So, what exactly happened to the boxcar? Does recovered fiber move by rail anymore? To borrow a familiar refrain, the reports of the death of scrap paper moving by boxcar are greatly exaggerated.
To be sure, the volume of rail shipments on Norfolk Southern (NS), one of two large eastern U.S. rail carriers, was down more than 20 percent year over year for 2009, reflecting both the industry’s decline as well as increased truck competition. However, scrap paper boxcar volume for the year was approximately 10,000 shipments, or about 100 trains’ worth. This figure excludes recovered fiber moving by intermodal container domestically or by ocean container to the ports for export.
U.S. railroads have a love-hate relationship with scrap paper. Profitability remains challenging, primarily in light of historical business models that lacked supply-chain management discipline. Excessive boxcar cycle times, damage to boxcar equipment by clamp truck operators and boxcars released dirty and unsuitable for subsequent paper loading are all the bane of efforts to render the business desirable. However, when managed properly, railroads can add significant value to the supply chain, increase market reach for recovered fiber grades and potentially generate a sufficient return for rail carriers.
NS is committed to boxcar movements of recovered fiber. The railroad believes that the market can be strategic in driving boxcar asset utilization and reducing empty miles from loaded movements of pulp and paper shipments.
BOXCAR VERSUS TRUCK
Just as trucks have increased in cubic carrying capacity over the years, so too have rail cars. Boxcars are long-lived assets—they are typically in service for 40 years—so there are still plenty of “old school” 70-ton cars around that are perfectly suitable for hauling paper and other products. The transition to larger boxcars will take place over time as the lower-capacity fleet is retired from service. The newest rail cars can carry 100 tons of lading and have 40 percent more capacity by volume than the last generation of boxcars and 80 percent more volume than a 53-foot truck trailer. These longer, taller boxcars give scrap paper shippers the ability to load more recovered fiber per car: Norfolk Southern has hauled scrap loads of dense bales in 60-foot high roof cars loaded in excess of 90 tons—the equivalent of more than four trucks, with the added benefit of lower carbon dioxide emissions.
Even so, bale size is another factor that needs to be considered when shipping by rail. Most recovered fiber boxcar loads cube out before they weigh out. Therefore, the dimensions and density of the recovered paper bales have a great bearing on how efficiently a boxcar is used.
NS has employed the use of load optimization software to model load plans for customers to maximize the lading weight in any size boxcar. This is important because as a general rule of thumb, the more product in a rail car, the less the effective price per ton, given that most rail pricing is done on a per-car basis.
Shippers recognize the output potential. Jonathan Sloan, president of Canusa-Hershman, with corporate offices in Baltimore and Branford, Conn., says, “Canusa-Hershman believes in the long-term viability of moving recovered fiber by rail. We’ve made it a priority that any new plants we site are rail served; three of our four facilities have rail.” He adds, “It allows us to reach more markets and improves plant efficiency being able to load significant volumes directly into cars and not having to wait for trucks to arrive.”
Investment in new, high-capacity boxcars is a $100,000-per-unit proposition, so maintaining fleet quality is important to keeping these cars in service handling paper and other products. In conjunction with CN Railway, NS developed the Certified Loader/Unloader program that provides shippers and receivers of recovered fiber a training regimen for the proper loading and unloading of boxcars. Once the training is completed, the facility receives a “Good Boxkeeping Seal of Approval” certification, which gives NS the confidence to supply premium boxcars to be used in recovered fiber service.
MAKING MARKETS
In 2010, Norfolk Southern is reinvigorating its “Bales on Rail” program to actively encourage boxcar shipments of recovered fiber. A simplified, state-to-state pricing matrix has been designed to make it easier to evaluate rail economics. Emphasis is being placed on shipments to paper mills that will reload inbound scrap loads with outbound linerboard, printing paper, newsprint or wood pulp.
The Norfolk Southern-served paper mill network is heavily concentrated in the Southeast. Paper shipments from the mills generally flow to the Midwest and Northeast, from which the boxcars often travel empty back toward their point of origination. Recognizing that most mills source recovered fiber within a certain radius that reflects relatively low local or regional freight costs, movements of scrap paper from the Northeast or Midwest back to the mills in the Southeast are generally limited to specialty grades. The new rate matrix provides for movements from anywhere on NS’s rail network to certain mill locations in the Southeast at effective rates of no more than $20 to $30 per ton.
Key to the success of boxcar movement is managing the inventory pipeline to ensure a steady flow of equipment consistent with a given destination’s ability to unload cars in a timely fashion. This can be accomplished using rail carriers’ suites of free e-commerce tools. Additionally, these Web-based applications allow customers to price shipments, order equipment, find transit times, submit shipping instructions, view invoices and make payments online. Visibility of shipments in real time is at the customer’s fingertips.
NS also is working with paper mills to provide incentives to reload equipment from inbound paper movements, whether from printers or box plants, even if the cars do not return to the same mill. For example, Norfolk Southern has worked to put together competitive interline rates with CN Railway from printers that NS serves, primarily in Pennsylvania and northern Virginia, to the paper mills in Canada that CN serves. Again, this is an effort to reduce the empty miles associated with the loaded paper movements originating in Canada.
CN’s Director of Marketing Andrew Fuller affirms CN’s commitment to moving recycled paper by rail. “Using rail cars to move recovered fiber is a logical solution for customer’s supply chain requirements, especially when they can be reloaded with outbound paperboard or paper,” Fuller says. “Shipping by rail makes strong economic sense, as it offers a transportation option that in many cases is already at the generator’s back door. The rail option provides customers with greater access to quality fiber sources and a consistent and environmentally friendly pipeline on wheels that can help optimize inventory management.”
NS also has targeted Mexico-destined shipments from Midwest and Northeast origins, as these scrap paper boxcars often will be reloaded south of the border with consumer goods, such as beer, sugar and tile, to return to the U.S. Collectively, these pricing actions allow recovered fiber buyers to expand their market reach beyond the traditional distances that scrap would otherwise travel.
Increased mill capacity and consumption in China, India and Indonesia are expected to drive continued growth in the demand for export fiber from the U.S. Finding a container in the interior of the country to load with scrap paper can be difficult, and this is where railroads can assist. For example, an exporter can load recovered fiber into a boxcar, which, when it reaches the port, is then cross-docked directly into ocean containers. NS has developed relationships with transloaders at East and Gulf Coast ports in an effort to facilitate this process.
EXPANDING MARKET REACH
Sponsored Content
Labor that Works
With 25 years of experience, Leadpoint delivers cost-effective workforce solutions tailored to your needs. We handle the recruiting, hiring, training, and onboarding to deliver stable, productive, and safety-focused teams. Our commitment to safety and quality ensures peace of mind with a reliable workforce that helps you achieve your goals.
Sponsored Content
Labor that Works
With 25 years of experience, Leadpoint delivers cost-effective workforce solutions tailored to your needs. We handle the recruiting, hiring, training, and onboarding to deliver stable, productive, and safety-focused teams. Our commitment to safety and quality ensures peace of mind with a reliable workforce that helps you achieve your goals.
Sponsored Content
Labor that Works
With 25 years of experience, Leadpoint delivers cost-effective workforce solutions tailored to your needs. We handle the recruiting, hiring, training, and onboarding to deliver stable, productive, and safety-focused teams. Our commitment to safety and quality ensures peace of mind with a reliable workforce that helps you achieve your goals.
Sponsored Content
Labor that Works
With 25 years of experience, Leadpoint delivers cost-effective workforce solutions tailored to your needs. We handle the recruiting, hiring, training, and onboarding to deliver stable, productive, and safety-focused teams. Our commitment to safety and quality ensures peace of mind with a reliable workforce that helps you achieve your goals.
Sponsored Content
Labor that Works
With 25 years of experience, Leadpoint delivers cost-effective workforce solutions tailored to your needs. We handle the recruiting, hiring, training, and onboarding to deliver stable, productive, and safety-focused teams. Our commitment to safety and quality ensures peace of mind with a reliable workforce that helps you achieve your goals.
While printers, box plants and material recovery facilities (MRFs) are common rail shipping points, additional efforts are being placed on developing transload options for non-rail served sources of fiber. For example, rail carriers often move paper products to warehouses for local or regional deliveries. These same trucks can pick up bales of fiber while making deliveries and consolidate scrap paper for reloading into rail cars.
The challenge for rail carriers to remain relevant to recovered fiber supply chains is to work with generators, brokers, buyers and receivers to change the long-standing paradigms associated with boxcar movements of scrap paper. Increasing percentages of contracted (versus spot-market) fiber sourcing, a disciplined approach to inventory pipeline management and attention to rail car quality will enable the industry to leverage the potentially significant value proposition that rail shipments can achieve. These benefits include expanded market reach, lower fiber supply-chain costs and reduced carbon dioxide emissions versus trucks and, for paper mills, lower overall supply-chain costs.
So, do railroads move recovered fiber in boxcars anymore? Absolutely, and they plan to greatly expand their role in the marketplace.
Get curated news on YOUR industry.
Enter your email to receive our newsletters.
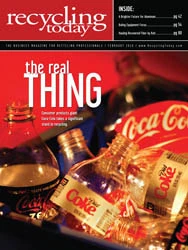
Explore the February 2010 Issue
Check out more from this issue and find your next story to read.
Latest from Recycling Today
- Green Cubes unveils forklift battery line
- Rebar association points to trade turmoil
- LumiCup offers single-use plastic alternative
- European project yields recycled-content ABS
- ICM to host colocated events in Shanghai
- Astera runs into NIMBY concerns in Colorado
- ReMA opposes European efforts seeking export restrictions for recyclables
- Fresh Perspective: Raj Bagaria