What to do with obsolete electronic equipment has grown as an issue as Americans continue to show an endless desire to use these devices at home and at work.

The answer for both organizations and individuals is increasingly to recycle the equipment in order to salvage parts or materials. An important part of the recycling process is the movement of these finished goods from the point of disposal through the recycling channels—a process known as reverse logistics.
Shippers can reduce their costs by developing a greater understanding of logistics and how it relates to recycling.
GETTING IN THE LOOP. Forward logistics is a value-adding process in which manufactured goods move from the point of production to the end user, and the cost is passed onto the consumer. However, companies often view reverse logistics as strictly an unallocated expense.
This perspective inhibits the user from seeing the broader picture and perhaps taking advantage of efficiencies in transportation, warehousing and other aspects of logistics, say some observers.
Among the goals of the parties involved in recycling computers, cell phones, televisions and other equipment that makes up the electronic scrap stream is to make their logistics systems as efficient as possible.
One challenge to reverse logistics in electronics is a shortage of shredding centers, which tends to raise transportation costs. Another is a cost allocation issue common to recyclers in other industries; although the value is different, it will likely cost the same amount to ship different obsolete electronics items whether they are destined for a remarketing center or to a shredding center.
ASSIGNING ROLES. Some electronics recycling companies also act as middle managers in the reverse logistics process. One such recycler is Reclamere Inc., based in Tyrone, Pa. The company specializes in providing a variety of end-of-life services for electronic equipment, such as computers, network infrastructure gear and telecommunications equipment, for medium-sized companies. Says Vice President of Technology and Logistics Angie Keating, "Mid-tier companies usually do not have loading docks, packaging materials or staff to handle recycling themselves. This is a labor-intensive process."
Reclamere provides services related to many parts of the recycling chain, including valuing old equipment for potential recycling; making detailed inventory lists; storage and redeployment; and refurbishing and resale.
A typical scenario involves Reclamere sending staff to an office to pack up and remove equipment. Keating says that one of the main logistics challenges for Reclamere is the cost of transportation. "In rural Pennsylvania, the freight lanes are not the best. Another challenge is the bulkiness of the equipment," she continues. "Computers are odd shaped when it comes to stacking. [Another challenge] is the less organized storage of our customers that we encounter, which complicates the process. Hospitals, banks or other organizations do not always have warehouses for storage of used equipment," she says.
Understanding the nuts and bolts of logistics can help all parties involved in recycling improve their efficiency levels. Bob Glavin, president and CEO of United Recycling Services Inc., an electronics recycler based in West Chicago, Ill., says that with less than truckload (LTL) shipments, the cost of freight is a factor. "The customer always pays freight," he notes. "Those with less volume may hold their goods in order to consolidate them with other shippers’ freight. They know that they can get better rates this way, but a lot of customers do not want to hold their goods. If they have five pallets now and in two months would have 5-½ pallets, they do not see the point of waiting," he says.
|
In addition to transportation, warehousing is one of United Recycling’s services that may also be an important consideration for shippers. For example, a major retailer can send its shipments to United Recycling, which would accumulate them and process them once per month or once per quarter, says Glavin.
For some customers, these services include parts harvesting, in which United Recycling will remove a CD-ROM or Pentium chip, and also rebuild and repackage the equipment. Glavin says that his main logistics challenges are warehousing, packaging, parts removal and managing inventory. "Inventory control is the single most complex aspect. We must keep a sophisticated inventory management system," he says.
Keating says there is an education process associated with electronics recycling and that it is part of Reclamere’s job to make customers aware of the steps involved. "Most shippers do not grasp the concept of reverse logistics sufficiently. The people in charge are often IT (information technology) professionals who have no experience with shipping or materials managers. Even materials managers (who deal with logistics) tend to view used computers as a commodity without considering the shipping requirements of different components," she says.
Keating says while there may be a growing awareness of the need for logistics efficiency on shippers’ parts, there are also a lot of companies allocating space for old computers for which they did not plan disposal.
She adds that many companies view recycling only as a new line item and do not realize that shipping out these old computers could save them money in the long run.
Tips for shippers include providing an accurate inventory of what is to be removed, such as how many CPUs they have, etc. If shippers provide an accurate inventory, they can be paid more for their electronic equipment.
Security of personal information is another important consideration when dealing with electronic equipment. Says Keating, "Although there are few regulations saying what you must do with a computer, there are many that say what you cannot do with personal information. Reclamere focuses on a secure chain of custody."
FINDING THE EFFICIENCIES. Dan Fadgen is vice president of business development at Pharmacy Software Solutions, Inc., a company based in Vernon Hills, Ill., that develops technology platforms for returns management applications. He also has experience with electronics recycling.
Fadgen says that for the past four to five years, companies have been recognizing the benefits of reverse logistics more. "In the past, manufacturers’ entire focus was on outbound distribution. For example, say that items are returned as unsaleable. If the manufacturer has that information, they would be able to consider whether there is a need to produce as much of it. [But] if you are looking just at sales, you do not get the full picture. From the manufacturer to the point of consumption is only 180 degrees," he says.
Glavin says that the area of his business that is generating the most inquiries is equipment redeployment, mostly from larger companies. "Let’s say that a company in Seattle wants to get rid of 500 Pentium computers. United Recycling could erase the hard drive, install a larger one and redeploy the equipment to the company’s Cleveland facility."
Although all shippers may not recognize the benefits of reverse logistics efficiency, some are mapping out their goals based on a cost savings strategy. At the City of Portsmouth (N.H.) Department of Public Works, a new plan for reverse logistics is being implemented.
Silke Sulle, solid waste coordinator, says that her department has found good ways to save costs. "In the past, Public Works would just pick up anything. But now we are starting to see more electronics retailers involved in take back programs for their equipment. The question from the public’s perspective is whether they want the company to do it or [if they want] their tax dollars to go toward equipment collection," she says.
Sulle admits that Portsmouth’s electronics recycling program is in its infancy stage. But, with cost savings as a priority, Portsmouth is about to undergo a new plan for reverse logistics of electronics equipment. Public Works will pay a flat fee to East Coast Electronics Recycling Inc., based in Massachusetts. The company is a subsidiary of Supreme Computer and Electronics Recycling Inc., a licensed recycler based in Lakewood, N.J. East Coast specializes in the environmentally safe removal and recycling of computer and electronic waste.
Convenience is also a benefit of this system, says Sulle. Public Works receives a 16-foot by 8-foot by 8-foot box and may load up to 10,000 pounds during a six week period. The goods do not need to be shrink wrapped because they are stacked directly in the vehicle. Peter Prinze, general manager at East Coast Electronics, says that his customers are looking for low cost, convenience and security. "With our services the customer handles the goods only once. When the box is ready, they call us for a pick up, and we drop a new box for them at the same time," he says.
Previously, Portsmouth would pay a rate per pound, plus a hauling fee. Says Sulle, "Our staff at Public Works would collect pallets in their warehouse, shrink wrap them when they accumulated 16 to 20 of them, and a broker would pick them up. Storage space is an issue, since we don’t have much." The new system will reduce Portsmouth’s charges by at least half, she estimates.
As companies and communities increase their levels of electronics recycling, they are becoming more aware of the need for and the mechanics of efficient logistics. There is an education process involved in electronics recycling in general, and all parties would probably benefit by developing and understanding the process of reverse logistics.
The author is a freelance writer based in Washington, D.C. He can be contacted via e-mail at acoia@verizon.net.
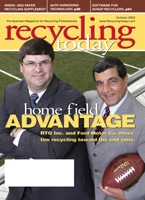
Explore the October 2003 Issue
Check out more from this issue and find your next story to read.
Latest from Recycling Today
- Returpack reports increased DRS activity in Sweden
- Trade groups align against European export restrictions
- Construction, auto sectors show mixed signals
- Politics in Turkey threaten recycled steel outlet
- Toppoint Holdings expands chassis fleet
- Lego creates miniature tire recycling market
- Lux Research webinar examines chemical recycling timetables
- Plastics producer tracks pulse of wire recycling market