THEN
When I first had any association with the scrap metal business I was a very young lad. Long ago, I remember my grandfather sitting on a box scraping the insulation off copper wire with a knife. My, my, how things have changed!
A lot of the differences are in the cost of operating. The cost of labor, insurance, fuel and equipment was much less years ago. Companies did not need that much equipment. Labor was plentiful and operators tried to pay a living wage, but there were few benefits involved.
Social Security costs were reasonable. Insurance, workers’ compensation—everything that had to do with running a business—was within reach financially.
The investment for storing inventory was not as costly either, and the material itself did not cost as much. Copper scrap was 20 cents per pound. Brass was 12 cents; aluminum was 6 or 7 cents, and steel scrap was $15 or $20 per gross ton.
Furthermore, banks were always there to help reliable customers. There was not a problem with getting a loan to carry you through slow times.
Today operating costs are extremely high. Years ago, most operations were non-union. Today, owners are competing in some respects with steel mills and automotive and manufacturing sectors that have very high hourly rates for employees.
Now the benefit costs are extremely high. Offering health insurance, retirement plans and 401(K)s are expensive. Insurance today is a huge budget item within the operations overhead, and includes workers’ compensation, auto insurance and equipment fleet insurance.
Additionally, the equipment needed today to operate is extremely costly, and therefore the investment in building and maintaning a plant ties up many dollars. The innovation of auto shredders, big shears and cranes, as well as front-end loaders and bulldozers to move the material has become a huge investment. Material handling has became much more efficient, but at a very high cost.
NOW
As of early 2009 there is little money for banks to lend to businesses. Another major difference is the decline in the number and types of domestic consumers for each item of material. Now, domestic consumers are scarce. Remaining brass and bronze ingot makers are just a few, and the consumers of aluminum scrap are consolidated.
Brass mills are, for the most part, gone in the U.S. The European market also has difficulty competing with China or India for nonferrous scrap.
Even the domestic steel mills have a difficult time, including the mini-mills that have to buy steel scrap to compete with export markets.
When colleagues ask, "What can be done to keep my business going?" I do not have an answer. This is a very different period of recession from what our industry has ever gone through.
What will happen, hopefully, with the economic stimulus package is that there will be road and bridge repairs that will create scrap. A new infrastructure to support green power would also create scrap. Production of new equipment and changeovers in factories with newer and modern machines can also create scrap.
The bad news is that new manufacturing processes are almost inevitably more efficient, so that scrap production will be less than it was in the past. Manufactured scrap will be in very short supply domestically and worldwide.
We do not know if the stimulus programs will create the jobs needed. Demolition and construction will definitely create scrap, but the overheads of scrap companies must be cut in some way.
Whether the workforce can be maintained with lower hourly rates or benefit packages or whether there will be changes in health insurance and other benefits remains to be seen. There may be a lot of concessions that need to be made to stimulate our business to be profitable once more. I hope it will happen.
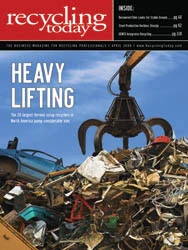
Explore the April 2009 Issue
Check out more from this issue and find your next story to read.
Latest from Recycling Today
- EMR adds electric material handler to its Becker, Minnesota, operations
- Greenwave Technology pares back losses in Q3
- Lindner shredders prepare Brazilian plastic for recycling
- China ups steel output, while other nations cut back
- ReElement, Posco partner to develop rare earth, magnet supply chain
- Comau to take part in EU’s Reinforce project
- Sustainable packaging: How do we get there?
- ReMA accepts Lifetime Achievement nominations