
Las Vegas is known for its big hotels, big casinos and big-name entertainment, but Republic Services is putting Las Vegas on the map for another big reason. The Phoenix-based waste services firm’s new Southern Nevada Recycling Center (SNRC) is considered the largest residential single-stream recycling facility in the United States.
The 110,000-square-foot SNRC, next door to Republic’s older, still operational 88,000-square-foot facility, combine to give it the title of the largest residential recycling facility. The SNRC’s advanced sorting technology and innovative design elements further set it apart.
“A recycling center of this magnitude is a bold undertaking and reflects our community’s commitment to environmental responsibility,” Tim Oudman, area president of Republic Services, said at the Nov. 12, 2015, opening of the SNRC.
MAKING THE TRANSITION
The facility’s General Manager Len Christopher says Republic first considered expanding about four years ago and spent some time looking at options and vendors.
As Republic began collecting residential recyclables using automated trucks, volume increased significantly. “We just got to the point where we were at capacity,” he says of the original facility, which was built in 1991.
Republic owned the property adjacent to its original MRF and decided to build its new facility there.
Republic continued processing material at the original MRF “until they could flip the switch and reroute the trucks next door,” Christopher says.

Processing really ramped up at the new facility in January as materials slowly transitioned from the old complex to the new complex. Christopher says Republic Services took its time to work out the required adjustments.
He describes the new processing system, designed and installed by San Diego-based CP Group, as much more efficient than the older system. Within three years, the new facility will be fully automated and operating at an estimated 70-ton-per-hour processing rate, according to Christopher.
“We didn’t jump out the gate at 70 tons per hour,” he says.
Christopher says he expects the new MRF to process 175,000 tons in 2016. “We are hoping to get that number up to about 250,000 tons in about three years.”
The SNRC was built primarily to process residential single-stream recyclables, which Christopher says make up about 80 percent of the incoming volume, with commercial and industrial recyclables account for the remaining 20 percent.
TIP TOP
The facility receives about 125 truckloads of material per day, 99 percent of which are delivered by Republic Services’ trucks.
Christopher says commercial, industrial and residential materials are kept separate from each other on the tipping floor because they are processed at different speeds. “We can run the residential faster than the commercial,” he adds.
Materials are weighed and held in a certain area of the tipping floor before being fed into metering bins, which create an even burden depth so that when the material is conveyed to the presort deck, the sorters easily can identify items that are not supposed to be in the loads, such as residuals or large items, and can remove them by hand.
Next, a series of screens separates the fiber, sorting it into various grades. A postsort of the fiber is conducted at the end of this process to check for contaminants.
The containers travel on to magnets that pull out steel and tin cans, and eddy current separators recover aluminum cans.
An optical sorter separates polyethylene terephthalate (PET) from high-density polyethylene (HDPE), and a split unit further separates HDPE into mixed color and natural streams.
Nos. 3-7 plastics also are recovered.
As with the fiber, postsorts of these streams are performed, removing contaminants by hand.
Glass stays in the glass cleaning system.
The entire system is controlled using a Panasonic Tough Book, which Christopher describes as a tablet similar to an iPad but more durable. It has been a welcome addition to the operation.
“It allows us to control anything and everything you can imaging in the facility,” he says, “whether we want to empty a bunker, turn on a baler, speed a belt up, slow it down, reverse it, you name it. Pretty much anything and everything a machine can do, we can control it from a hand-held device, so it’s really great from a supervisory standpoint that we can walk and monitor and make adjustments on the fly.”
Christopher says the tablet is more efficient than the old way of making adjustments by relaying information via walkie-talkie to someone at the control panel.
Also contributing to efficiency improvements at the new SNRC are the single-level platforms, which Christopher says increase the ability to supervise employees because they are all visible.
“It is much safer that way,” he adds.
As well, catwalks were built from each office directly to the deck, so employees don’t have to go down to ground level to access the system.
The SNRC employs 160 people and runs two processing shifts and an overnight maintenance shift.
UP FOR THE CHALLENGE
After materials are separated through the SNRC’s CP system, they are conveyed to bunkers prior to being baled and moved to a warehouse. From there, materials are sold into their various markets.
Prices for recycled commodities may be down, but Christopher says he isn’t worried about the short-term outlook.
“When you make an investment like this, you can’t look at what is going on today,” he says.
“In the past 10 years, we’ve had a lot of ups and downs. The good news is we continue to sell products and move products, and eventually we hope to see markets get a little bit stronger,” Christopher says.
“We just keep doing what we are doing, and when the price goes up, that’s good,” he adds.
Republic Services’ extensive footprint in southern Nevada extends beyond its newest recycling facility. The company also operates its largest landfill and its largest transfer station in the area.
Christopher says it is his job to “keep stuff away from them.”
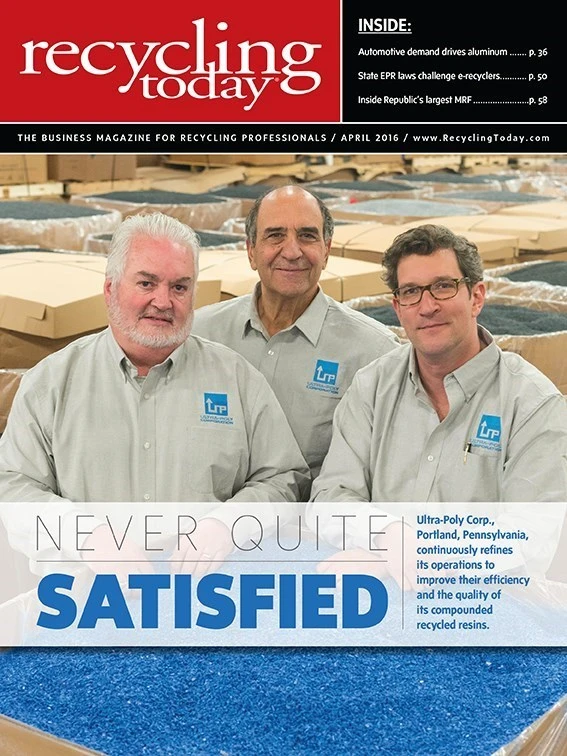
Explore the April 2016 Issue
Check out more from this issue and find your next story to read.
Latest from Recycling Today
- AF&PA report shows decrease in packaging paper shipments
- GreenMantra names new CEO
- Agilyx says Styrenyx technology reduces carbon footprint in styrene production
- SABIC’s Trucircle PE used for greenhouse roofing
- Hydro to add wire rod casthouse in Norway
- Hindalco to invest in copper, aluminum business in India
- Recycled steel price crosses $500 per ton threshold
- Smithers report looks at PCR plastic’s near-term prospects