Recovering copper and aluminum from wire and cable scrap is an activity with a long history. Some methods for processing this material that were being used in the 1960s and earlier are still in use today, while others have fallen out of favor or have been prohibited outright.
Before it was recognized as environmentally unsound and potentially harmful to workers, open burning or burning in furnaces with unfiltered emissions was one way to address larger amounts of cable and wire.
Starting in the late 1960s, furnaces became more widespread. Those that were equipped with scrubbers and other emissions controls or could be retrofitted with such controls are still in occasional use today.
Simply stripping the plastic coating from the wire and cable and cutting the metal into shippable lengths was also a traditional way of processing this material. Smaller amounts of cable are still processed this way.
Throughout much of the 20th century, alligator shears (to cut cable into manageable lengths) and hand tools accomplished much of the work in a relatively labor-intensive manner.
Between labor-intensive stripping and environmentally questionable burning, when Kansas City recycler Larry Mallin decided to steer his family business into wire and cable processing in 1964, he refers to it on his company’s Web site as "entering the ‘then new and unpopular’ wire chopping industry."
The write-up at www.MallinBrothersCompany.com continues, "At the time, burning the insulation off the wire was the only way to recycle and recover the metal. Larry thought that with wire chopping, the company would make processing much easier and even enhance the value of the wire. Finally, in 1968, Mallin Brothers Co. Inc. became one of the first wire chopping facilities in the nation."
NOWAs with so many other recycling endeavors, the benefits of automation can be seen in how wire and cable processing can be accomplished today.
Large-volume wire and cable processors in North America today feed material into automated size reduction and sorting equipment that yields clean, pure chops of copper and aluminum (such as those from Shine Bros. Corp. in the 2004 photo above), as well as sometimes-recyclable plastic products.
Size-reduction equipment deployed includes high-volume shredding machines made by companies like France’s MTB.
Mallin Brothers Co. is among those companies deploying an MTB machine, a BDR 2400 model that it says "not only increases production, but also generates a more uniform feed into our granulation lines. This creates greater capacity and higher quality finished products."
The company’s volume and the shredder’s ability to work at high speeds means Mallin Brothers starts off by feeding its system with an excavator equipped with a grapple. That’s a long way from "stacking loose burned wire by hand on pallets for shipments," which Larry Mallin says was the industry’s standard practice several decades ago.
Separation has kept up with higher-speed shredding with a variety of equipment choices available to wire and cable recyclers, including vibrating screens, gravity separation tables and magnetic and electro-static separation equipment.
Automation cannot entirely replace human experience and knowledge, it should be pointed out. At wire chopping locations such as Mallin Brothers, "All incoming wires undergo rigorous screening and sorting. Everything that is entered into our process has been visually checked for quality by one of our team members," the company states on its Web site. "Inspection continues through the recycling process and past the finished product."
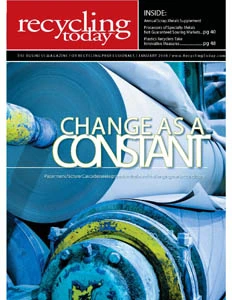
Explore the January 2008 Issue
Check out more from this issue and find your next story to read.
Latest from Recycling Today
- Nucor receives West Virginia funding assist
- Ferrous market ends 2024 in familiar rut
- Aqua Metals secures $1.5M loan, reports operational strides
- AF&PA urges veto of NY bill
- Aluminum Association includes recycling among 2025 policy priorities
- AISI applauds waterways spending bill
- Lux Research questions hydrogen’s transportation role
- Sonoco selling thermoformed, flexible packaging business to Toppan for $1.8B