
The Prairie Lakes Municipal Solid Waste Authority (PLMSWA), a joint powers agreement between Becker, Clay, Otter Tail, Todd and Wadena counties, owns and operates the Perham Resource Recovery Facility (PRRF), Perham, Minnesota. The PRRF was built in 1986 and originally owned by Otter Tail Power Co. Subsequently, the city of Perham owned and operated the PRRF before transferring ownership to the PLMSWA in June 2011.
The PRRF receives and processes approximately 60,000 tons per year of municipal solid waste (MSW) from the five counties and consists of a material recovery facility (MRF), combustion units, waste heat boilers, steam generators and air pollution control (APC) equipment. The PRRF combusts approximately 45,000 tons of material annually and produces steam, which is sold to local customers. It also can generate electricity as needed by the Otter Tail Power Co.
In 2014 a MRF was added at the front end and the waste-to-energy (WTE) facility was retrofitted, adding a second boiler and additional APC equipment. The PRRF’s MSW processing capacity increased from 116 tons per day (TPD) to 200 TPD. These changes allowed the PRRF to process more waste from the region while increasing overall recycling rates, produce more steam for its customers and reduce the use of an existing natural-gas-fired auxiliary boiler for meeting normal steam demand.
PLMSWA aimed to reduce landfilled material to no more than 15 percent of total MSW generated in the region by 2030.
Serving a dual purpose
The authority contracted RRT Design & Construction, a Melville, New York-based systems integrator and engineer/constructor of solid waste processing facilities, to design and construct the MRF, which has two main functions: improving the characteristics of incoming MSW by removing noncombustible materials and undesirable waste prior to feeding PRRF combustors and recovering recyclables.
The MRF’s major equipment included a trommel, eddy current separator, balers, magnetic belt separators, sorting stations and various conveyors. Automation would be applied where possible and manual sorting techniques would be limited to high-value recyclables and removal of undesirable waste for the combustors that could be recycled instead.
The MRF was designed to recover ferrous metals, nonferrous metals, old corrugated containers (OCC) and plastics for recycling. The system also removes undesirable waste, such as e-scrap and fines, including glass and grit. The remaining material is conveyed to the refuse pit and used as fuel for the WTE plant.
The process starts on the tipping floor, where bulky materials are removed. The rest of the MSW is conveyed to a sorting station, where other bulky items (rejects) and clean OCC are removed. Sorters also remove unprocessable items, such as propane tanks, electronics, batteries and wires, all of which are recycled.
The waste then enters a trommel, which opens trash bags and also separates materials into three streams: unders, middlings and overs. A screen further processes the unders, with material larger than 1 inch being conveyed to the main process line. Material less than 1 inch enters an air classifier, which recovers light materials and feeds them to the main process line. Heavies are compacted and landfilled.
Middlings are transported via a series of conveyors and are exposed to a belt magnet and an eddy current separator for the recovery of ferrous and nonferrous metals, respectively. The oversized materials combine with the middlings and are discharged to a second sorting station to remove rejects missed in the first sorting station and to recover additional recyclables. This combined stream is then exposed to another magnet to recover more ferrous metals.
The MRF diverted 18 percent of the total MSW received in 2015 from the facility’s combustion units. The recovered recyclables amounted to nearly 3 percent of the total waste received.

The PRRF combusted nearly 40,000 tons of MSW in 2015—27 percent more than in 2012. While the amount of waste processed is related partially to the MRF addition, the main reason is because of the increased WTE capacity. The combusted material’s quality also was improved.
Effects on MSW quality
The MRF manipulates incoming waste for combustion by removing OCC, ferrous and nonferrous metals, fines and rejects (material of no heating value). Although the MRF recovers corrugated cardboard that has relatively high BTU properties, it also removes much of the noncombustible matter (glass, metals and electronic scrap) and high-moisture organic waste.
The average heating value of the MSW processed after the MRF addition has increased more than 20 percent, largely because the MRF removes noncombustible material and reduces moisture content. The refuse-derived fuel (RDF) the MRF produces generates more than 16 percent more steam at a higher energy density compared with unprocessed MSW.
The RDF allows the WTE plant to produce the same amount of steam (51,500 pounds per hour) at lower feed rates (7.7 tons per hour versus 6.4 tons per hour). Notable, however, is the added cost to operate the MRF.
The MRF realized several operational and cost benefits and is a complementary addition to the community’s overall MSW management approach and the WTE plant’s infrastructure. Although every plant is unique, these results suggest this approach can add value elsewhere.
Get curated news on YOUR industry.
Enter your email to receive our newsletters.
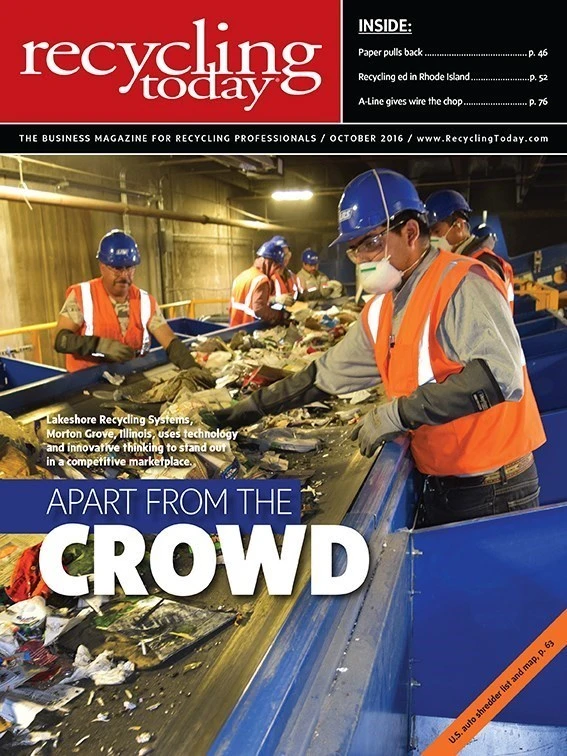
Explore the October 2016 Issue
Check out more from this issue and find your next story to read.
Latest from Recycling Today
- Hitachi forms new executive team for the Americas
- Southwire joins Vinyl Sustainability Council
- Panasonic, Sumitimo cooperate on battery materials recycling in Japan
- Open End Auto Tie Balers in stock, ready to ship
- Reconomy names new chief financial officer
- ICIS says rPET incentives remain weak
- New Jersey officials award $16.2M in annual recycling, waste reduction grants
- Linder Industrial Machinery announces leadership changes