The business models associated with collecting and processing end-of-life electronics appear very different at first glance, but in fact they share the same fundamental goal. That goal is to maximize the value of intact items for resale, recover components for resale and/or recover commodities for recycling. These valuations, however, are not made in a vacuum, but must be measured relative to the costs of handling and processing different items using different means.
There are several approaches to consider when studying this recycling segment. Businesses can be set up in many different ways to accomplish this goal, as can the recycling plants, or material recovery facilities (MRFs), where the work will be done.
COLLECTIONS DEPARTMENT. The simplest approach to the electronics recycling business is to collect end-of-life electronics and to have others do the processing. This model has been adopted, for example, by some established companies in the hazardous waste industry.
These companies have municipal contracts to provide household hazardous waste collection services for various municipalities. Typically, during designated dates and times, residents bring consumer-generated hazardous waste to one or more collection points where the waste is properly handled and ultimately properly destroyed or disposed of by the contracting company.
Recognizing opportunity, some of these organizations have offered their contracted communities electronics recycling collection services. In some cases they have not gone into the electronics processing business, but simply deliver the electronic scrap collected during collection events to processors approved by them through an internal auditing process.
DISMANTLING. For a time, when the electronic recycling industry was in its infancy, the phrase, "Every company with a screwdriver calls itself an electronics recycling processor," was an apt definition of the state of affairs.
This has now evolved to the next simplest approach to the business (and the model adopted by the vast majority of those in the business) of handling end-of-life electronics based on what I call the retail end of the business. Here, the electronics recycling processor provides local (and to some extent regional) collection of electronics recycling combined with some manual (vs. automated) processing.
Glass Half-Full |
The companies involved in CRT processing and recycling are part of the wholesale side of the electronics recycling processing business, meaning that they not only serve local markets, but also receive entire tractor trailer loads of monitors and televisions or CRTs from retail processors or large generators.A CRT tube consists of the panel, which is what you see when you look at a monitor or television. This is a thick piece of CRT glass with a chemical coating on the inside that reacts to electrons beamed at it and may be made of leaded or unleaded glass. The funnel portion of a CRT is a funnel-shaped piece of glass ending at the thin end with a cylindrical-shaped stainless steel component, which is an electron gun.
Funnel glass is always leaded and is also coated on the inside. Basically, the images we see result from electrons being beamed at the coating on the back of the CRT panel in very specific patterns. Panel glass and funnel glass are connected by a frit, a high lead-content material used to bind the two parts of a CRT together.
Today, there are three primary techniques for processing CRT glass. One method is to prepare CRT glass for use in a glass-melting furnace to make new CRTs. This requires sorting the leaded panel from the unleaded panel glass and keeping both separate from the funnel and frit, which can be recycled together. For glass-to-glass recycling, not only must the different types of glass be sorted, but also all chemical coatings must be removed.
Because this process is difficult, only a very small number of entities are currently involved in glass-to-glass CRT recycling. This method of recycling is further complicated by the shrinking market share of CRTs vs. flat screen panels. Consequently, fewer furnaces are melting CRT glass, resulting in a much lower domestic demand. However, export demand for properly prepared CRT glass does continue to make this business a viable electronics recycling business model.
The second method of CRT recycling is for the CRT glass to go to a lead smelter. Primary lead smelters can use the CRT glass in either their blast furnace operations or in their sintering operations. The CRT glass is used for both its lead content and for its silica content. This use of CRTs has led to our next electronics recycling business model. Here, some processors have set themselves up to be very efficient in the hand dismantling of monitors and televisions and receive these not only from local markets but, on a wholesale basis of whole tractor trailers from other retail electronics recycling processors or large generators.
The CRT glass is prepared for the lead smelter by breaking it in an automated and environmentally sound manner that contains the lead dust and automatically removes the shadow mask (a piece of ferrous metal inside a CRT) from the glass. Also adhering to a very similar business model are entities that have automated equipment to, in an environmentally sound manner, shred whole monitors and televisions as well as other types of electronic scrap and automatically separate the glass from the ferrous metals, nonferrous metals and plastic. The ultimate value of the materials making up televisions and monitors tends to make business models involving them regional in nature because of the transportation costs involved. The third electronics recycling business model related to end-of-life monitors is to refurbish the monitors into small televisions. In developing nations there is a constant demand for cheap, small-sized televisions. Cheap, for obvious reasons and small sized because of the size of the homes they are destined for. This has lead to a niche market for a small number of entities that purchase monitors on a wholesale basis and produce televisions from them. |
The retail electronics recycling processor relies upon its ability to provide prompt, reliable and efficient pick-up service to businesses, institutions and government offices and typically also provides collection services for municipal events.
Retail electronics recycling processors tend to price their services on a retail basis and, because they provide premium and customer-specific services, they are typically in the higher end of the pricing spectrum for those services.
After making pickups at various businesses and institutions, retail electronics recycling processors make handling and processing decisions for the full spectrum of end-of-life electronics, including everything you can imagine, plus some you cannot.
The fun now begins as, for each item, the retail electronics recycling processor begins the real moneymaking decisions.
Question No. 1 is usually the most obvious: "Can I resell this item without doing any work except that associated with marketing it as an intact unit?" If the answer is yes, unless there was a re-sale stipulation by the generator, it probably will be re-sold.
If the answer is no, Question No. 2 is asked: "Is it economically viable to repair this item and re-sell it as an intact item?" If yes, so be it.
If no, Question No. 3 is asked: "Is it economically viable to remove certain components from this item and re-sell them to component after-markets?"
Electronics recycling processors sell intact products and components using a multitude of markets. Many have retail showrooms where the public can shop for used items and components. Most use e-Bay and other specialized Web-based stores, and many components are sold in bulk through brokers, ultimately finding their way into products being manufactured overseas.
Of course, it is impossible for the electronics recycling processor to re-sell everything that comes in the door. After the re-sale of products and components, left are the final end-of-life products and components that need to be recycled, not as reusable items, but for the value of the materials they are made of.
Again, the electronics recycling processor has to make decisions concerning each item or type of item. The prime question emerges: "Is it economically viable for me to hand-dismantle this item into its various materials or should I send it to a more specialized processor?"
My experience indicates that many choose to send end-of-life monitors and televisions to processors specializing in the recycling of products containing cathode ray tubes (CRTs). The reasons for this appear to be twofold. One, the inherent value of the materials in a monitor or television is low relative to their size and weight. Two, the glass in CRTs contains lead and requires specialized handling.
Still, some electronics recycling processors choose to hand-dismantle their monitors and send intact or broken CRTs to a specialized processor.
At the other end of the value spectrum is the end-of-life electronics recycling that does not contain CRTs, consisting mostly of metal and plastic.
There are robust markets for most materials found in end-of-life electronics. Markets for nonferrous metal, ferrous metal, printed circuit boards, insulated wire and copper-bearing material (from such things as power supplies, small motors, etc.) can all be found in the United States and Canada.
The retail electronics recycling processor will either hand-dismantle these products or sell intact products or components to others for dismantling. Such decisions are made based upon the perceived value of the dismantled commodities vs. the labor to dismantle the product, and based upon experience, guess work or the more mundane facts of business, such as space and labor availability.
It should be noted that many components that fall in the lower end of the value spectrum (i.e., keyboards and other smaller components) end up being exported to areas where labor costs are lower than in North America.
Baled plastic from the casings of end-of-life electronics currently also enjoys robust markets. However, markets for electronics recycling plastic are primarily overseas for many reasons.
The plastic from end-of-life materials consists of many different resins. Some of these components may contain added materials such as fire retardant compounds. Economically, the different resin types are not typically sorted in the United States, but can be sorted where the cost of labor is much lower and where health and safety standards may not be as stringent as they are in the United States.
NATIONWIDE.The final model to be discussed in this article is what is referred to as the "national player."
The national player may or may not have multiple locations but is characterized by the fact that their business model is, to a large extent, based on doing business at the wholesale level.
These recycling companies receive incoming products from a variety of sources, including retail electronics recycling processors, Fortune 500 companies with multiple nationwide locations and/or large government entities. These electronics recyclers are usually specialized processors of CRTs or other products using automated methods.
There appear to be a number of successful business models for electronics recycling processors. The electronics recycling processor operating what I refer to as a retail type business using manual dismantling methods, though limited in growth by local demographics and competition, should remain a vibrant part of this industry.
Because of the environmental aspects of processing CRTs, the specialized monitor, television and CRT processors with their more automated approach to processing will be in constant demand for years to come. As in any other service industry, there will be the national players, vying for the volume potential that comes from doing business with national entities.
Like any relatively young industry, there are many business models associated with electronics recycling processing. For this effort, I have touched only on those that have thus far garnered the most volume.
Like any recycling based business, higher volumes result in lower per-unit operating costs and the opportunity to use higher levels of automation, further reducing operating costs.
The competition for growth is on the incoming side of the business, not on the sale of components or commodity side. Those that are successful will be successful because they can attract more business through their procurement efforts.
For the future, I turn to the "crystal monitor" and see the following:
• The actual number of processors servicing any given geographic area will tend to go down via consolidation of businesses and attrition as business flows into the hands of the most efficient operators.
• Consolidation on a regional or national level will occur as specialized processors with automated processing systems seek high volumes of materials. As volumes go up, their per-unit processing costs go down, allowing them to reach further for materials.
One avenue for controlling volume is to vertically integrate backwards to purchase local retail-type electronics recycling processor, as this is where the volume will actually come from.
• Consolidation for consolidation’s sake, as happened in the solid waste business in the 1970s and 1980s (and to some extent in the recycling industry in the 1990s), is likely.
Certain investors may believe that by owning a large number of previously locally based electronics recycling operations, they will be able to provide standardized operating procedures and to consolidate overhead functions, therevy being rewarded with the proper return on their investments.
Looking at the history of two different recycling industries, I see a common thread that may foretell much about the future of the electronics recycling processing business.
Consider the traditional scrap metal processing industry, which has been with us since the dawn of the industrial age, and the relatively new business of processing municipally generated fiber, bottles and cans. The most successful operators in both of these areas are those with the lowest per-unit operating costs and the highest levels of automation, a fact electronics recyclers should note.
The author is vice president of RRT Design & Construction, a Melville, N.Y.-based provider of design/build and operations management services to the recycling and solid waste industries.
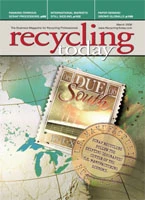
Explore the March 2006 Issue
Check out more from this issue and find your next story to read.
Latest from Recycling Today
- Radius experiences sixth consecutive quarterly loss
- US ferrous market exhibits upward pricing pressure: Davis Index
- Glass Packaging Institute applauds regulation change
- Engcon adds to Tiltorotator line
- Paper recycling is focus of two January webinars
- Disruption likely for material flows in mid-January
- Blue Whale Materials to expand Oklahoma lithium-ion battery recycling plant
- CARI names new president and CEO