THEN
The lead-acid battery has been a recyclable item for decades, but the way end-of-life batteries are handled has changed dramatically during that time.
Knowledge that over-exposure to lead or virtually any exposure to corrosive acid is harmful seems well entrenched, but in the early days of scrap recycling the safe handling of lead was not a given.
The extent to which at least one veteran scrap recycler dismissed concerns could be heard in the comment of an attendee of an ISRI (Institute of Scrap Recycling Industries Inc.) Roundtable event in the late 1990s, who ventured that since lead was a natural substance and part of the environment, he was not convinced that exposure to it was harmful.
The U.S. EPA’s level of concern about lead exposure can be seen in its summary report on a former battery breaking facility in Berks County, Pa., that became a designated Superfund site.
A 1983 report summarizing what the EPA found at the 10-acre site notes, "This facility was in operation from 1961 until 1971, during which time lead was reclaimed from auto/truck batteries. The procedure consisted of dumping the acid, crushing the battery casings and separating the lead."
Potential harm was more than theoretical, as the site in 1983 included three residences, and storm runoff from the site could drain into the Schuylkill River watershed.
As for the site’s residents, the EPA report states, "Elevated levels of lead were found in the blood of four children residing on site as reported by the Pennsylvania Department of Health. The Centers for Disease Control concurred with the Pennsylvania Department of Health and strongly recommended immediate action to remove this potential and possible/actual public health threat."
Whether batteries were sawed, sheared or crushed, throughout much of the 20th century the process was at times taking place in locations without adequate protection from direct contact and without adequate ventilation for lead dust or acidic mist that was created.
NOW
Automobile dismantlers, recyclers and others seeking advice on how to safely handle lead-acid batteries can now tap into that knowledge at several sources, including the Web site of the U.S. Occupational Safety & Health Administration (OSHA).
For the most part, dismantlers and recyclers handling those batteries are no longer doing any processing and instead are shipping the batteries to smelting facilities with highly automated systems into which large investments have been made to ensure safety and environmental compliance.
At such a facility, according to OSHA, "Used batteries are usually received in palletized containers and can either be stored or transferred to conveyors for shredding. These are normally low-exposure operations."
One of the melting facilities handling a considerable number of automotive batteries is run by Canada’s Newalta, which purchased the Nova Pb plant in Quebec in 2007.
A video at Newalta’s Web site, www.newalta.com, touts the company’s strict compliance with Canadian and U.S. environmental regulations, and its operation of a laboratory as well as a manufacturing plant that are ISO audited and certified.
Water used at the plant (as well as rainwater falling on site) is treated at the company’s own water treatment plant. Water is continually reused in the on-site industrial process, with lead contaminants removed from any water that does finally leave the site.
Newalta keeps the air clear through a multi-stage process designed to protect workers and prevent harmful emissions. Newalta says highly sophisticated equipment treats gasses and releases steam free of toxic substances at the end of the process.
Companies like Newalta have found that strict compliance can have upfront and ongoing costs, but those are necessary costs of doing business when handling lead-acid batteries.
Get curated news on YOUR industry.
Enter your email to receive our newsletters.
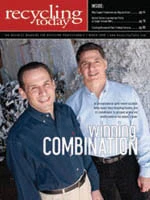
Explore the March 2009 Issue
Check out more from this issue and find your next story to read.
Latest from Recycling Today
- Freepoint Eco-Systems receives $50M loan for plastics recycling facility
- PET thermoform recycling the focus of new NAPCOR white paper
- Steel Dynamics cites favorable conditions in Q1
- Hydro starts up construction in Spain
- Green Cubes unveils forklift battery line
- Rebar association points to trade turmoil
- LumiCup offers single-use plastic alternative
- European project yields recycled-content ABS