THEN
Torches with cutting power provided by acetylene, propane, argon or oxygen gas; iron or aluminum powders; or compressed air (and combinations of these elements) have long provided an image of activity at a scrap yard.
Crews of torch cutters have helped scrap company owners downsize and dismantle objects as large as decommissioned war ships and as common as beams just a little too thick or lengthy to be introduced into processing machinery.
In his "Handbook of Recycling Techniques," Dutch recycler and writer Alfred Nijkerk spells out both the many applications and the limitations of torch cutting in the scrap environment.
According to Nijkerk, the use of acetylene torches dates back to the early 19th century, although scrap recyclers are not known to have used them until around the early 20th century.
Throughout the first half of the 20th century as open hearth furnaces welcomed iron and steel scrap as a feedstock, torches helped dismantle and downsize large obsolete items into pieces that could "pass through the relatively narrow furnace mouth," according to Nijkerk.
Steel beams, rail cars and ships all proved to be ideal candidates to face the cutting torch, which Nijkerk says, "remained the most important scrap processing method until around the 1960s."
Torches remain on the job in scrap yards, with companies like Eddie’s Welding Supply of Stafford, Texas, providing the Victor Bulldog line and other torches to scrap recyclers.
But some of the tasks once performed by torch cutters proved suitable for mechanical equipment such as small, alligator shears.
Other lengthy metal objects could be introduced into hydraulic guillotine shears, possibly whole or possibly after being cut once by a torch cutter. By the 1960s, scrap recyclers could do the math to determine whether to buy a large shear or to retain sizable torch-cutting crews.
NOW
The 1970s brought about an innovation that has had a lasting impact on the torching-vs.-shearing equation: the mobile hydraulic shear.
LaBounty Manufacturing (now a part of The Stanley Works) is credited by Nijkerk as having introduced mobile shears to the scrap market in the 1970s.
Initially, demolition contractors were predominant buyers, and the steel beam scrap they often generate was the most common material cut by these shears.
In the past 30-plus years, however, the markets for mobile shears and the number of applications for them have grown considerably.
Currently one of the most competitive sectors in the recycling equipment market, several manufacturers have introduced a wide range of shear sizes, configurations and outright variations on shearing that have combined to give the mobile shear an expanded presence at scrap yards and demolition sites around the world.
Shears can be seen at demolition sites attached to high-reach cranes, chewing through beams that formerly would have been brought to the ground courtesy of a wrecking ball and then been torched into smaller pieces, either to be transportable or to be furnace- or guillotine shear-ready.
At both demolition sites and scrap yards, shears closer to the ground prepare material when and where it is most logical at a high production rate relative to torch cutting. The safety of mobile shears compared to torch cutting (with its volatile gases) has also gained favor with recyclers.
Mobile shears are now found even at ship-breaking operations, and the range of sizes of available shears allows them to be used attached to the largest scrap handlers as well as with skid steer loaders for smaller tasks.
Torches still have their uses in scrap yards for some beams, plates and large objects. Mobile shears, however, are performing some of the same tasks that were formerly accomplished by torch cutters.
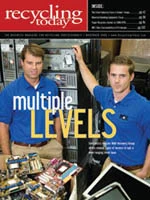
Explore the November 2008 Issue
Check out more from this issue and find your next story to read.
Latest from Recycling Today
- NWRA announces 2025 Driver of the Year, Operator of the Year winners
- The Scrap Show: Nanci Schuld of FE Trading Group LLC
- Call2Recycle Canada partners with RLG to advance battery collection
- Report delves into recovery opportunities for food-grade polypropylene
- Reimagining Supplier Payments in Metal Recycling: A Digital Leap Forward
- STEINERT Lithium Battery Detection and Removal from Waste Streams
- Driving the Future: Innovations in Waste & Recycling Technology
- Robin Wiener recognized for recycling leadership