains through a buried pipe into the StormFilter system for further cleansing of pollutants. Eventually, the water from the StormFilter discharges into the wetlands.
The engineers from Stormwater Management told us that this type of an approach to a stormwater management system is recognized as a best management practice by New Jersey, as well as by many other states. (The New Jersey Department of Environmental Protection has produced a manual on best management practices for stormwater management, which is available online at http://www.njstormwater.org/bmp_manual2.htm.)
IMPROVING WATER QUALITY. The StormGate Separator improves water quality by directing polluted, low-volume runoff into stormwater "cleaning" chambers while allowing heavy rainfall to bypass the chambers. The high-flow bypass in the StormGate Separator, along with a specially placed orifice, prevents flow from heavy downpours from washing any collected pollutants or oil out of the system.
The engineered contours on the site direct the runoff throughout the site to the holding pond. When the pond reaches its flood stage, it flows into the StormFilter.
The StormFilter cleans the runoff by passing it through a patented, passive-filtration system to remove pollutants to levels that meet stringent regulatory requirements, like the ones that New Jersey demands.
Each StormFilter cartridge contains CSF leaf media that filters runoff and holds contaminants, especially dirt particles and oil sheen. The media removes pollutants, like sediment, oil and grease, metals, nutrients and organic material, as well as trash and debris, before the runoff enters the wetlands.
This filtering system combined with the detention pond at our facility address any issues that we might have with stormwater pollutants. It’s reliable, easily installed and maintained and generally recognized by the recycling industry and state regulators as an extremely versatile stormwater best management practice.
MAINTAINING AND MONITORING. In its third year of operation, the StormFilter and StormGate Separator combination have provided our company with a simple and inexpensive method for meeting NJDEP stormwater permit requirements.
When we see that the water in the StormFilter is rising or that a build up of mud has caused the output flow to slow, usually about once a year, we know it’s time for maintenance.
This year we are planning to pave our parking lot and the incoming queuing area to the transfer station. This measure will further reduce the sediment and solids going into the catch basins and the build up of sediment in the detention pond.
Recently we conducted maintenance and replaced the CSF leaf media in the 30 cartridges in the StormFilter.
Because the media binds pollutants, it can be either recycled or taken to a landfill with no concern about contaminants entering the water table.
To document that we are meeting the New Jersey’s stormwater runoff requirements, we test the outflow every 90 days. Accutest Laboratories from Dayton, N.J., visits our facility to test the quality of the runoff discharging into the wetlands.
For three years, we’ve passed every quarterly sampling test.
Dominick Mazza is president of Mazza Demolition, Transfer, Recycling and Scrap Metal, a second generation company based in Tinton Falls, N.J.
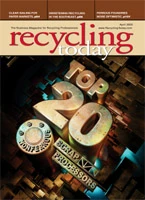
Explore the April 2005 Issue
Check out more from this issue and find your next story to read.
Latest from Recycling Today
- P+PB adds new board members
- BlueScope, BHP & Rio Tinto select site for electric smelting furnace pilot plant
- Magnomer joins Canada Plastics Pact
- Out of touch with reality
- Electra names new CFO
- WM of Pennsylvania awarded RNG vehicle funding
- Nucor receives West Virginia funding assist
- Ferrous market ends 2024 in familiar rut